-
- News
- Books
Featured Books
- smt007 Magazine
Latest Issues
Current IssueIntelligent Test and Inspection
Are you ready to explore the cutting-edge advancements shaping the electronics manufacturing industry? The May 2025 issue of SMT007 Magazine is packed with insights, innovations, and expert perspectives that you won’t want to miss.
Do You Have X-ray Vision?
Has X-ray’s time finally come in electronics manufacturing? Join us in this issue of SMT007 Magazine, where we answer this question and others to bring more efficiency to your bottom line.
IPC APEX EXPO 2025: A Preview
It’s that time again. If you’re going to Anaheim for IPC APEX EXPO 2025, we’ll see you there. In the meantime, consider this issue of SMT007 Magazine to be your golden ticket to planning the show.
- Articles
- Columns
Search Console
- Links
- Media kit
||| MENU - smt007 Magazine
Estimated reading time: 5 minutes
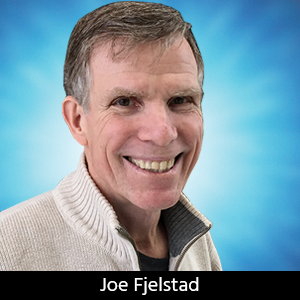
Flexible Thinking: Flexible Circuit Technology—Looking Back and Forward
Don’t worry. This is not a repeat of January’s Roman mythology history lesson about Janus, but it is another homage to the roots and branches of this increasingly important interconnection technology.
Flexible circuit technology came on the scene as a solution largely for niche applications, however, the technology has emerged in recent years as a cornerstone of modern electronics. Today, the technology is enabling a broad range of new product designs across industries. From wearable devices and medical implants to foldable smartphones and numerous automotive applications, flexible circuits are arguably at the heart of much of the next generation of innovations.
Over the past few years, the technology has undergone remarkable transformations, thanks to advancements in materials, manufacturing equipment, processes, and design techniques constantly popping up. These breakthroughs have served not only to improve the performance and functionality of electronic devices of every stripe but also opening new avenues for more sustainable and efficient product development.
Having written on the topic of flex circuits for many years, you will know that the concept of flexible circuits conflated with “flexible electronics” and “flex hybrid electronics” is not new. Early innovations related to flexible circuits (based on the technical literature searches of my dear friend Dr. Ken Gilleo) date back to the early 1900s but the technology did not find significant commercial use until the 1960s and 1970s, primarily in military and aerospace applications, but also notably in automotive dashboard instrument display cluster circuits. Typically, early flexible circuits were relatively simple, single-layer designs made from polyimide or polyester films, used in applications that required flexibility but not necessarily high-density interconnects or sophisticated features.
However, as demand for smaller, lighter, and more versatile electronics grew, so too did the potential for flexible circuit technology. Today, flexible circuits are often multilayer and ubiquitous in modern electronics, from consumer gadgets like smartphones and wearables to advanced medical devices, automotive sensors, and industrial control systems. The challenge over the past few decades has been to make flexible circuits more robust, capable, and cost-effective, while maintaining their inherent flexibility. The last few years have seen significant strides in achieving these goals.
The Role of Materials and Processes
One of the most significant recent advances in flexible circuit technology has been the development of new materials. Traditional flexible circuits were limited by the availability of suitable substrates and conductors. Polyimide and polyester films dominated as substrates, while copper was typically used for conductors. While suitable for many applications, these materials had limitations in terms of conductivity, durability, and manufacturing complexity.
In recent years, there has been a concerted effort to develop materials that overcome these challenges. Among the most exciting developments have been improvements in conductive inks and printing technologies. Researchers in both industry and academia have made substantial progress in developing highly conductive inks: not only silver, which has long been the go-to solution, but also improved copper and more recently, graphene. These improved inks, in combination with advances in printing technologies, allow for the creation of intricate circuit patterns with a lower cost and faster turnaround time compared to traditional methods. The concepts now being offered harken back in my memory to the ELF Technologies founded by Raychem scientists Dr. Leo Svendsen, Dr. Gary Geschwind, and Ray Noel, whom I helped as a consultant to launch the company in Redwood City in 1990.
At ELF (an acronym for Extend Length Flex), we were laser-printing catalytic toners onto moving rolls of polyimide film and then electrolessly and electrolytically plating them with copper in a roll-to-roll process. At the time, I envisioned an objective to create an “economic run unit of one,” a “holy grail” of manufacturing. I suggested that it might also be possible to have a factory (initially limited to single-sided flex) run virtually by the customer where they bid for position in a production cue. Current printing technologies not only shorten time to prototypes and market but also make flexible circuits more affordable. Moreover, they enable the design of circuits with complex geometries that would be difficult or impossible to achieve using more conventional manufacturing techniques.
That said, there is another potential companion method that might be used: laser direct structuring (LDS), which uses a laser to directly structure conductive patterns onto a substrate by ablating copper metal rather than imaging with a photopolymer and chemically etching. Where it can be used, it can potentially offer significant savings, certainly in terms of time.
Another area of advance has been in stretchable materials which have become a significant focus in the development of flexible interconnection solutions. For applications like wearable electronics or health-monitoring devices, flexibility alone is insufficient; stretchability is vital for such applications to conform to the human anatomy. While early stretchable designs needed to serpentine conductors to mitigate stress damage to conductors, stretchable conductive inks now are being developed to produce circuits that maintain their functionality even when stretched or deformed. Such material combinations are paving the way for innovations in robotics and smart wearable products such as health monitoring solutions.
Traditional methods for fabricating flexible circuits are unlikely to disappear anytime soon but they will be increasingly complemented by new techniques that increase precision, reduce costs, and allow for the integration of advanced features. One of the more promising is 3D printing. Because most flexible circuits are “flex-to-fit” applications, being able to print in 3D has some profound implications, allowing the printing of both the body and the conductor patterns in a single machine. It may not yet be as cost effective as one might hope.
What’s Next?
The future of flexible circuits appears incredibly bright. With continued advancements in materials, manufacturing techniques, and integration with emerging technologies, flexible circuits are poised to play an even more prominent role in shaping the future of electronics. From ultra-thin, stretchable wearables to smart packaging and beyond, the possibilities are quite literally endless, limited only by the designer’s imagination
Since their introduction, flexible circuits have represented not just a technological breakthrough but a fundamental shift in how engineers and product developers think about electronics. Their evolution is a testament to the power of the minds of the innovators, their collaboration, and the relentless pursuit of new possibilities. As this technology matures, we will undoubtedly see it transform the way we interact with the world around us, paving the way for smarter, more intuitive, and more sustainable electronic devices for years to come.
This column originally appeared in the February 2025 issue of Design007 Magazine.
More Columns from Flexible Thinking
Flexible Thinking: The Key to a Successful Flex Circuit Design TransferFlexible Thinking: Mind-tapping into January
Flexible Thinking: Another PCB Design Paradigm Shift in the Works
Flexible Thinking: Rules of Thumb—A Word to the Wise
Flexible Thinking: Musings on High Density Interconnections
Flexible Thinking: Integrated Passive Devices—Design Solutions With Many Benefits
Flexible Thinking: Mechatronics in a Flex World
Flexible Thinking: PCB Designers Still Wanted