-
- News
- Books
Featured Books
- pcb007 Magazine
Latest Issues
Current IssueInventing the Future with SEL
Two years after launching its state-of-the-art PCB facility, SEL shares lessons in vision, execution, and innovation, plus insights from industry icons and technology leaders shaping the future of PCB fabrication.
Sales: From Pitch to PO
From the first cold call to finally receiving that first purchase order, the July PCB007 Magazine breaks down some critical parts of the sales stack. To up your sales game, read on!
The Hole Truth: Via Integrity in an HDI World
From the drilled hole to registration across multiple sequential lamination cycles, to the quality of your copper plating, via reliability in an HDI world is becoming an ever-greater challenge. This month we look at “The Hole Truth,” from creating the “perfect” via to how you can assure via quality and reliability, the first time, every time.
- Articles
- Columns
- Links
- Media kit
||| MENU - pcb007 Magazine
Estimated reading time: 5 minutes
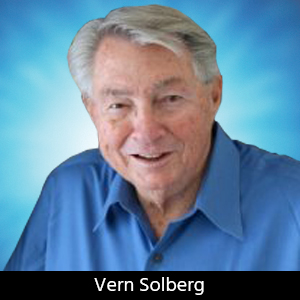
Flexible and Rigid-Flex Circuit Design Principles, Part 3
Specifying Base Materials
In collaboration with the supplier, define the materials that will meet the intended operating environment. Establish dielectric film thickness, finished copper foil thickness requirement, and determine whether the design requires an adhesive layer for bonding copper foil to the flex material or specify an adhesiveless copper clad dielectric. In regard to the base material, copper bonded to the dielectric using adhesive film is the most economical choice; however, when the product requires long-term dynamic flex operation, the adhesiveless copper-clad dielectric may be warranted. Additionally, adhesiveless copper flex can be supplied much thinner than the copper foils bonded onto flex with adhesive. The thin copper enables very fine-line circuit pattern capability.
It is important to research the various products in order to choose the one that best meets the design requirements. The key physical attributes that should be considered when selecting base materials for flexible circuits are:
- Moisture absorption
- Fire-retarding properties
- Electrical properties
- Mechanical properties
- Thermal properties
Both adhesiveless copper-clad films and materials relying on lamination with high-temperature adhesives will continue evolve. For example, DuPont, a major supplier of polyimide base materials, is said to have developed high-temperature adhesive technology that combines new polymer systems that significantly improves moisture and chemical resistance. The new material is tougher, exhibits better thermal conductivity and furnishes higher tensile strength with less dimensional distortion.
Semi-Additive Circuit Plating Process
Although applying copper foil to both sides of the polyimide film with adhesives is common, the copper can also be furnished on both surfaces without adhesive. The vapor deposition process, for example, furnishes a copper base metalization as thick as 200 microns. The sputter deposition process provides a thin seed layer of copper onto the polyimide film while in a vacuum chamber. A cathode element is charged with positive ions that form small particles of the copper that adhere to the dielectric films surface. In both variations, additional copper thickness is built-up onto the copper seed layer by electrolytic pattern plating.
Cover-Layer and Cover-Coat Materials
The cover-layer (commonly referred to as “coverlay”) is a thin dielectric film that is laminated over the copper surfaces following the chemical etching process. The purpose of the cover-layer film is to insulate and protect the copper circuit during operation as well as conforming to the same flex and form requirements of the base material. The cover-layer film material will normally be a thinner version of the base dielectric. For example, while the copper-clad base dielectric may be 25 microns (0.001“) or 50 microns (0.002“) thick, the coverlay material thickness will be only 12 microns (0.0005“).
Cover-coat is a more economical photoimageable dry (semi-liquid) film applied onto the copper-clad surface by lamination or as a liquid photoimageable material deposited onto the circuit surface using a screen or spray-coating process. As far as mechanical integrity, the laminated cover-layer film materials are physically the most durable while the thin cover-coat materials may exhibit pinhole voids and it may become brittle, commonly forming micro-cracks in the bend area.
Fabrication Documentation
Flexible circuit and rigid-flex fabrication drawings often have common issues with dimensioning. Too often the fabricator receives flex circuit documentation that is dimensioned as if they were sheet metal or machined parts with tolerances that are often made too tight for standard flex manufacturing processes or material properties. Over-dimensioning and tolerance issues commonly cause delays in getting drawings checked and approved or delays in getting on-time delivery from suppliers. Too often QA will reject parts that would work just fine because they just don’t meet tolerances specified on drawings and source inspectors cannot buy these parts without some higher-level approval. Unnecessary part rejection ties up supply chain, quality control, engineering, and manufacturing resources. Although the mechanical data within the computer-generated design file will be very detailed and include all dimensional attributes of everything needed to manufacture the circuit, the documentation developed for user acceptance can be simplified.
On the other hand, key information must be furnished. The intent is to provide the fabricator with the locations of the critical areas that are to be folded or flexed. Separate views showing an installed flex configuration should be added to the fabrication drawing as well. Drawings should contain a detailed list and description of the materials contained in the flex-circuits construction:
- Material stack-up
- Reinforced/stiffened areas
- Critical thickness areas
Include cross-section details for the more complex multilayer and rigid-flex applications and point out critical thickness areas. Define both upper and lower ends of the thickness requirement. When multiple conductors are routed in the same direction on both surfaces of the flexible base material, the circuit path on each side in the bend or fold area must be offset from one another to prevent stress cracking in the copper foil.
In regard to specifying fold and bend areas on the flexible circuit fabrication and assembly documentation, IPC-2223 recommends the following:
- Bend/fold line location dimensions on the fabrication document shall be depicted as a reference.
- The assembly document should show the dimensions of the finished folded configuration as a reference only.
- Bend/fold lines should be depicted as centerlines and noted as “bend line corresponds to center of the arc formed when folded.”
For maximum dynamic flex life and reliability, conductors in the bend area should always be routed perpendicular to the bend area. Furthermore, all conductors in the flex or bend zones (with the exception of those carrying current), should be uniform in width and evenly spaced. The neutral bend axis, where possible, should be located at the center of the conductor pattern. Although the design may require copper build-up during the via-hole plating process, avoid specifying additional build-up plating in areas requiring bending or maximizing flexibility.
There are bound to be a number of material-related questions that will arise during the planning and design phase of the flexible and rigid-flex substrate. As a general rule, the fabricator will be able to address most material issues. Other resources to consult when researching materials for the more unique flexible and rigid-flex applications are material suppliers. Both material specifications and application notes will often be available for the asking.
More Columns from Designer's Notebook
Designers Notebook: Basic PCB Planning Criteria—Establishing Design ConstraintsDesigners Notebook: Layer Stackup Planning for RF Circuit Boards
Designers Notebook: Addressing Future Challenges for Designers
Designers Notebook: Impact of Advanced Semiconductor Packaging on PCB Stackup
Designers Notebook: Implementing HDI and UHDI Circuit Board Technology
Designer's Notebook: Heterogeneous Integration and High-density SiP Technologies
Designers Notebook: PCB Design and IPC-CFX for Assembly Automation
Designer’s Notebook: What Designers Need to Know About Manufacturing, Part 2