-
-
News
News Highlights
- Books
Featured Books
- pcb007 Magazine
Latest Issues
Current IssueSales: From Pitch to PO
From the first cold call to finally receiving that first purchase order, the July PCB007 Magazine breaks down some critical parts of the sales stack. To up your sales game, read on!
The Hole Truth: Via Integrity in an HDI World
From the drilled hole to registration across multiple sequential lamination cycles, to the quality of your copper plating, via reliability in an HDI world is becoming an ever-greater challenge. This month we look at “The Hole Truth,” from creating the “perfect” via to how you can assure via quality and reliability, the first time, every time.
In Pursuit of Perfection: Defect Reduction
For bare PCB board fabrication, defect reduction is a critical aspect of a company's bottom line profitability. In this issue, we examine how imaging, etching, and plating processes can provide information and insight into reducing defects and increasing yields.
- Articles
- Columns
- Links
- Media kit
||| MENU - pcb007 Magazine
Estimated reading time: 12 minutes
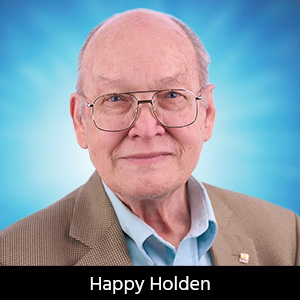
Contact Columnist Form
Failure Modes and Effects Analysis (FMEA)
Figure 2: FMEA flow chart.
Steps in Performing FMEA
- Discuss and define system functional requirements (scope), including all modes of operation (list in order of decreasing importance). Is it for concept, system, design, process, product or service and customer needs?
- Develop a functional block diagram and a reliability block diagram (Figure 2) for each subassembly being analyzed.
- Define parameters and functions of each functional block required for successful operation of the system.
- Using the FMEA forms to document the further steps, identify potential failure modes for each of the functional blocks.
- Analyze system or subassembly functions affected by factors such as those in the list of FMEA considerations.
- Identify all possible causes for each failure mode of the functional block being analyzed. The causes must be detailed to the component level wherever possible. These are potential failure modes. If necessary, go back and rewrite the function with more detail to be sure the failure modes show a loss of that function.
- Identify all possible ways the failure modes could affect the functions of the higher level assemblies.
- Assign the frequency, criticality, and detection values for each failure mode. (Tables 1– 3)
- Obtain the RPN by multiplying the three values assigned in step 8. This priority number will allow us to focus on the most important failure modes first.
- Determine all the possible root causes and corrective actions for each failure mode, and update the design status as it progresses.
- Summarize the failure modes and corrective actions in order of decreasing RPN.
- Focus on eliminating at least the 50% of the failure modes with the highest RPN.
An example of a FMEA analysis is shown in Figure 3.
Page 3 of 5
More Columns from Happy’s Tech Talk
Happy’s Tech Talk #40: Factors in PTH Reliability—Hole VoidsHappy’s Tech Talk #39: PCBs Replace Motor Windings
Happy’s Tech Talk #38: Novel Metallization for UHDI
Happy’s Tech Talk #37: New Ultra HDI Materials
Happy’s Tech Talk #36: The LEGO Principle of Optical Assembly
Happy’s Tech Talk #35: Yields March to Design Rules
Happy’s Tech Talk #34: Producibility and Other Pseudo-metrics
Happy’s Tech Talk #33: Wet Process Management and Control