-
- News
- Books
Featured Books
- smt007 Magazine
Latest Issues
Current IssueSupply Chain Strategies
A successful brand is built on strong customer relationships—anchored by a well-orchestrated supply chain at its core. This month, we look at how managing your supply chain directly influences customer perception.
What's Your Sweet Spot?
Are you in a niche that’s growing or shrinking? Is it time to reassess and refocus? We spotlight companies thriving by redefining or reinforcing their niche. What are their insights?
Moving Forward With Confidence
In this issue, we focus on sales and quoting, workforce training, new IPC leadership in the U.S. and Canada, the effects of tariffs, CFX standards, and much more—all designed to provide perspective as you move through the cloud bank of today's shifting economic market.
- Articles
- Columns
- Links
- Media kit
||| MENU - smt007 Magazine
Streamlining PCB Assembly and Test NPI with Shared Component Libraries
November 16, 2015 | Pat McGoff, Mentor GraphicsEstimated reading time: 3 minutes
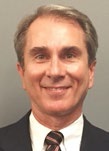
PCB assembly designs become more complex year-on-year, yet early-stage form/fit compliance verification of all designed-in components to the intended manufacturing processes remains a challenge. So long as librarians at the design and manufacturing levels continue to maintain their own local standards for component representation, there is no common representation in the design-to-manufacturing phase of the product lifecycle that can provide the basis for transfer of manufacturing process rules to the design level. A comprehensive methodology must be implemented for all component types, not just the minority which happen to conform to formal packaging standards, to successfully left-shift assembly and test DFM analysis to the design level and thus compress NPI cycle times. The elements of such a solution include implementing de-facto standards for package and pin-type classifications, as well as DFM analysis rules that are associated with these classifications and the intended manufacturing processes. The resulting solution enables the transfer of DFM rules from the manufacturing process expert to the design and NPI engineers on the design side responsible for verifying manufacturing-process compliance of new product designs.
This paper will demonstrate the technological components of the working solution: the logic for deriving repeatable and standardized package and pin classifications from a common source of component physical-model content, the method for associating DFA and DFT rules to those classifications, and the transfer of those rules to separate DFM and NPI analysis tools elsewhere in the design-through-manufacturing chain, resulting in a consistent DFM process across multiple design and manufacturing organizations. Following establishment of a common source of component definitions and classifications, rules-based generation of assembly- level machine libraries is enabled from the same source that drove the DFM process, resulting in right-first-time launch of a new product into the manufacturing process.
The principles of lean manufacturing, “getting it right first time,” and minimizing waste and unnecessary manual interaction, are all familiar and generally accepted as contributing factors toward cost reduction and quality maximization. In that context, this paper will examine two specific engineering-process aspects of introducing a new PCB design into assembly manufacturing and the technical barriers to be overcome to make the processes as lean as possible.
The two engineering processes to be discussed are:
1. Performing design-for-assembly (DFA) verification on a new product design, as early as possible in the product lifecycle, and in any case before transferring the design into manufacturing.
2. Preparing assembly-line machine library content for fast set-up.
Before getting into the technicalities of the two topics and how they are related, it is worth first considering the business environment of PCB manufacturing. It is now about 20 years since PCB assembly manufacturing began to be outsourced in a major way, with the resulting rapid growth of the now well-known EMS and contract manufacturers. Before the outsourcing revolution, when design and manufacturing operations were generally vertically integrated, it was common to see CAD/CAM engineering processes being set up and maintained by electronics OEMs, depending for their success on internally defined library standards, a specific and relatively narrow range of manufacturing processes, and plenty of in-house proprietary software to link it all together. By contrast, today’s challenge is to take full advantage of the outsourcing opportunity, the choice, the flexibility, and the cost-competitiveness, without losing the advantage through engineering-process inefficiencies related to discontinuities in CAD/CAM software, data flows, and libraries between the customer (the design organization) and the suppliers (the manufacturers). To make matters worse, the typical manufacturer of today will serve dozens, if not hundreds, of design-customers, and the design organization may use dozens of EMS providers. This many-to-many interface between design and manufacturing tends to drive engineering processes toward standardized “lowest common denominator” workflows that are relatively manual, error-prone, and slow. These workflows are certainly somewhat “standard”, but they are far from lean, in terms of minimizing waste and maximizing consistency through automation.
The two engineering processes described in this paper are specifically designed to enable a high degree of production-portability between a product’s design organization and multiple manufacturing facilities and processes.
Editor's Note: This article originally appeared in the November 2015 issue of SMT Magazine.
Testimonial
"In a year when every marketing dollar mattered, I chose to keep I-Connect007 in our 2025 plan. Their commitment to high-quality, insightful content aligns with Koh Young’s values and helps readers navigate a changing industry. "
Brent Fischthal - Koh YoungSuggested Items
Mentor Graphics Polska Sp. z o.o Merge into Siemens Industry Software Sp. Z.o.o.
11/03/2021 | Mentor GraphicsMentor Graphics Polska Sp. z o.o plans to merge into Siemens Industry Software Sp. Z.o.o. in the first quarter of 2022. Therefore, the companies have jointly agreed on a Terms of Merger of Companies.
If It's My Data, I Can Do What I Want, Right?
05/04/2017 | Michael Ford -- Column: The Essential Pioneer's Survival GuideIn the light of the new IoT philosophies that are rapidly becoming the expectation, the problem of flexibility versus risk is resolved on the lower level, as IoT establishes the transfer and availability of data everywhere without the need for "hacking" into internal system database structures.
The Building Blocks of Industry 4.0
04/21/2017 | Kevin Decker-Weiss, CircuitByteAt the recent IPC APEX EXPO, Kevin Decker-Weiss, director of sales at CircuitByte, joins panellist from Mentor Graphics and EMS firm Saline Lectronics in a roundtable on the building blocks of Industry 4.0 hosted by Scoop. Here is his take on that panel and the show.
Sales and Marketing in a Digital Transformation Reality
12/21/2016 | Jay Gorajia, Mentor Graphics Corp.While many of the common sales and marketing best practices apply to the PCB assembly industry, however, deep manufacturing and electronics design expertise is required to truly drive customer interactions from one-off transactions into long and sustaining relationships as the industry goes through rapid change such as the larger involvement of a younger generation in the workforce, and the move to digital transformation and smart manufacturing.
December 2016 Issue of SMT Magazine Available Now
12/02/2016 | I-Connect007The December 2016 issue of SMT Magazine examines the myriad challenges facing sales and marketing execs in the PCB assembly industry.