-
-
News
News Highlights
- Books
Featured Books
- smt007 Magazine
Latest Issues
Current IssueIntelligent Test and Inspection
Are you ready to explore the cutting-edge advancements shaping the electronics manufacturing industry? The May 2025 issue of SMT007 Magazine is packed with insights, innovations, and expert perspectives that you won’t want to miss.
Do You Have X-ray Vision?
Has X-ray’s time finally come in electronics manufacturing? Join us in this issue of SMT007 Magazine, where we answer this question and others to bring more efficiency to your bottom line.
IPC APEX EXPO 2025: A Preview
It’s that time again. If you’re going to Anaheim for IPC APEX EXPO 2025, we’ll see you there. In the meantime, consider this issue of SMT007 Magazine to be your golden ticket to planning the show.
- Articles
- Columns
Search Console
- Links
- Media kit
||| MENU - smt007 Magazine
Value Stream Mapping: Operationalizing Lean Manufacturing
October 14, 2015 | Erwin Patrocinio, Integrated Micro-Electronics Inc.Estimated reading time: 2 minutes
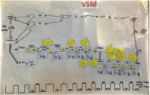
In the realm of electronics manufacturing services, EMS providers are continuously fraught with pressures from the original equipment manufacturers (OEMs) to lower the total cost of production.
One of the tools used by EMS companies to achieve this goal is value stream mapping (VSM). VSM is a lean manufacturing technique used to document, analyze and improve the flow of information or materials required to produce a product or service. It provides optimum value to the customer through a complete value creation process with minimum waste in design (concept to customer), build (order to delivery), and maintenance (in-use through life cycle to service). Through VSM, the EMS provider maximizes the customer gains by adhering to a clear vision and implementing a clear plan connecting all improvement activities.
The VSM is a visualization tool that has its origin in the Toyota version of lean manufacturing (Toyota Production System). Through this tool, inherent wastes or losses within an operation are identified. The value stream maps reflect a broad view of the process, usually from external supplier to an external customer at a given facility.
Many of the problems that the VSM exposes reach across organizational lines of responsibility and expertise. The goal of the process is to identify, demonstrate and decrease those activities that do not add value to the production process.
By applying VSM, EMS providers can have a clearer picture of multiple processes involved in a work flow, identify waste and its sources, identify where change is required, standardize the process, and identify potential problems that could be encountered in the future state. It can also be used as a tool for planning as well as for managing changes. The VSM process helps make organizations more efficient by improving their processes. Let’s see how VSM is applied in an EMS environment.
The illustration below is an example of how a VSM project is done. The workshop typically runs for several days depending on the complexity of a certain project under study, while project closure is targeted within six months.
Pre-work is being done prior to the learning session and workshop. This includes gathering and analysis of business operations information, important production details and current performance. The line walk helps in gathering more information and shows the actual scenario of production where team members do line observation in each process and take notes.
This forms part of the actual mapping process. And like any other improvement discipline, the VSM project has its own project charter that states the project timeline, estimated benefits and other project information.
Editor's Note: This article originally appeared in the October 2015 issue of SMT Magazine.
Suggested Items
Siemens to Bring Advanced Timing Constraint Capabilities to EDA Design Flow with Excellicon Acquisition
05/19/2025 | SiemensSiemens has entered into an agreement to acquire Excellicon to bring its best-in-class software for the development, verification, and management of timing constraints to Siemens’ EDA portfolio of software for IC design
Revolutionizing Inspection With Delvitech
05/19/2025 | Nolan Johnson, SMT007 MagazineRoberto Gatti, CEO of Delvitech, shares insights into its Horus machine, a revolutionary innovation in AI-driven inspection technology. This unique system leverages five patented optical heads and custom cameras to perform high-speed, precise inspections. With capabilities that extend beyond traditional limitations, the Horus machine seeks to transform inspection in electronics and microelectronics, as well as the food and pharmaceutical industries, showcasing the versatility and power of its AI-native technology.
It’s Only Common Sense: The Importance of Setting Realistic Expectations
05/19/2025 | Dan Beaulieu -- Column: It's Only Common SenseWhether dealing with customers, employees, or stakeholders, setting and managing expectations can make or break relationships, trust, and long-term success. Below are the reasons it’s critical to set realistic expectations and how doing so can bolster your business's credibility.
I-Connect007 Editor’s Choice: Five Must-Reads for the Week
05/16/2025 | Nolan Johnson, I-Connect007My picks for the week include—as a complement to the trade agreement news—SEMI's public support of a bill including new tax credit eligibility for semiconductor manufacturers. This provision feels quite similar to the current PCB investment bill that's been introduced to the current Congress; here’s hoping Congress takes a more holistic approach to electronics manufacturing.
NCAB Acquires 100% of B&B Leiterplattenservice GmbH in Germany
04/23/2025 | NCABNCAB has signed an agreement to acquire 100 percent of B&B Leiterplattenservice GmbH (B&B) headquartered in Mittweida, west of Dresden. The company had net sales of around 150 MSEK in 2024 within the PCB trading with an EBITA exceeding SEK 20 million.