-
- News
- Books
Featured Books
- design007 Magazine
Latest Issues
Current IssueAll About That Route
Most designers favor manual routing, but today's interactive autorouters may be changing designers' minds by allowing users more direct control. In this issue, our expert contributors discuss a variety of manual and autorouting strategies.
Creating the Ideal Data Package
Why is it so difficult to create the ideal data package? Many of these simple errors can be alleviated by paying attention to detail—and knowing what issues to look out for. So, this month, our experts weigh in on the best practices for creating the ideal design data package for your design.
Designing Through the Noise
Our experts discuss the constantly evolving world of RF design, including the many tradeoffs, material considerations, and design tips and techniques that designers and design engineers need to know to succeed in this high-frequency realm.
- Articles
- Columns
- Links
- Media kit
||| MENU - design007 Magazine
Beyond Design: Stackup Planning, Part 4
November 19, 2015 | Barry Olney, In-Circuit DesignEstimated reading time: 1 minute
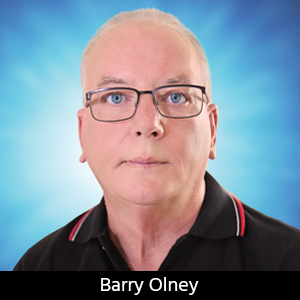
In this final part of the Stackup Planning series, I will look at 10-plus layer counts. The methodology I have set out in previous columns can be used to construct higher layer-count boards. In general, these boards contain more planes and therefore the issues associated with split power planes can usually be avoided. Also, 10-plus layers require very thin dielectrics in order to reduce the total board thickness. This naturally provides tight coupling between adjacent signal and plane layers reducing crosstalk and electromagnetic emissions.
In high-speed digital designs, transient ground currents are the primary source of both unwanted noise voltages and radiated emissions. In order to minimize these emissions, the impedance of the ground should be minimized by reducing the inductive loop area. Inductance is directly proportional to the length of the conductor, so keep the loop area as short as possible.
To minimize inductance, two conductors (signal traces or ground planes) that carry current in the same direction should be separated. However, two conductors that carry current in the opposite direction (such as signal and ground planes or power and ground planes) should be positioned as closely as possible. Both these cases also help eliminate crosstalk.
Here are some additional rules for high-speed design:
- Use multiple ground planes, where possible, rather than power planes, in the stackup to isolate signal layers.
- Place stitching ground vias close to every signal transition (via) to provide a short current return path.
- Spread numerous ground stitching vias around the board to connect the multiple ground planes through a low impedance path.
- Don’t use ground pours on signal layers as this reduces the impedance of nearby traces. If you must, in order to balance copper, separate the signal and pour by 20 mils.
If power planes are used as reference planes, then the return current must transverse stitching capacitors in order to jump between ground and power planes. The current flowing through these stitching capacitors will create a voltage drop across them. These voltages may radiate adding to system noise problems.
To read this entire column, which appeared in the October 2015 issue of The PCB Design Magazine, click here.
Suggested Items
Happy’s Tech Talk #40: Factors in PTH Reliability—Hole Voids
07/09/2025 | Happy Holden -- Column: Happy’s Tech TalkWhen we consider via reliability, the major contributing factors are typically processing deviations. These can be subtle and not always visible. One particularly insightful column was by Mike Carano, “Causes of Plating Voids, Pre-electroless Copper,” where he outlined some of the possible causes of hole defects for both plated through-hole (PTH) and blind vias.
Trouble in Your Tank: Can You Drill the Perfect Hole?
07/07/2025 | Michael Carano -- Column: Trouble in Your TankIn the movie “Friday Night Lights,” the head football coach (played by Billy Bob Thornton) addresses his high school football team on a hot day in August in West Texas. He asks his players one question: “Can you be perfect?” That is an interesting question, in football and the printed circuit board fabrication world, where being perfect is somewhat elusive. When it comes to mechanical drilling and via formation, can you drill the perfect hole time after time?
The Evolution of Picosecond Laser Drilling
06/19/2025 | Marcy LaRont, PCB007 MagazineIs it hard to imagine a single laser pulse reduced not only from nanoseconds to picoseconds in its pulse duration, but even to femtoseconds? Well, buckle up because it seems we are there. In this interview, Dr. Stefan Rung, technical director of laser machines at Schmoll Maschinen GmbH, traces the technology trajectory of the laser drill from the CO2 laser to cutting-edge picosecond and hybrid laser drilling systems, highlighting the benefits and limitations of each method, and demonstrating how laser innovations are shaping the future of PCB fabrication.
Day 2: More Cutting-edge Insights at the EIPC Summer Conference
06/18/2025 | Pete Starkey, I-Connect007The European Institute for the PCB Community (EIPC) summer conference took place this year in Edinburgh, Scotland, June 3-4. This is the third of three articles on the conference. The other two cover Day 1’s sessions and the opening keynote speech. Below is a recap of the second day’s sessions.
Day 1: Cutting Edge Insights at the EIPC Summer Conference
06/17/2025 | Pete Starkey, I-Connect007The European Institute for the PCB Community (EIPC) Summer Conference took place this year in Edinburgh, Scotland, June 3-4. This is the second of three articles on the conference. The other two cover the keynote speeches and Day 2 of the technical conference. Below is a recap of the first day’s sessions.