Manufacturing Micro Components with Laser Light
March 24, 2016 | RUBINEstimated reading time: 5 minutes
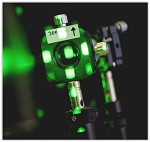
Non-contact mounting and manipulation of objects with the aid of light – it sounds like a vision from a science-fiction film. But it is daily routine at the Applied Laser Technologies lab.
Working with optical tweezers is daily routine for PhD student Jannis Köhler. He uses the tool for testing the manipulation of rotatable microstructures.
If the Enterprise cannot escape an enemy or the Millennium Falcon in Star Wars is pulled into the Death Star by an invisible force, so-called tractor beams are at work. A frequently used technical aid in science fiction movies; however, just like intergalactic spaceships, it is still waiting to be realised – at least on a large scale.
On the microscopic level, tractor beams have long been deployed. At the Chair of Applied Laser Technologies, they are in use more or less every day. The team headed by Prof Dr Cemal Esen (fig. 1) utilises laser light for mounting and manipulating miniscule objects. In this way, the diameter of the manipulated particles is in the range of 0.5 and 20 micrometres, and they are consequently even smaller than the diameter of a human hair.
This is the clou. That’s because technical components have become extremely sophisticated, and in future they might be made even smaller. So small that not even the finest pair of mechanical tweezers will be able to grip them. This is where optical tweezers are applied as a trapping tool made up of strongly focused laser light.
Light applies a force to the miniscule objects, which pulls them towards the spatial location of strongest intensity into the laser beam – at least if the objects are spherical. Applied forces are very small – approximately one billionth Newton. Thus, this technology is useless for moving spaceships. However, optical tweezers have become a standard tool for the manipulation of microscopic particles in research.
Cemal Esen’s group has developed matching modules which the tool can manipulate to assemble larger structures. Even though this is basic research, the engineers do not lack in ideas for potential applications in which the technology can be used one day in future.
“It is conceivable that such modules could be used to build micro-robots,” fantasises PhD student Sarah Ksouri. “Such systems could be used for minimal invasive surgery.” The micro machines could perform various repair procedures in the human body. “Currently, this is a crazy, but innovative idea,” she adds.
For the vision to become reality, extremely small machines must be built. Optical tweezers have been created precisely for processes carried out on such miniscule scale. Another advantage is: if small objects are trapped and moved with light, no damage will occur, such as the one that might be caused by the pressure of real tweezers.
However, manufacturing modules suitable for this procedure is not a trivial task. They must be fully compatible and form long-lasting structures. But at the same time it must be possible to disassemble them, if needed. Sarah Ksouri discloses where the ideas are coming from. “We essentially imagine large objects and consider methods of reproducing them as miniscule copies,” says the engineer. Examples include click-lock laminate flooring or the interlocking system of Lego bricks.
“However, the forces vary significantly from those in reality,” points out her PhD colleague Jannis Köhler. “If I want to move a cup, it’s mainly its weight that is relevant. Whereas our components are so small that weight is not an issue.” On this level, surface forces play a crucial role. Adhesion could be a problem, for example. If an object suddenly ends up stationary on a surface, the researchers can barely get it off again.
The first step of the process is a three-dimensional computer model of the object that is supposed to be manufactured, which is subsequently realised with a micro 3D-printer. To this end, the researchers apply a drop of photoresist to a slide. The fluid is exposed to the laser beam in the spots indicated by the computer model. In the places where the photoresist is exposed to the laser, a solid structure is formed. The remaining liquid is rinsed off with a solvent.
“But it’s not as if it’s so simple that this procedure works by creating one structure,” explains Ksouri. The engineers had done countless investigations until they succeeded in producing two matching jigsaw pieces. If the clearance fit is not precise or if the fluid cannot be rinsed off the generated structure, assembling the pieces might be impossible. In this case, it takes a lot of work to find the error.
Jannis Köhler uses the same method to create objects of a different kind. His rotatable structures (fig. 3) might one day become the movable elements in a micro-robot. Moreover, he is puzzling over components made from elastic polymers, which could be more easily assembled than rigid materials. In order to interlock two structures, a certain force must be applied – in the same way that two Lego bricks are clicked together. If one of the elements yielded a bit, it might be easier to push the other one in.
The team at the Chair of Applied Laser Technologies is thus researching a number of different principles for merging two-photon polymerisation and optical tweezer technologies in an appropriate way. At the moment, additional experiments with doped materials are carried out. Those materials are enriched with nanoparticles from certain elements which give polymer structures a specific function, for example by giving them magnetic or electrically conducting properties.
Such experiments are possible only because the Chair unites the expertise and technology of three different fields under one roof: two-photon polymerisation, optical tweezers and nano-doping. “Only a handful of labs worldwide are able to apply these three technologies at the same time,” states Cemal Esen. One of his group’s dreams is to combine all three processes in one device one day. In the first step, those devices would generate functionless structures from polymers. They would subsequently apply nanoparticles to these structures in order to give them a specific function; and, finally, they would assemble them to larger structures. Until then, the RUB group has still a lot of basic research ahead.
Suggested Items
Insulectro & Dupont Host Technology Symposium at Silicon Valley Technology Center June 25
06/22/2025 | InsulectroInsulectro, the largest distributor of materials for use in the manufacture of PCBs and printed electronics, and DuPont, a major manufacturer of flex laminates and chemistry, invite fabricators, OEMS, designers, and engineers to attend an Innovation Symposium – Unlock the Power - this Wednesday, June 25, at DuPont’s Silicon Valley Technology Center in Sunnyvale, CA.
Ventec Strengthens Commitment to Halogen-Free PCB Manufacturing in Europe
06/11/2025 | Ventec International GroupVentec International Group, the PCB materials innovator, manufacturer, supplier and one-stop shop for copper clad laminates, prepregs, as well as process consumables and PCB manufacturing equipment has established volume inventory of halogen-free FR4.1 and FR15.1 PCB materials at its European hub in Germany.
Ventec International Group Enters into a Fulfillment and Supply Agreement with Matrix and Launches Ventec Americas
06/09/2025 | Ventec International GroupVentec is excited to announce a new partnership with Matrix aimed at enhancing the fulfillment, value-added conversion, and distribution of PCB base materials across the North American market. This collaboration is set to significantly improve supply chain efficiency, and delivery performance for the company's North American customers.
Panasonic Appoints Matrix as its Authorized Distributor in Europe
06/03/2025 | Matrix ElectronicsEffective July 1st, 2025, Panasonic Industry Co., Ltd. has appointed Matrix Electronics Limited as its Authorized Distributor in the European region.
From DuPont to Qnity: A Bold Move in Electronics Materials
05/14/2025 | Marcy LaRont, I-Connect007DuPont has announced the intended spinoff of a public independent electronics company, Qnity, which will serve as a solutions provider to the semiconductor and electronics industries to enhance competitiveness and innovation in advanced computing, smart technologies, and connectivity. In this interview, Jon Kemp, Qnity CEO-elect and current president of DuPont’s Electronics business, shares his insights on the strategic separation from DuPont.