-
- News
- Books
Featured Books
- pcb007 Magazine
Latest Issues
Current IssueSales: From Pitch to PO
From the first cold call to finally receiving that first purchase order, the July PCB007 Magazine breaks down some critical parts of the sales stack. To up your sales game, read on!
The Hole Truth: Via Integrity in an HDI World
From the drilled hole to registration across multiple sequential lamination cycles, to the quality of your copper plating, via reliability in an HDI world is becoming an ever-greater challenge. This month we look at “The Hole Truth,” from creating the “perfect” via to how you can assure via quality and reliability, the first time, every time.
In Pursuit of Perfection: Defect Reduction
For bare PCB board fabrication, defect reduction is a critical aspect of a company's bottom line profitability. In this issue, we examine how imaging, etching, and plating processes can provide information and insight into reducing defects and increasing yields.
- Articles
- Columns
- Links
- Media kit
||| MENU - pcb007 Magazine
Beyond FR-4: High Performance Materials for Advanced Designs, Part 2
May 19, 2016 | Advanced CircuitsEstimated reading time: 6 minutes
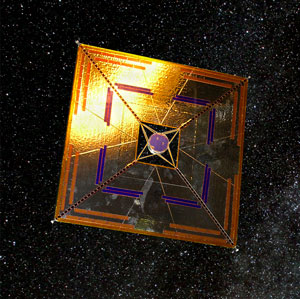
In Part One we covered basic FR-4 and variants that have been used in the commercial and military market for the past few decades, but in this column we will delve into the newer materials that target a specific application and/or market segment. As PCBs have become less a point-to-point wiring base and more an integral part of the signal path, so have the properties of the material become more important due to their effect on the signal.
In the quest to provide lower loss and dielectric constant there have been continual advancements in the resin formulation, such as high-Tg DICY-cured materials, high Tg un-filled phenolic-cured materials, high Tg filled phenolics, and modified epoxies. With advantages gained in signal integrity there have also been trade-offs in reliability, most commonly high temperature solderability and thermal decomposition. And other considerations such as stiffness, brittleness, moisture absorption, and outgassing, etc., need to be considered. So in short there is no perfect material that is best in all circumstances, but rather a list of characteristics that should be carefully scrutinized and chosen for the particular end-use of the product.
Questions to Ask Yourself
When considering a specific laminate material for the design there is a short list of characteristics that must meet the need before final selection:
- Do I need lead-free assembly compliance (RoHS)?
- Will I be limited by the manufacturer’s available core and prepreg thicknesses?
- What factor is most important—low (or high) dielectric constant or low loss tangent?
- What is the operating (frequency) range of the product (particularly in RF/microwave designs)?
- Are there published and verified outgassing specifications (typically aerospace and military apps)?
- Is hardness/brittleness a factor?
- What is the average (or maximum) intended operating temperature?
- Will I require offshore availability (for volume manufacturing)?
- What is the cost?
And there are many more considerations as well. Let’s take a closer look into some of the modern material selections that address specific needs. In the previous installment we reviewed polyimide, PPO (e.g., Getek) and high-frequency materials (e.g., Rogers & Taconic). Here are a few slightly more (specifically targeted) materials to add to the mix:
Thermal Laminates
As metal dissipates more thermal energy in the form of heat than thermoplastics, early PCB designs that had heat-generating components or were intended to dissipate heat relied on thicker metal layers or cores—heavy copper cores, brass and aluminum were also commonly used. But they came with manufacturing challenges as heavier metal required special fabrication processes which reduced the availability of qualified suppliers or raised the board price as a result. Today, specific formulations of laminates are engineered to work with a heavier metal layer to dissipate heat more effectively (if not more economically). Some of these materials are available from Bergquist Corporation, Laird Technologies, Stablcor and Arlon-Med. There are combinations of metal-backed laminates that are engineered for specific purposes (such as the booming LED industry). But they still come with their unique manufacturing requirements so selection should be considered by consulting your PCB fabricator’s engineering department.
Some of the newer formulations such as Arlon’s 91ML and 92ML offer great promise as the fabrication process is not radically different than building a typical FR-4 board. And the material properties are such that the benefit does not come at as high a premium as previous materials—such is the goal of modern material development.
HDI Thin-Laminates
When it comes to laser microvia processing, perhaps the most important characteristic of the material is that it can be laminated in a very thin layer—in order to keep the aspect ratio of the ablated hole manufacturable, and considering that the microvias are completely copper filled it must be thin enough to maintain a reasonable plating cycle time. Modern microvias are plated with copper from bottom to the top, and the technology must still allow a fairly thin surface thickness to facilitate fine lines and spaces—it would seem that one works against the other! So a fully copper plated/filled microvia must be completely filled, void-free, and post-planarized very flat to provide a planar surface for a robust solder joint. And here’s the rub—the smaller the microvia the thinner the associated dielectric thickness has to be.
Around fifteen or so years ago the cell-phone industry required a thin resin-coated foil (RCF)—often referred to as resin-coated copper (RCC) that would enable very small well-formed laser ablated microvias as there was the absence of e-glass support (as in standard PCB materials). But the trade-off for small diameter holes was a serious issue with X/Y dimensional stability (layer registration) due to the lack of reinforcement. If the features were as large as possible and the production panels as small as possible (to minimize registration errors), then it was workable, but as chip packages evolved ever smaller the registration issues increased. So RCF/RCC was gradually phased out, and for many years it was back to thin prepreg (e.g., 106) or flat-weave e-glass varieties of the same. Now there are improved materials available that address X/Y registration, small pad adhesion, and all of the other drawbacks while still maintaining the lack of supporting e-glass which is necessary for small diameter hole formation. Products such as ZetaLam introduced by Integral Technologies Corporation meet this current need.
Embedded Capacitance Materials
With the need to considerably reduce the overall form factor of modern PCB designs one of the methods is to eliminate passive surface components, and even though the overall size and pitch of such has been constantly shrinking, they can still take up a lot of space. Add to that the need to shorten signal lines and the popularity of capacitance layers has steadily been on the increase. The most commonly known version of capacitance layer pairs has been the product marketed as BC (e.g., buried capacitance—which began as “ZBC” when Zycon Corporation originally patented the concept—then bought by Hadco Corporation and finally Sanmina Corporation in its present day iteration). Basically, as opposing copper planes are placed closer to each other a natural capacitance can be achieved. It has been a technology that was licensed (both in the material manufacturing as well as PCB fabrication) but there are also alternative products that achieve similar results without a license (e.g., DuPont HK-4, 3M ECM, etc.). Basically, added to the board stackup as a thin plane/plane pair with the proper routing, the electrical benefit can be achieved and also reducing the number of assembled caps as a side benefit makes it attractive if a design warrants it.
Thin-Film Resistors
The same concept of eliminating surface components is the idea behind thin-film resistor layers. As a hybrid layer of Ni/Cr or Ni/P (depending upon the product—Ohmega or Ticer—two of the most commonly used technologies). The etched signal layer will include in-line resistors (the value being determined by surface area), which are then embedded within the board as laminated layers and thus eliminates surface components and possible trace length reduction. It is a mature process but does take additional processing and testing steps so there is a natural cost adder involved.
We have only scratched the surface of what is available in the advanced PCB world and there are new technologies being introduced every year, but you will want to thoroughly investigate each option and discuss the pros and cons with the PCB fabricator, as with any advanced technology. The PCB industry is rapidly approaching the limits of manufacturing using standard PCB technology, but as we borrow concepts and materials from the packaging industry we truly have a new paradigm in printed circuit design and manufacturing.
For more information about printed circuit board materials available for manufacturing advanced PCB designs, click here.
Testimonial
"The I-Connect007 team is outstanding—kind, responsive, and a true marketing partner. Their design team created fresh, eye-catching ads, and their editorial support polished our content to let our brand shine. Thank you all! "
Sweeney Ng - CEE PCBSuggested Items
Weller Tools Supports Future Talent with Exclusive Donation to SMTA Michigan Student Soldering Competition
07/23/2025 | Weller ToolsWeller Tools, the industry leader in hand soldering solutions, is proud to announce its support of the upcoming SMTA Michigan Expo & Tech Forum by donating a limited-edition 80th Anniversary Black Soldering Set to the event’s student soldering competition.
Koh Young Appoints Tom Hattori as President of Koh Young Japan
07/21/2025 | Koh YoungKoh Young Technology, the global leader in True 3D measurement-based inspection solutions, announced the appointment of Tom Hattori as President of Koh Young Japan (JKY).
Silicon Mountain Contract Services Enhances SMT Capabilities with New HELLER Reflow Oven
07/17/2025 | Silicon Mountain Contract ServicesSilicon Mountain Contract Services, a leading provider of custom electronics manufacturing solutions, is proud to announce a significant upgrade to its SMT production capability with the addition of a HELLER 2043 MK5 10‑zone reflow oven to its Nampa facility.
Knocking Down the Bone Pile: Addressing End-of-life Component Solderability Issues, Part 4
07/16/2025 | Nash Bell -- Column: Knocking Down the Bone PileIn 1983, the Department of Defense identified that over 40% of military electronic system failures in the field were electrical, with approximately 50% attributed to poor solder connections. Investigations revealed that plated finishes, typically nickel or tin, were porous and non-intermetallic.
SHENMAO Strengthens Semiconductor Capabilities with Acquisition of PMTC
07/10/2025 | SHENMAOSHENMAO America, Inc. has announced the acquisition of Profound Material Technology Co., Ltd. (PMTC), a premier Taiwan-based manufacturer of high-performance solder balls for semiconductor packaging.