-
- News
- Books
Featured Books
- design007 Magazine
Latest Issues
Current IssueAll About That Route
Most designers favor manual routing, but today's interactive autorouters may be changing designers' minds by allowing users more direct control. In this issue, our expert contributors discuss a variety of manual and autorouting strategies.
Creating the Ideal Data Package
Why is it so difficult to create the ideal data package? Many of these simple errors can be alleviated by paying attention to detail—and knowing what issues to look out for. So, this month, our experts weigh in on the best practices for creating the ideal design data package for your design.
Designing Through the Noise
Our experts discuss the constantly evolving world of RF design, including the many tradeoffs, material considerations, and design tips and techniques that designers and design engineers need to know to succeed in this high-frequency realm.
- Articles
- Columns
- Links
- Media kit
||| MENU - design007 Magazine
DownStream Takes on Data Documentation Management
December 21, 2015 | Andy Shaughnessy, PCB Design007Estimated reading time: 3 minutes
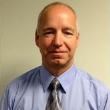
Most PCB designers love their jobs. But designers will also tell you that as much as they enjoy laying out the board, they dislike the final data documentation step, which often involves various formats, including handwritten notes. Enter DownStream Technologies, a company founded 14 years ago to address the challenges related to post-processing the design. Senior Product Marketing Manager Mark Gallant recently discussed the company’s efforts to take the pain out of data documentation, even as data becomes more complex.
Andy Shaughnessy: Why don’t you start out by giving us a little background about DownStream.
Mark Gallant: DownStream Technologies was founded in January 2002 by former PADS Software executives who acquired the assets of Advanced CAM Technologies—products with the brand name CAM350—from Innoveda prior to its acquisition by Mentor Graphics. The newly formed executive team chose the name DownStream Technologies to reflect their goal of delivering technology focused on the “downstream” phase of the PCB design process. Specifically, it’s technology to help bridge the chasm between PCB design and PCB manufacturing domains.
At the time of DownStream’s founding, the predominant method of transitioning a PCB design to manufacturing involved post-processing a design to extract multiple files. Each file was independent of the other in format and content, and disjointed from the original design from which they were derived. What we call the “traditional” process for handoff to manufacturing worked well enough to take us from the days of PCB design by light table up to the start of the 21st century. However, as technology continued to evolve in complexity and market windows to profitability continued to shrink, the traditional process led to higher costs, lower quality and ultimately delayed time to market.
Our founders believe the transition from virtual design to the manufacture of the physical product could be, and should be, improved. We observed this trend in several of our early adopter customers—organizations that were the first to implement new technologies and processes which, once proved out, led to adoption by the rest of the market. To reduce manufacturing delays, these early adopters educated themselves on the PCB manufacturing process. Their newfound knowledge led them to introduce DFM analysis and single file design exchange into their new product introduction process. This revised approach, rather than the “hand it over the wall and hope” method, resulted in significant time-to-market gains. Fundamentally, they were shifting their attention from “upstream” processes to refocus on “downstream” processes, shifting from how a design is created to how it is to be manufactured. The trend of refocusing on manufacturing and a belief that DFM tools and singular design exchange files were evolving from “nice to do” to “must do” was the catalyst for the creation of DownStream. Since our start we have introduced a full suite of DFM analysis, PCB documentation, and assembly panel design tools.
Shaughnessy: What are your customers’ biggest demands when it comes to their new product design process?
Gallant: In the world of electronic product development, and specifically PCB design, the demand is clear: a successful, error-free transition from design to manufacturing. Many of our customers believe the transition process from design to manufacturing is the next frontier of time-to-market gains. Their focus is no longer just faster PCB design, which emphasizes and prioritizes the design phase of new product development. Instead the trend is towards PCB design and manufacturing, and giving equal weight to design and manufacturing. The question, then, is why is this happening, and why now?
Looking back from today’s vantage point, it is an obvious and necessary direction. Electronics manufacturers always list time to market, cost and quality as top priorities in new product introduction. Be the first to market, produce it at the lowest cost, and provide the highest quality. To be successful, the manufacturing process and its many issues, requirements and challenges must be minimized before production begins.
The demands from this new focus on the transition of design to manufacturing are to support a new downstream-focused engineering process, develop or enhance our tools to analyze designs for “manufacturability” issues, and support industry standard, intelligent design exchange file formats that drive the entire manufacturing process for new products.
To read this entire article, which appeared in the November 2015 issue of The PCB Design Magazine, click here.
Suggested Items
GlobalFoundries to Acquire MIPS to Accelerate AI and Compute Capabilities
07/09/2025 | GlobalFoundriesGlobalFoundries announced a definitive agreement to acquire MIPS, a leading supplier of AI and processor IP. This strategic acquisition will expand GF’s portfolio of customizable IP offerings, allowing it to further differentiate its process technologies with IP and software capabilities.
LITEON Technology Reports Consolidated June Sales of NT$13.6 Billion, Up 16% Y-o-Y
07/08/2025 | LITEON TechnologyLITEON Technology reported its June consolidated revenue of NT$13.6 billion. Thanks to the growth from power management in cloud computing, advanced server, and networking, the revenue is up 2% M-o-M, 16% Y-o-Y. The cumulative sales for January to June totaled NT$76.8 billion, up 24%, Y-o-Y.
Inside Aimtron’s Cross-border EMS Strategy
07/08/2025 | Nolan Johnson, SMT007 MagazineMukesh Vasani immigrated from a very small farming village in India to the U.S. in 1995 as a civil engineer. After shifting into electronics, Mukesh built his Chicago-based company, Aimtron, into a successful enterprise by combining quality with competitive pricing. He leveraged his roots in India to expand manufacturing without compromising on quality.
Be the Partner Engineers Can Rely On
07/08/2025 | Nolan Johnson, SMT007 MagazineGreen Circuits’ unique niche in the electronics manufacturing industry comes partly from its location in Silicon Valley, but also from its specialty of serving up quick-turn prototypes and low-volume work with high-complexity production. In this conversation, CEO Michael Hinshaw emphasizes the value of end-to-end services, especially while the pace of R&D development is accelerating amidst a growing demand for complexity across industries.
Electronics Industry Wrestles with Cost Pressures and Weaker Profitability
07/07/2025 | Global Electronics AssociationElectronics manufacturers are facing rising material and labor costs according to the Global Electronics Association’s June Sentiment of the Global Electronics Manufacturing Supply Chain Report.