-
- News
- Books
Featured Books
- design007 Magazine
Latest Issues
Current IssueProper Floor Planning
Floor planning decisions can make or break performance, manufacturability, and timelines. This month’s contributors weigh in with their best practices for proper floor planning and specific strategies to get it right.
Showing Some Constraint
A strong design constraint strategy carefully balances a wide range of electrical and manufacturing trade-offs. This month, we explore the key requirements, common challenges, and best practices behind building an effective constraint strategy.
All About That Route
Most designers favor manual routing, but today's interactive autorouters may be changing designers' minds by allowing users more direct control. In this issue, our expert contributors discuss a variety of manual and autorouting strategies.
- Articles
- Columns
- Links
- Media kit
||| MENU - design007 Magazine
Ventec to Focus on ‘tec-speed’ Brand for High Speed/Low Loss Materials at IPC APEX 2016
March 8, 2016 | Ventec International GroupEstimated reading time: 2 minutes
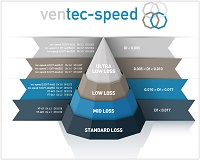
Ventec International Group, a world leader in the production of polyimide and high-reliability epoxy laminates and prepregs, unveiled their high-speed/low-loss product portfolio, tec-speed, in January 2016. Ventec will be showcasing the range globally at a number of shows this year. Starting with IPC APEX EXPO in Las Vegas (15-17 March 2016), tec-speed will be a highlight at Ventec’s booth number 827 with an emphasis on the mil/aero applications.
Tec-speed unites Ventec's high-speed/low-loss product portfolio and better positions the range under a single identity, connecting the products through a clear and cohesive visual presentation. The tec-speed laminates and prepregs range from mid-loss (Df 0.012) to ultra-low-loss (Df 0.003) specifications with Dk levels ranging between 3.9 and 3.2, offering the ultimate in laminate technology and quality assurance through Ventec's proprietary manufacturing and distribution network.
Jack Pattie, president of Ventec USA, said, “Thermal performance and signal integrity demands are increasing, particularly for mil/aero applications where miniaturization and density of components are pushing the boundaries of PCB design. Tec-speed materials and our strategic roadmap of new innovative additions to the range, provide the technological innovation, high performance and quality demanded by our customers.”
A selection of products will be highlighted at the show, including:
- tec-speed 6.1 (Dk 3.2, Df 0.004 RC 50%) - Ultra-Low Loss High-Tg material available with all copper styles, including HVLP. Uses low Dk spread glass to improve skew and jitter. Applications include telecom, router, servers, etc. Specifically developed for backplane and daughter card designs where good signal integrity is essential. This material has excellent thermal properties.
- tec-speed 4.0 (Dk 3.8, Df 0.007) - Low-loss high-Tg material available with all copper styles, including HVLP. Applications focus on high-frequency and high-speed designs, Automotive and satellite communication, Navigation and GPS are typical applications. This material has excellent thermal properties.
- tec-speed 1.0 (Dk 3.9, Df 0.012 @ 10GHz RC75%) - Mid-loss mid-Tg halogen-free material available with all copper styles. Applications include hand-held products, specifically those that require high-frequency high-speed materials. This material has excellent thermal properties.
About Ventec International
With volume manufacturing facilities and HQ in Suzhou China, Ventec International specializes in advanced copper clad glass reinforced and metal backed substrates for the PCB industry. With distribution locations and quick-turn CCL manufacturing sites in both the US and Europe, Ventec International is a premier supplier to the Global PCB industry. For more information about Ventec’s solutions and the company’s wide variety of products, please click here or download to the Ventec APP.
Testimonial
"Our marketing partnership with I-Connect007 is already delivering. Just a day after our press release went live, we received a direct inquiry about our updated products!"
Rachael Temple - AlltematedSuggested Items
50% Copper Tariffs, 100% Chip Uncertainty, and a Truce
08/19/2025 | Andy Shaughnessy, I-Connect007If you’re like me, tariffs were not on your radar screen until a few months ago, but now political rhetoric has turned to presidential action. Tariffs are front-page news with major developments coming directly from the Oval Office. These are not typical times. President Donald Trump campaigned on tariff reform, and he’s now busy revamping America’s tariff policy.
Global PCB Connections: Understanding the General Fabrication Process—A Designer’s Hidden Advantage
08/14/2025 | Markus Voeltz -- Column: Global PCB ConnectionsDesigners don’t need to become fabricators, but understanding the basics of PCB fabrication can save you time, money, and frustration. The more you understand what’s happening on the shop floor, the better you’ll be able to prevent downstream issues. As you move into more advanced designs like HDI, flex circuits, stacked vias, and embedded components, this foundational knowledge becomes even more critical. Remember: the fabricator is your partner.
MKS’ Atotech to Participate in IPCA Electronics Expo 2025
08/11/2025 | AtotechMKS Inc., a global provider of enabling technologies that transform our world, announced that its strategic brands ESI® (laser systems) and Atotech® (process chemicals, equipment, software, and services) will showcase their latest range of leading manufacturing solutions for printed circuit board (PCB) and package substrate manufacturing at the upcoming 17th IPCA Show to be held at Pragati Maidan, New Delhi from August 21-23, 2025.
MKS Showcases Next-generation PCB Manufacturing Solutions at the Thailand Electronics Circuit Asia 2025
08/06/2025 | MKS Instruments, Inc.MKS Inc, a global provider of enabling technologies that transform our world, today announced its participation in Thailand Electronics Circuit Asia 2025 (THECA 2025), taking place August 20–22 at BITEC in Bangkok.
Point2 Technology, Foxconn Interconnect Technology Partner to Revolutionize AI Cluster Scalability with Terabit-Speed Interconnect
08/06/2025 | BUSINESS WIREPoint2 Technology, a leading provider of ultra-low-power, low-latency mixed-signal SoC solutions for multi-terabit interconnect, and Foxconn Interconnect Technology (FIT), a global leader in precision interconnect solutions, have signed a Memorandum of Understanding (MOU) to accelerate the commercialization of next-generation Active RF Cable (ARC) and Near Pluggable e-Tube (NPE) solutions.