-
-
News
News Highlights
- Books
Featured Books
- smt007 Magazine
Latest Issues
Current IssueIntelligent Test and Inspection
Are you ready to explore the cutting-edge advancements shaping the electronics manufacturing industry? The May 2025 issue of SMT007 Magazine is packed with insights, innovations, and expert perspectives that you won’t want to miss.
Do You Have X-ray Vision?
Has X-ray’s time finally come in electronics manufacturing? Join us in this issue of SMT007 Magazine, where we answer this question and others to bring more efficiency to your bottom line.
IPC APEX EXPO 2025: A Preview
It’s that time again. If you’re going to Anaheim for IPC APEX EXPO 2025, we’ll see you there. In the meantime, consider this issue of SMT007 Magazine to be your golden ticket to planning the show.
- Articles
- Columns
Search Console
- Links
- Media kit
||| MENU - smt007 Magazine
Low-Temperature Thick Film Pastes Permit Lead-Free Soldering
December 8, 2015 | Steven Grabey, Heraeus ElectronicsEstimated reading time: 2 minutes
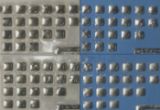
New technologies in the printed electronics industry have fostered an increased interest in low-temperature polymer thick film products. Industry expectations are demanding that low-temperature products perform at the same level as their high-temperature counterparts, including high reliability, strong adhesion, and solderability with lead-free solders.
Much of the shift to lead-free solders is due to environmental concerns and legislation that has surfaced over the past 15 years. Traditionally, it has only been possible to use leaded solders for soldering to polymer-based thick film conductors. While using lead-free solders is beneficial both to the industry and the environment, they pose challenges during processing. The high temperatures required for lead-free soldering generate a harsh environment that is too severe for polymer thick film pastes to survive.
Using New Substrates
As the electronic industry moves towards flexible electronics, they are realizing the benefits in using substrates such as treated glass and aluminum that require a low-temperature-processing, polymer thick film. These materials not only offer a cost-effective approach to building complex, integrated circuits, they also provide a viable option to manufacturers dealing with the new demands of substrates that cannot handle temperatures higher than 500°C.
Polymer thick film materials have the versatility to be engineered depending on substrate and preferred application method such as screen printing, stencil printing, dispensing, dipping, and roll-to-roll printing. For traditional thick film materials, additive processing has always offered benefits including ease of use, simple design changes, and the ability to manufacture patterns from simple circuits to intricate designs.
The addition of polymer thick film to this category not only continues to have these listed advantages but also brings new gains such as: low temperature processing, quick-curing steps, and the ability to offer many of the same benefits as high-temperature thick film material without the need for the traditional firing step.
Despite the known advantages for polymer thick film materials, they are not as widely accepted in the industry as equivalent alternatives to their standard high-temperature thick film counterparts. This is due to two disadvantages – reliability and process-ability – prevalent in polymer thick films. Although many polymer thick films are considered to be reliable, they do not have the typical life span of a cermet (ceramic-metal) paste.
It is difficult to use lead-free solders when working with polymer materials. Frequently, the processing temperatures of the solders are greater than those of the polymers used to create the conductive pastes. This leads to the leaching of the conductive materials and the poor wetting of the solder.
To solve these problems, a new polymer thick film paste has been developed that is compatible with a variety of substrates and readily accepts lead-free solder. This easy-to-process paste features low temperature curing (150°C – 200°C); offers excellent solderability with SAC305 solder; and is RoHS- and REACH compliant. It allows conductive polymer pastes to be used in a variety of functions such as position sensors, low-temperature heater applications, and tempered-glass connection points.
This article will present data that shows how the thick film paste was assessed under various parameters including solder acceptance, adhesion, and thermal and SEM analysis.
Editor's Note: This article originally appeared in the December 2015 issue of SMT Magazine.
Suggested Items
KYZEN to Focus on Aqueous Cleaning and Stencil Cleaning at SMTA Juarez
05/20/2025 | KYZEN'KYZEN, the global leader in innovative environmentally responsible cleaning chemistries, will exhibit at the SMTA Juarez Expo and Tech Forum, scheduled to take place Thursday, June 5 at the Injectronics Convention Center in Ciudad Jarez, Chihuahua.
Koh Young Installs 24,000th Inspection System at Top 20 EMS
05/14/2025 | Koh YoungKoh Young, the global leader in True 3D measurement-based inspection and metrology solutions, proudly announces the installation of its 24,000th inspection system at a Top 20 Global EMS in Thailand.
Indium’s Karthik Vijay to Present on Dual Alloy Solder Paste Systems at SMTA’s Electronics in Harsh Environments Conference
05/06/2025 | Indium CorporationIndium Corporation Technical Manager, Europe, Africa, and the Middle East Karthik Vijay will deliver a technical presentation on dual alloy solder paste systems at SMTA’s Electronics in Harsh Environments Conference, May 20-22 in Amsterdam, Netherlands.
SolderKing Achieves the Prestigious King’s Award for Enterprise in International Trade
05/06/2025 | SolderKingSolderKing Assembly Materials Ltd, a leading British manufacturer of high-performance soldering materials and consumables, has been honoured with a King’s Award for Enterprise, one of the UK’s most respected business honours.
Knocking Down the Bone Pile: Gold Mitigation for Class 2 Electronics
05/07/2025 | Nash Bell -- Column: Knocking Down the Bone PileIn electronic assemblies, the integrity of connections between components is paramount for ensuring reliability and performance. Gold embrittlement and dissolution are two critical phenomena that can compromise this integrity. Gold embrittlement occurs when gold diffuses into solder joints or alloys, resulting in mechanical brittleness and an increased susceptibility to cracking. Conversely, gold dissolution involves the melting away of gold into solder or metal matrices, potentially altering the electrical and mechanical properties of the joint.