-
- News
- Books
Featured Books
- pcb007 Magazine
Latest Issues
Current IssueThe Hole Truth: Via Integrity in an HDI World
From the drilled hole to registration across multiple sequential lamination cycles, to the quality of your copper plating, via reliability in an HDI world is becoming an ever-greater challenge. This month we look at “The Hole Truth,” from creating the “perfect” via to how you can assure via quality and reliability, the first time, every time.
In Pursuit of Perfection: Defect Reduction
For bare PCB board fabrication, defect reduction is a critical aspect of a company's bottom line profitability. In this issue, we examine how imaging, etching, and plating processes can provide information and insight into reducing defects and increasing yields.
Voices of the Industry
We take the pulse of the PCB industry by sharing insights from leading fabricators and suppliers in this month's issue. We've gathered their thoughts on the new U.S. administration, spending, the war in Ukraine, and their most pressing needs. It’s an eye-opening and enlightening look behind the curtain.
- Articles
- Columns
- Links
- Media kit
||| MENU - pcb007 Magazine
Estimated reading time: 12 minutes
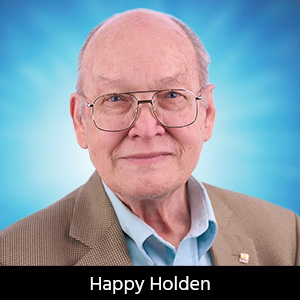
Contact Columnist Form
Failure Modes and Effects Analysis (FMEA)
FMEA ConsiderationsWhen analyzing system or subassembly functions affected by factors, consider this list:
Corrective Actions
When the failure modes have been rank ordered by RPN, corrective action should be first directed at the highest ranked concerns and critical items. If a recommended action might be a design of experiments (Plackett-Berman or Taguchi Method). The intent of any recommended action is to reduce the occurrence, severity and/or detection ranking.
What is Process FMEA (P-FMEA)?
Definition
A process potential FMEA (P-FMEA) is an analytical technique utilized by manufacturing/process engineers as a means to assure that, to the extent possible, potential concerns have been considered and addressed. In its most rigorous form, a P-FMEA is a summary of the engineer’s thoughts (including an analysis of items that could go wrong based on experience and past concerns) as a process is developed. This systematic approach parallels and formalizes the mental discipline that an engineer normally goes through in any manufacturing planning process.
The P-FMEA identifies potential product-related process failure modes, assesses the potential down-stream effects of the failures, identifies the potential manufacturing or assembly process causes, and identifies failure modes ranking according to their effect on the customer, thus establishing a priority system for corrective action considerations. The P-FMEA also documents the results of the manufacturing or assembly process.
Here is a list of activities for a P-FMEA:
1. Determine potential concerns that might cause failure modes for each process or subassembly and causes associated with the designing and manufacturing of a product
2. Identify actions which could eliminate or reduce the chance of a potential process failure occurring
3. Document the process and give each mode a numeric rating for frequency of occurrence, criticality, and probability of detection. Finally, multiply these three numbers together to obtain the RPN, which is used to guide the design effort to the most critical problems first.
Two aspects of P-FMEA are particularly important: a team approach, and timeliness. The team approach is vital because the broader the expertise that is brought to bear on making and assigning values to the failure mode list, the more effective the P-FMEA will be.
Timeliness is important because P-FMEA is primarily a preventive tool, which can help steer manufacturing development decisions between alternatives before failure modes are built-in, rather than reworking after the failure occurs. P-FMEA is equally applicable to hardware or software.
Steps in Performing P-FMEA
1. Discuss and define manufacturing and process functional requirements, including all modes of operation (list in order of decreasing importance).
2. Develop a functional block diagram and a reliability block diagram (Figure 2) for each manufacturing/process being analyzed.
3. Define parameters and functions of each functional block required for successful operation of the process.
4. Using the FMEA forms to document the further steps, identify potential failure modes for each of the functional blocks.
5. Analyze process or subassembly functions affected by factors such as those in the list of FMEA considerations.
6. Identify all possible causes for each failure mode of the functional block being analyzed. The causes must be detailed to the component level wherever possible.
7. Identify all possible ways the failure modes could affect the functions of the higher level manufacturing steps or processes or assemblies.
8. Assign the frequency, criticality, and detection values for each failure mode. (Tables 1–3).
9. Obtain the RPN by multiplying the three values assigned in step 8. This priority number will allow us to focus on the most important failure modes first.
10. Determine corrective actions for each failure mode, and update the manufacturing documentation as it progresses.
11. Summarize the failure modes and corrective actions in order of decreasing RPN.
12. Focus on eliminating at least the 50% of the failure modes with the highest RPN.
Summary
FMEA and P-FMEA are continuing processes that should be initiated at investigation/launch time of the design cycle and then be regularly updated as changes occur throughout the phases of product development. FMEA must be completed before the design is frozen, for its purpose is to affect the design and harden it against failures due to causes that can be anticipated. Potential manufacturing or assembly concerns known by the design engineer should be conveyed to the production engineers, using means such as the P-FMEA team meetings.
References
1. Procedures for Performing FM ECA, MIL-ST D-162, available from National Technical Information Service, Springfield VA 22161.
2. O'Connor, P.D.T., Practical Reliability Engineering, 2nd Edition, John Wiley & Sons, 1985. ISBN 0-471-90551-8.
3. Potential Failure Modes and Effects Analysis, Ford Motor Co., Sept. 1988. Available from FORD, Electronics Division, P.O. Box 6010, Dearborn, MI 48121-6010. Attn: Supplier Quality Manager.
4. Ireson & Coombs, Handbook of Reliability Engineering and Management, McGraw-Hill, 1988. ISBN 0-07-032039-X.
Seminars
- Reliability in Product Design and Testing, American Supplier Institute, 6 Parkland Blvd. Suite 411, Dearborn MI 48126. Contact: (313) 336-8877.
- Applied Reliability Engineering and Product Assurance for Engineers and Managers, Univ. of Maryland, Center for Professional Development, University Blvd. at Adelphi Rd., College Park MD 20742-1668. Contact: (301) 985-7157.
- Reliability Training Program (videotape seminar), Technicomp Inc., 1111 Chester Avenue, 300 Park Plaza, Cleveland OH 44114. Contact: (216) 687-1122.
Software Tools
- PC FMECA (IBM PC Program), Management Sciences Inc., 6022 Constitution Ave. NE, Albuquerque, NM 87110. Contact: (505) 255-8611.
- TreeMaster (IBM PC Program), Management Sciences Inc., 6022 Constitution Ave. NE, Albuquerque, NM 87110. Contact: (505) 255-8611.
- Results (FTA Program), Management Sciences Inc., 6022 Constitution Ave. NE, Albuquerque, NM 87110. Contact: (505) 255-861.
Happy Holden has worked in printed circuit technology since 1970, with Hewlett-Packard, NanYa/Westwood, Merix, Foxconn and Gentex. He is the co-editor, with Clyde Coombs, of the Printed Circuit Handbook, 7th Ed. To contact Holden, click here.
Page 5 of 5More Columns from Happy’s Tech Talk
Happy’s Tech Talk #40: Factors in PTH Reliability—Hole VoidsHappy’s Tech Talk #39: PCBs Replace Motor Windings
Happy’s Tech Talk #38: Novel Metallization for UHDI
Happy’s Tech Talk #37: New Ultra HDI Materials
Happy’s Tech Talk #36: The LEGO Principle of Optical Assembly
Happy’s Tech Talk #35: Yields March to Design Rules
Happy’s Tech Talk #34: Producibility and Other Pseudo-metrics
Happy’s Tech Talk #33: Wet Process Management and Control