-
- News
- Books
Featured Books
- pcb007 Magazine
Latest Issues
Current IssueInventing the Future with SEL
Two years after launching its state-of-the-art PCB facility, SEL shares lessons in vision, execution, and innovation, plus insights from industry icons and technology leaders shaping the future of PCB fabrication.
Sales: From Pitch to PO
From the first cold call to finally receiving that first purchase order, the July PCB007 Magazine breaks down some critical parts of the sales stack. To up your sales game, read on!
The Hole Truth: Via Integrity in an HDI World
From the drilled hole to registration across multiple sequential lamination cycles, to the quality of your copper plating, via reliability in an HDI world is becoming an ever-greater challenge. This month we look at “The Hole Truth,” from creating the “perfect” via to how you can assure via quality and reliability, the first time, every time.
- Articles
- Columns
- Links
- Media kit
||| MENU - pcb007 Magazine
Estimated reading time: 5 minutes
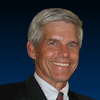
All About Flex: Embracing the Mess
Marketing in the world of printed circuits is an important discipline, but I have learned it is better to be prepared with a nimble reaction than to expect the marketing department to consistently be successful in predicting the future. The path to the goal is often achieved much more quickly by making an early decision followed by a course correction rather than waiting for all the information. Several related factoids characterize the markets for flexible circuits and flexible heaters:
- We live in a world of “time based competition.” Being faster to market can be more profitable than being better.
- Customers’ needs many times don’t fit within the supplier’s existing/proven/Six-Sigma capabilities.
- Technology and markets move quickly, rewarding suppliers that respond rapidly.
- Customers give suppliers money to figure things out.
The myriad of electronic applications drive flexible circuit product configurations and constructions spanning broad engineering imaginations. Circuits that require controlled impedance push trace widths down, and copper thicknesses increasingly thinner, with .0007” copper a common specification. These applications also tend to drive film substrates thicker to increase separation distance between signals and ground planes. Circuitry intended to carry heavy current pushes copper the opposite direction, sometimes involving metal thicknesses in excess of .010”. These circuits tend to stretch the definition of the word flexible.
Product configuration selections can also involve adding copper layers to make multilayer structures, plating multiple surface treatments for solder pads vs. switch contact regions, attaching selective stiffeners for mechanical and component support, and orientation of copper grain to properly orient circuit traces in applications requiring dynamic flexing. Requirements for optimizing component attachment create an additional complexity dimension as nesting circuits for material usage competes with assembly panelization requirements. These seemingly endless permutations of “want to have” vs. “need to have” requirements can drive mushrooming product features, untested manufacturing processes, and unique routing sequences. It can tax the creativity of the best product and applications engineers. What a mess!
But it is a wonderful mess. Complexity makes sourcing parts overseas, across multiple time zones and language barriers, a very risky proposition. The world of flexible circuit manufacturing involves custom engineered parts with unique performance requirements. Every application is different. The kiss of death on most any part number is when someone states the circuit is a “no brainer.” When I hear this, it is generally time to get material ready for a restart. In an attempt to deal with the mess, the manufacturer is tempted to “standardize” their offering, often defined by comfortable or existing manufacturing capabilities. Isn’t the solution to stop building the oddball parts? Or define a niche product offering so resources can be focused? Maybe, but the business world is littered with companies that have disappeared because they were too restrictive in their willingness to change. Attempting to put in systems or procedures to deal with the complexity is noble, and existing procedures always deserve challenge, but new rules and procedures should be considered as part of a continuous improvement project rather than an end state. Change takes us out of our comfort zone, it is difficult…and often it is absolutely necessary.
Page 1 of 2
More Columns from All About Flex
All About Flex: Terms and ConditionsAll About Flex: ISO 9001 Basics
All About Flex: FAQs on UL Listings for Flexible Circuits
All About Flex: Avoiding Trace Fracturing in a Flexible Circuit
Polyimide vs. Silicone for Flexible Heaters
All About Flex: Copper Thickness Requirements for Flex Circuits
All About Flex: Copper Grain Direction
All About Flex: Options for Purchasing Flexible Heaters