-
- News
- Books
Featured Books
- smt007 Magazine
Latest Issues
Current IssueIntelligent Test and Inspection
Are you ready to explore the cutting-edge advancements shaping the electronics manufacturing industry? The May 2025 issue of SMT007 Magazine is packed with insights, innovations, and expert perspectives that you won’t want to miss.
Do You Have X-ray Vision?
Has X-ray’s time finally come in electronics manufacturing? Join us in this issue of SMT007 Magazine, where we answer this question and others to bring more efficiency to your bottom line.
IPC APEX EXPO 2025: A Preview
It’s that time again. If you’re going to Anaheim for IPC APEX EXPO 2025, we’ll see you there. In the meantime, consider this issue of SMT007 Magazine to be your golden ticket to planning the show.
- Articles
- Columns
Search Console
- Links
- Media kit
||| MENU - smt007 Magazine
Solder Paste Dispensing: Breaking the Limits of Printing
June 27, 2016 | Stephen Las Marias, I-Connect007Estimated reading time: 2 minutes
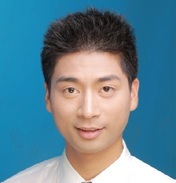
At the recent NEPCON China, I sat down with Eric Gu, application manager at Nordson Asymtek China, to talk about the challenges and innovations in solder paste dispensing, and factors to consider when using solder paste dispensers.
Stephen Las Marias: Eric, what are the greatest challenges that manufacturers have when it comes to soldering?
Eric Gu: Before, we were normally using screen printing for the solder paste process. But nowadays, products such as mobile phones, cameras or smart watches have become smaller and thinner. Therefore, the PCBs inside these products have become smaller and smaller, including the chips, the packages, and the components. So the current printing process would be limited by this trend. Also, printing will be limited by the gap. If the components are tall, we cannot do printing. So, it will require solder paste dispensing. That’s where we are. We have a needle valve for solder pasting. And also, when dispensing solder paste, you know, there are some alloys in solder paste that may cause needle clogging during dispensing. We have an extensive experience on solving these kinds of issue. We have very high level of success in solder paste dispensing.
Las Marias: Definitely the shrinking components are a big factor. But as we go smaller, the solder pastes being dispensed definitely are also becoming dot sized. What is the impact of the material in the solder on this trend?
Gu: Yes. The component is becoming smaller. It will only require to dispense a very small dot and hold a very narrow line, which is a key challenge. Another challenge is that material inside the solder paste can cause needle clogging.
Las Marias: So what innovations are happening to help customers address that issue?
Gu: Actually, we are using needle dispensing instead of jetting, but I know there are maybe one or two vendors here that are using solder jetting. Of course, solder jetting is much faster than solder-based needle dispensing. But you know, the key limitation of solder-based jetting is that we cannot use many types of solder pastes. Solder pastes have many types—type 1 through type 6. The smaller the solder particle, the more expensive the paste. For instance, a type 6 solder paste is maybe 10 or 15 times more expensive than type 5 solder paste. For solder paste jetting, maybe we can only use type 5 or type 6. But for our needle dispensing, we can use everything from type 1 to type 6—this is one advantage of needle dispensing.
Editor's Note: This article originally appeared in the June 2016 issue of SMT Magazine.
Suggested Items
Happy’s Tech Talk #38: Novel Metallization for UHDI
05/07/2025 | Happy Holden -- Column: Happy’s Tech TalkI have been involved in high-density electronics substrates since 1970 when I joined Hewlett-Packard’s RF semiconductor group after college. Figure 1 shows the difference between trace/space lithography for substrates and silicon starting in 1970. My projects involved sapphire circuits for RF devices, but the figure displays the state of PCBs and integrated CMOS circuits and their packaging, not discreet RF devices. Even then, semiconductors were 50X higher density.
Real Time with... IPC APEX EXPO 2025: Emerging Trends in Design and Technology
04/16/2025 | Real Time with...IPC APEX EXPOAndy Shaughnessy speaks with IPC design instructor Kris Moyer to discuss emerging design trends. They cover UHDI technology, 3D printing, and optical data transmission, emphasizing the importance of a skilled workforce. The role of AI in design is highlighted, along with the need for understanding physics and mechanics as designs become more complex. The conversation concludes with a focus on enhancing math skills for better signal integrity.
Real Time with... IPC APEX EXPO 2025: Transition Automation Focusing on Security Coatings and Squeegee Technology
04/16/2025 | Real Time with...IPC APEX EXPOMark Curtin, President of Transition Automation, gives an update on recent innovations at his company. He highlights a record sales month and their new focus on security coatings to fight counterfeiting. Mark explains the engineering behind their durable squeegees, the importance of maintenance, and the value of considering overall costs over just price.
Elephantech: For a Greener Tomorrow
04/16/2025 | Marcy LaRont, PCB007 MagazineNobuhiko Okamoto is the global sales and marketing manager for Elephantech Inc., a Japanese startup with a vision to make electronics more sustainable. The company is developing a metal inkjet technology that can print directly on the substrate and then give it a copper thickness by plating. In this interview, he discusses this novel technology's environmental advantages, as well as its potential benefits for the PCB manufacturing and semiconductor packaging segments.
Flexible Thinking: Flexible Circuit Technology—Looking Back and Forward
03/03/2025 | Joe Fjelstad -- Column: Flexible ThinkingFlexible circuit technology came on the scene as a solution largely for niche applications, however, the technology has emerged in recent years as a cornerstone of modern electronics. Today, the technology is enabling a broad range of new product designs across industries. From wearable devices and medical implants to foldable smartphones and numerous automotive applications, flexible circuits are arguably at the heart of much of the next generation of innovations.