-
- News
- Books
Featured Books
- smt007 Magazine
Latest Issues
Current IssueSupply Chain Strategies
A successful brand is built on strong customer relationships—anchored by a well-orchestrated supply chain at its core. This month, we look at how managing your supply chain directly influences customer perception.
What's Your Sweet Spot?
Are you in a niche that’s growing or shrinking? Is it time to reassess and refocus? We spotlight companies thriving by redefining or reinforcing their niche. What are their insights?
Moving Forward With Confidence
In this issue, we focus on sales and quoting, workforce training, new IPC leadership in the U.S. and Canada, the effects of tariffs, CFX standards, and much more—all designed to provide perspective as you move through the cloud bank of today's shifting economic market.
- Articles
- Columns
- Links
- Media kit
||| MENU - smt007 Magazine
Overview Miniaturization on Large Form Factor PCBA
February 24, 2016 | D. Geiger, A. Mohammed, M. Kurwa, AEG, Flextronics International Inc.Estimated reading time: 10 minutes
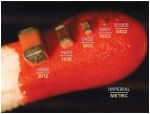
In today’s fast moving world of consumer electronics, miniaturization has been a key element to enable smarter phones, wearable devices, and other technology advances. The miniaturization technologies used on the board assembly level include tighter component to component spacing (down to 0.100mm in some cases), use of package on package technology, finer pitches (direct flip chip down to 160um and CSP packages down to 0.3mm pitch). The use of these technologies has enabled greater functional density in the applications.
When looking at the tear downs of many of the items, the PCBA is the smallest part of the overall system. Batteries and displays in smart phone take up most of the space within the mechanical assembly. Advances in the assembly area have also enabled these capabilities and a trend of these miniaturization techniques are migrating to other products that typically have longer or harsher reliability requirements. Products such as server, storage and telecom would like further increase functional density so would benefit from these technologies. However, there are some constraints to applying these technologies to these PCBA types.
Items like rework ability and the effects on the adjacent components need to be taken into account. This is a critical item as many of these products need to survive in the field upwards of 15-20 years. For the consumer level product 2-5 years is sufficient typically. For the various miniaturization technologies this paper will explore what is needed to use the technologies successfully and then explain some of the challenges that need to be addressed.
Miniaturization of passive components
As component packages continue to trend smaller, the office equipment boards, telecom, server, storage have usually have not gone beyond the 0402 package size. In consumer electronics the trend is going beyond 01005 and down into m03015 or even m0201. A migration of traditional 0201 passive components is being seen, especially on RF type of boards. The smaller components are desirable for the designers to help the signal integrity and also enable less amount of board real estate to be used.
On these larger form factor boards overall real estate is not a main concern; however localized high density around critical circuits is required. In some cases, localized design rules are used for the high density areas. The processes for printing solder paste, placing the components, reflow and rework have all been developed many years ago, so now the challenges would be what are the effects of implementing the smaller packages onto these high value boards.
One of the key challenges in the process for 0201 on large form factor assemblies is the ability to print solder paste successfully. In many cases these boards were using 0.150mm to 0.125mm stencils while 0201 process it is ideal to use 0.100mm thick stencils. Solder paste particle size can help and the more common particle size being used today is type 4 especially for the high volume products. Also advances in stencil technologies with nano-coatings or fine grain stencil have help create more consistent solder deposits and have helped reduce the area ratios that can be printed consistently.
A couple solutions for applying 0201 onto the large form factor PCBA is to use a step stencil if 0.125/0.150mm is required for other components, the 0201 area can be stepped down to 0.100mm. However if the components are too close together then a step stencil may not be feasible. Then the solution can be to overprint the 0201s using the 0.125mm stencil and open the stencil aperture to allow for an area ratio around 0.6 to ensure good printability.
In the picture (Picture 1), a land pattern was design to allow the use of a 0.150mm stencil to achieve a good print for the 0201 component. This pattern allowed high yields, however it did not take advantage of the actual 0201 space savings.
One other solution is to change the overall stencil to 0.100mm thick and only add more solder to the components that may need additional solder, such as connectors. A way to add more solder is to overprint the pad or pick and place preform of solder onto the solder deposit. These techniques have been used for various solutions today.
Component-to-component spacing
Another area that PCB designer would like to be able to do is to decrease the spacing between a BGA to the adjacent components. It is common to leave a spacing of up to 5mm between a BGA and the adjacent ICs. The main reason for this spacing is to allow for rework of the BGA without affecting the adjacent components which in turn could affect the overall reliability of the solder joints on the adjacent component. In the consumer products, this is not a concern as the long term reliability is shorter than the infrastructure or industrial type of products. The BGA rework process typically uses hot air through a nozzle that directs the heat to the targeted component however the heat spillover will affect the IC components next to it potentially causing partial reflow of the solder joint. (See Figure 1) The ideal condition is to prevent the adjacent component from reaching the reflow temperatures or ensuring that the full component solder joints see complete reflow temperatures.
Figure 1: Conventional Setup for BGA rework.
In order to allow closer component spacing between a BGA to another IC heat management needs to be resolved. Initial assembly of BGA to adjacent components is capable in the current manufacturing process. Spacing down 0.250mm spacing can be achieved. This is commonly used for consumer level product where impact on rework ability is less of a concern.
Figure 2: Peak Temperature vs Distance with various shielding.
Page 1 of 3
Testimonial
"In a year when every marketing dollar mattered, I chose to keep I-Connect007 in our 2025 plan. Their commitment to high-quality, insightful content aligns with Koh Young’s values and helps readers navigate a changing industry. "
Brent Fischthal - Koh YoungSuggested Items
Indium Corporation Promotes Two Leaders in EMEA (Europe, Middle East, and Africa) Markets
08/05/2025 | Indium CorporationWith its commitment to innovation and growth through employee development, Indium Corporation today announced the promotions of Andy Seager to Associate Director, Continental Sales (EMEA), and Karthik Vijay to Senior Technical Manager (EMEA). These advancements reflect their contributions to the company’s continued innovative efforts with customers across Europe, the Middle East, and Africa (EMEA).
MacDermid Alpha Electronics Solutions Unveils Unified Global Website to Deepen Customer, Talent, and Stakeholder Engagement
07/31/2025 | MacDermid Alpha Electronics SolutionsMacDermid Alpha Electronics Solutions, the electronics business of Elements Solutions Inc, today launched macdermidalpha.com - a unified global website built to deepen digital engagement. The launch marks a significant milestone in the business’ ongoing commitment to delivering more meaningful, interactive, and impactful experiences for its customers, talent, and stakeholders worldwide.
KOKI to Showcase Analytical Services and New HF1200 Solder Paste at SMTA Guadalajara 2025
07/31/2025 | KOKIKOKI, a global leader in advanced soldering materials and process optimization services, will exhibit at the SMTA Guadalajara Expo & Tech Forum, taking place September 17 & 18, 2025 at Expo Guadalajara, Salón Jalisco Halls D & E in Guadalajara, Mexico.
Weller Tools Supports Future Talent with Exclusive Donation to SMTA Michigan Student Soldering Competition
07/23/2025 | Weller ToolsWeller Tools, the industry leader in hand soldering solutions, is proud to announce its support of the upcoming SMTA Michigan Expo & Tech Forum by donating a limited-edition 80th Anniversary Black Soldering Set to the event’s student soldering competition.
Koh Young Appoints Tom Hattori as President of Koh Young Japan
07/21/2025 | Koh YoungKoh Young Technology, the global leader in True 3D measurement-based inspection solutions, announced the appointment of Tom Hattori as President of Koh Young Japan (JKY).