-
- News
- Books
Featured Books
- pcb007 Magazine
Latest Issues
Current IssueSales: From Pitch to PO
From the first cold call to finally receiving that first purchase order, the July PCB007 Magazine breaks down some critical parts of the sales stack. To up your sales game, read on!
The Hole Truth: Via Integrity in an HDI World
From the drilled hole to registration across multiple sequential lamination cycles, to the quality of your copper plating, via reliability in an HDI world is becoming an ever-greater challenge. This month we look at “The Hole Truth,” from creating the “perfect” via to how you can assure via quality and reliability, the first time, every time.
In Pursuit of Perfection: Defect Reduction
For bare PCB board fabrication, defect reduction is a critical aspect of a company's bottom line profitability. In this issue, we examine how imaging, etching, and plating processes can provide information and insight into reducing defects and increasing yields.
- Articles
- Columns
- Links
- Media kit
||| MENU - pcb007 Magazine
Whelen & IPS: A Strategic Partnership—A Winning Combination
November 4, 2015 | Bryan Bernas, I-Connect007Estimated reading time: 3 minutes
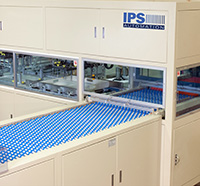
Integrated Process Systems, Inc. (IPS) is a manufacturer of automated wet process equipment and material handling systems in Cedar City, Utah. IPS was formed in June of 1996 with a philosophy of being a multi-product, multi-industry company. In 1996, IPS purchased the assets of VCM for its vertical process equipment, and in 2000, purchased the assets of Western Technology Associates Inc. (WTA) for its horizontal process equipment and VRP technology. The result is the establishment of IPS as a state-of-the-art product line that offers a turnkey solution to all wet process and material handling requirements.
Of the 39 suppliers Whelen chose to use, none were as integral to the automation and overall design and layout of the line as IPS, with its team led by President Mike Brask. In February 2014, IPS approached Whelen at a very early stage, to put the required infrastructure in place before any of the equipment could be installed. This involved the design and installation of al the overhead utilities: the blower on the roof for exhaust, the process piping, as well as all the Unistrut framing (yellow and green for Mike’s favorite Green Bay team—a playful jibe for a factory located in the heart of New England Patriot territory). IPS also hired local mechanical contractors to run the plumbing, which would later be connected to pump stations (also installed by IPS) scattered throughout the factory. From start to finish, the Whelen project took the IPS team approximately 18 months.
Speaking about taking on such a large project, Brask said, “From an engineering point of view, the challenge was thinking through all the process flows and automation details that needed to happen; Alex Stepinski had his flow charts and his logic worked out, but what does that tool have to look like? That’s where we came in. He did a very good job spec’ing the process, which made it a lot easier, but then configuring the tools to do each one of those functions—that took some time. Another big challenge for us was that normally, equipment manufacturers in the U.S. don’t get huge orders like this every day. We had to ramp up to keep up with the capacity we needed to build this along with our other projects and try to balance it all.”
The IPS equipment made up about one-third of Whelen’s equipment spend. Overall, IPS installed 52 machines at Whelen. One of the key technical challenges was working with other vendors to integrate their tools into the software management system. IPS had the responsibility of integrating these tools for the line to run as a turnkey solution. This involved writing software drivers to work with each supplier’s unique formats and languages that, in some cases, weren’t developed at the time the orders were placed with IPS. All systems needed to be programmed so the user could define the process flow of each job in a tray that could be independently routed and tracked. This soft-ware and hardware allowed the line to run as a continuous system.
All IPS equipment was manufactured in the U.S. in Cedar City, Utah, except for the handling equipment, which was made by IPS’ Taiwanese partner, WorldTech. It makes up an impressive automated conveyor system that tracks very smoothly and is filled with IPS loader/unloaders, buffer systems, etching and stripping systems, and so on. But perhaps the most impressive IPS system is the vertical electrolytic plating machine. Being fully automated, this machine has the biggest cycle time gain; in 30–40 minutes Whelen is able send a panel through the entire process. After all of the equipment was installed, IPS also worked with Proface, their touchscreen provider, to develop software that coordinates all the machines and allows the system to monitor each job in real-time.
Within the budget Whelen set, Alex dreamed up a remarkable factory, but it was IPS that played a central role in making it a reality.
“We’re in a redefining moment,” Brask said.” We had our initial business plan that we started the company with—to be multi-product, multi-industry. We’ve always stuck with that philosophy. That has gotten us through the down-turns and the recessions. We’ve been fortunate enough to always be stable. Now what we’re doing is we’re redefining the business plan to basically bring to the table integration and automation. It’s what the future market needs in the U.S. for circuit boards.”
Testimonial
"In a year when every marketing dollar mattered, I chose to keep I-Connect007 in our 2025 plan. Their commitment to high-quality, insightful content aligns with Koh Young’s values and helps readers navigate a changing industry. "
Brent Fischthal - Koh YoungSuggested Items
Southwest Antennas Secures First Major European Order for their Permanent Mounting Kits
07/24/2025 | Southwest AntennasSouthwest Antennas is proud to announce the receipt of its first major European order for the company’s Permanent Mounting Kits, marking a significant milestone in its international expansion efforts.
SCS Launches New G4 Spin Coater and Upgrades 6800 Series with Improved Design Features
07/23/2025 | SCSSpecialty Coating Systems (SCS) is pleased to announce the launch of its next-generation G4 Spin Coater, delivering enhanced control, connectivity and usability for research, development and small-scale production environments.
AI-driven MES Rewriting the Rules of Manufacturing Transformation
07/23/2025 | Francisco Almada Lobo, Critical ManufacturingThe Critical Manufacturing MES & Industry 4.0 International Summit, June 12–13, revealed a profound shift in how manufacturers approach digital transformation. AI-enabled execution systems are no longer a future ambition but are essential for navigating complexity and driving change.
Smart Automation: What Industry 4.0 Means for Mid-sized Electronics Manufacturing
07/24/2025 | Josh Casper -- Column: Smart AutomationIndustry 4.0 has become a go-to phrase in manufacturing circles, though it’s often used as a slogan rather than a clearly defined concept. At electronics manufacturing trade shows or conferences, marketing banners and vendor literature display the term prominently; many technical sessions also focus on it. Industry 4.0 is the push for smart factories, with a focus on autonomous machines, cloud-connected systems, and AI-powered decisions.
ESD Alliance Reports Electronic System Design Industry Posts $5.1 Billion in Revenue in Q1 2025
07/16/2025 | SEMIElectronic System Design (ESD) industry revenue increased 12.8% to $5,098.3 million in the first quarter of 2025 from the $4,521.6 million registered in the first quarter of 2024, the ESD Alliance, a SEMI Technology Community, announced in its latest Electronic Design Market Data (EDMD) report.