-
- News
- Books
Featured Books
- smt007 Magazine
Latest Issues
Current IssueSupply Chain Strategies
A successful brand is built on strong customer relationships—anchored by a well-orchestrated supply chain at its core. This month, we look at how managing your supply chain directly influences customer perception.
What's Your Sweet Spot?
Are you in a niche that’s growing or shrinking? Is it time to reassess and refocus? We spotlight companies thriving by redefining or reinforcing their niche. What are their insights?
Moving Forward With Confidence
In this issue, we focus on sales and quoting, workforce training, new IPC leadership in the U.S. and Canada, the effects of tariffs, CFX standards, and much more—all designed to provide perspective as you move through the cloud bank of today's shifting economic market.
- Articles
- Columns
- Links
- Media kit
||| MENU - smt007 Magazine
Innovative New Uses for Ceramic Column Grid Arrays from TopLine
December 18, 2015 | Andy Shaughnessy, I-Connect007Estimated reading time: 8 minutes
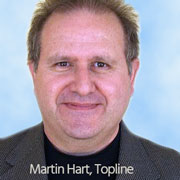
TopLine President and CEO Martin Hart sat down to discuss his paper on ceramic column grid arrays (CCGA) at the recent SMTA International show in Chicago. Hart begins by explaining the relationship between CCGA and ball grid arrays (BGA), and TopLine's drive to find new uses for CCGA.
Andy Shaughnessy: Martin, why don't you start by giving us a little background on CCGAs.
Martin Hart: The best way to talk about CCGAs is to reference their cousin, the BGA. Everybody is familiar with BGA—ball grid arrays. Few people realize that the CCGA, the ceramic column grid array, was actually invented about ten years before the first BGA. When BGA first came out, they were invented by Bell Laboratories; a full ten years after columns had already been in the field. The main purpose of having a column instead of a solder ball is to extend reliability. You get more temperature cycles out of a solder column because it will absorb the CTE mismatch between the materials of ceramic and substrate, such as an FR-4 PC board.
Shaughnessy: We just don't hear much about CCGA. Everybody seems to have settled on the BGA and flip chips and various other sorts of packaging. Why did the CCGA fall out of favor?
Hart: That's a good question. BGAs are lower cost and much easier to assemble. During the manufacturing process, attaching a solder ball is significantly easier than attaching a column. Solder balls roll and self-center onto the BGA pads. Columns are difficult to attach to the pads. They don't self-center because they are held rigidly in place, usually by a graphite tool, during the column attach process. Columns can easily get bend if handled incorrectly.
Shaughnessy: You have to literally stand this thing up.
Hart: You have to stand the column straight up during the attachment of the column to the substrate.
Shaughnessy: It sounds very risky, in a way.
Hart: There is an element of risk, but it’s more of a situation of having a correct manufacturing process. Your process has to be dialed to effectively use column grid arrays. Once you have a process in place, then CCGA seems to work well.
Shaughnessy: What is the new use that you seem to have found for them?
Hart: First I’ll tell you the traditional places where column grid arrays are used. Traditionally, they've been used in defense, military, aerospace and also in high-value computing. One new area is down-hole drilling, where you have electronics going down several miles. It's very hot as you go below the earth’s surface. There is also interest in specialized automotive where you have electronics in the firewall. Also, columns can be are found in some medical. Not medical implants in a human body, but in medical equipment. There is a benefit to use CCGA wherever you have a large ceramic package, and mounted on an FR-4 board or a polyimide board. CCGA is more reliable when the temperature swings dramatically.
If you have a very small ceramic, it's safe to use a BGA. I've researched and wrote some tables and calculations showing when it is safe to use a ceramic BGA and when you must use a CCGA. A small 15 mm square ceramic BGA will not cause any problem with solder ball delamination. But if you start to go larger, say a 35 mm square, 40 mm square, 45 mm or even larger, 50 mm square, then solder balls will delaminate. That will effectively create a catastrophic failure in the equipment.
I also want to point out that your equipment does not even have to be electrically switched on. Say, if your equipment is turned off, sitting in storage, then if you have a large ceramic part mounted with solder balls on an FR-4 board, then that equipment might fail. If your equipment is out in the elements experiencing alternating hot and cold temperatures, then your equipment might fail if it contains large ceramic BGA components. When the sun goes down, temperatures might drop -25 to -40°. And when the sun comes up temperatures might rise 100-125°. Just sitting in the box, you'll see the phenomenon of delamination with large ceramic BGA components.
Shaughnessy: What led you to focus more on CCGA?
Hart: The original business of TopLine was to manufacture process development kits of all kinds of parts, from BGA and QFP in a kit form with circuit boards. Customers, particularly in mil-defense, were asking for column grid arrays so they could perform their own process development. This has gone on for a number of years and we decided, "Okay, we need to jump in and address this market of producing CCGA and solder columns."
Shaughnessy: I guess CCGA would have its own completely different process.
Hart: Yes, it does. The process of attaching a column onto a ceramic substrate is totally different than attaching solder balls to a BGA. CCGA requires a graphite fixture to hold the column upright at a 90° angle. It involves having a controlled reflow process. We found that vapor phase reflow ovens are best solution because your maximum temperature is fixed. You can also use a twelve-zone oven, but you have to have that oven profile really dialed to attach solder columns.
Shaughnessy: How tall is this column?
Hart: Oh, good question. Traditionally, columns are 2.2 mm high. There's nothing totally magical about 2.2 mm high. Columns have been made 1.27 mm, which is 50 mills. Columns have been made bigger in diameter and smaller in diameter. IBM set the standard years ago with studies and of papers showing that 2.2 mm, is a good column height. The industry settled ever since. The secret is actually in the attachment process. You start with a longer column and then trim it down to 2.2 mm during the planarization process. After all the columns are attached in an array, you literally have to cut the columns shorter to planarize them. So you wind up with 2.2 mm, but you start off with a column that is 2.3 mm, up to 2.5 mm, in order to wind up with 2.2mm.
Page 1 of 2
Testimonial
"Advertising in PCB007 Magazine has been a great way to showcase our bare board testers to the right audience. The I-Connect007 team makes the process smooth and professional. We’re proud to be featured in such a trusted publication."
Klaus Koziol - atgSuggested Items
Integrated Solutions for Board-level Reliability: A Smarter Path Forward
08/27/2025 | Alan Gardner, MacDermid Alpha Electronic SolutionsIn today’s electronics manufacturing landscape, reliability is no longer just a benchmark but a business imperative. As industries such as automotive, aerospace, and high-performance computing (HPC) push the boundaries of innovation, the demand for dependable board-level performance under extreme conditions has never been greater.
ZESTRON Expands Capabilities with Addition of the EPS by i-Tech AG 75 Pallet Cleaning System
08/26/2025 | ZESTRONZESTRON, the global leader in high-precision cleaning solutions and services, is excited to announce the addition of a new capability in its Technical Center in Manassas, VA:
Pick and Place Machine Innovator - NECTEC Launches Next-Gen SMT Line Solution With LED and X-ray Technology
08/26/2025 | Globe NewswireNECTEC PTE. LTD., a leading provider of SMT electronics manufacturing equipment, announced the official launch of its next-generation SMT solutions, featuring newly upgraded pick and place machine, specialized LED pick and place machines, enhanced Reflow Oven technology, advanced X-ray Inspection, high-speed X-ray Counter, and premium Solder Paste
MS2 Technologies, LLC/P. Kay Focuses on Central America with First Installation in Honduras
08/24/2025 | P. Kay Metal, Inc.This year MS2 Technologies has turned their focused to the growing electronics market in Central America. With that focus came the adaptation of MS2 and the Akila System from a Honduras-based corporation with manufacturing plants in both Honduras and Mexico.
BEST Inc. Provides High-Reliability BGA Reballing and Component Rework Services
08/22/2025 | BEST Inc.BEST Inc., a leader in electronic component services, is pleased to announce its component rework services are available for all types of area array devices including ball grid array, land grid array and quad flat no-lead SMT packages.