-
- News
- Books
Featured Books
- design007 Magazine
Latest Issues
Current IssueCreating the Ideal Data Package
Why is it so difficult to create the ideal data package? Many of these simple errors can be alleviated by paying attention to detail—and knowing what issues to look out for. So, this month, our experts weigh in on the best practices for creating the ideal design data package for your design.
Designing Through the Noise
Our experts discuss the constantly evolving world of RF design, including the many tradeoffs, material considerations, and design tips and techniques that designers and design engineers need to know to succeed in this high-frequency realm.
Learning to Speak ‘Fab’
Our expert contributors clear up many of the miscommunication problems between PCB designers and their fab and assembly stakeholders. As you will see, a little extra planning early in the design cycle can go a long way toward maintaining open lines of communication with the fab and assembly folks.
- Articles
- Columns
Search Console
- Links
- Media kit
||| MENU - design007 Magazine
From the CAM Shop: Tight Tolerance Design Tips
July 8, 2016 | Mark Thompson, CID, Prototron CircuitsEstimated reading time: 2 minutes
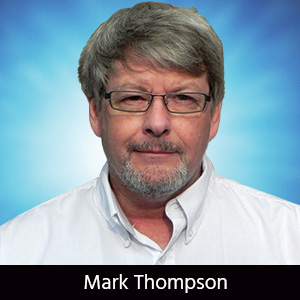
After you finish your design, it winds up in the hands of people like Mark Thompson, the man who runs the CAM department at Prototron Circuits in Redmond, Washington. He sees CAD data firsthand, and often has to address errors and inconsistencies in PCB designs. For this issue, we asked Mark to discuss the today’s tight tolerances, some of the problems they can cause PCB designers, and what designers can do when dealing with shrinking features.
Andy Shaughnessy: What are the tightest tolerances you are currently building?
Mark Thompson: First off, that is a great question. We have long said in fabrication if you added up all the accumulative tolerances a fab shop has to deal with the part would be physically impossible to build. Having said that, unusual process tolerances CAN be achieved, such as plated holes with a +/-.002” tolerance for press-fit devices. One fab shop may say that the best they can do for plated holes and slots/cutouts would be +/-.003” but often we can do +/-.002”. How is that possible, you ask? For one thing, we can tell the CAM system to select a tool that is +.004-.000”. This selects a tool that works best for a +/-.002” final tolerance.
Another typical tolerance issue is with controlled impedance. Many fabricators ask for +/-15% tolerance for traces thinner than .0035”. This is not uncommon considering that just 10% = less than half a mil of total accumulated deviation throughout the fabrication process. The good news is that most fabricators use a field solver for the impedances, which means they can adjust for process variables like plate, etch, mask thickness, etc. And ultimately this means that even in situations where a fabricator may ask for +/-15%, they may incur as little as 5% deviation if they have good process control. I guess I would end by saying if the customer has some unusual tolerances they need to achieve. I recommend speak with your chosen fabricator to make sure they can be met.
Shaughnessy: What are the most challenging issues fabricators face regarding fine spaces, traces, and pitch?
Thompson: Another great question. There are many. First and foremost is the chosen copper weight vs. trace and space. Many times this comes down to what a fabricator has to do for compensations for the process. In this case, we are talking about etch compensations.
Let’s say you have a .1 mm trace and space design and you desire 3 oz. finish. The general rule of thumb is that for every half ounce of starting copper, we do a half-mil etch compensation. For three ounces we would need a .003” etch comp, and if the space is .00393” (.1 mm) we would be left with a .00093”, space which is way outside of most folks’ capabilities.
To read this entire article, which appeared in the June 2016 issue of The PCB Design Magazine, click here.
Suggested Items
RF PCB Design Tips and Tricks
05/08/2025 | Cherie Litson, EPTAC MIT CID/CID+There are many great books, videos, and information online about designing PCBs for RF circuits. A few of my favorite RF sources are Hans Rosenberg, Stephen Chavez, and Rick Hartley, but there are many more. These PCB design engineers have a very good perspective on what it takes to take an RF design from schematic concept to PCB layout.
Elephantech: For a Greener Tomorrow
04/16/2025 | Marcy LaRont, PCB007 MagazineNobuhiko Okamoto is the global sales and marketing manager for Elephantech Inc., a Japanese startup with a vision to make electronics more sustainable. The company is developing a metal inkjet technology that can print directly on the substrate and then give it a copper thickness by plating. In this interview, he discusses this novel technology's environmental advantages, as well as its potential benefits for the PCB manufacturing and semiconductor packaging segments.
Trouble in Your Tank: Organic Addition Agents in Electrolytic Copper Plating
04/15/2025 | Michael Carano -- Column: Trouble in Your TankThere are numerous factors at play in the science of electroplating or, as most often called, electrolytic plating. One critical element is the use of organic addition agents and their role in copper plating. The function and use of these chemical compounds will be explored in more detail.
IDTechEx Highlights Recyclable Materials for PCBs
04/10/2025 | IDTechExConventional printed circuit board (PCB) manufacturing is wasteful, harmful to the environment and energy intensive. This can be mitigated by the implementation of new recyclable materials and technologies, which have the potential to revolutionize electronics manufacturing.
Connect the Dots: Stop Killing Your Yield—The Hidden Cost of Design Oversights
04/03/2025 | Matt Stevenson -- Column: Connect the DotsI’ve been in this industry long enough to recognize red flags in PCB designs. When designers send over PCBs that look great on the computer screen but have hidden flaws, it can lead to manufacturing problems. I have seen this happen too often: manufacturing delays, yield losses, and designers asking, “Why didn’t anyone tell me sooner?” Here’s the thing: Minor design improvements can greatly impact manufacturing yield, and design oversights can lead to expensive bottlenecks. Here’s how to find the hidden flaws in a design and avoid disaster.