-
- News
- Books
Featured Books
- smt007 Magazine
Latest Issues
Current IssueIntelligent Test and Inspection
Are you ready to explore the cutting-edge advancements shaping the electronics manufacturing industry? The May 2025 issue of SMT007 Magazine is packed with insights, innovations, and expert perspectives that you won’t want to miss.
Do You Have X-ray Vision?
Has X-ray’s time finally come in electronics manufacturing? Join us in this issue of SMT007 Magazine, where we answer this question and others to bring more efficiency to your bottom line.
IPC APEX EXPO 2025: A Preview
It’s that time again. If you’re going to Anaheim for IPC APEX EXPO 2025, we’ll see you there. In the meantime, consider this issue of SMT007 Magazine to be your golden ticket to planning the show.
- Articles
- Columns
Search Console
- Links
- Media kit
||| MENU - smt007 Magazine
Material Effects of Laser Energy When Processing Circuit Board Substrates During Depaneling
July 27, 2016 | Ahne Oosterhof, LPKF Laser & Electronics North AmericaEstimated reading time: 13 minutes
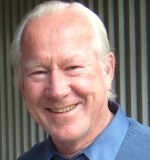
Using modern laser systems for the depanelization of circuit boards can create some challenges for the production engineer when it is compared to traditional mechanical singulation methods. Understanding the effects of the laser energy to the substrate material properly is essential in order to take advantage of the technology without creating unintended side effects. This paper presents an in-depth analysis of the various laser system operating parameters that were performed to determine the resulting substrate material temperature changes. A theoretical model was developed and compared to actual measurements. The investigation includes how the temperature increase resulting from laser energy during depaneling affects the properties of the PCB substrate, which varies from no measurable change to a lowering of the surface resistance of the cut wall depending on the cutting parameters.
In addition, the amount and properties of the ejecta that are potentially resulting from the laser processing is investigated. Understanding the composition and quantity of any resulting residue may have a great impact to both the board design and the selection of the appropriate circuit board singulation method that will achieve the best possible results. An energy dispersive X-ray analysis method (EDX) was performed to investigate if any unwanted material compounds are present on the cutting sidewalls of an FR4 circuit board substrate as a result of laser energy induced during the depaneling process.
Depaneling Methods
Many depaneling methods are being used in the industry, such as:
- punching/die cutting
- v-scoring
- wheel cutting/pizza cutter
- sawing
- water jet
- routing (+nibbling)
Some of these are useful only in very low cost, minimal quality applications; others can only be used for rectangular boards. Several can do damage to the board edges because of significant pressure and/or bending forces potentially causing some delamination which may impact long-term reliability. All this means that during the board layout care must be exercised to keep fragile components and sometimes circuit traces away from board edges. And the waterjet method has hardly been explored.
The most commonly used method is the routing where a kerf is cut around each board, regardless of board shape, by the panel manufacturer. To keep the board in the panel during the assembly process in a few locations the kerf is interrupted. The routed kerf in the panel typically is about 3 mm wide, which means that in a case with many small boards a significant amount of panel space is used for cutting slots. Sometimes, with many slots in the panel, the panel becomes less rigid and panel supports or a pallet is required during the assembly process. Typically, holes are being drilled in the connected areas to make it easier to break the boards from the panel which means that during board layout these locations must be decided and fragile components must be kept away from them.
Figure 1: Combining various singulation methods in the one panel.
Laser Cutting
The latest method added is laser routing, which can be done after the last step in the board assembly process. This means the panel retains its rigidity throughout the previous assembly steps. Like a router, the laser cuts completely through the board, so no bending or pressing on the edges of the board occurs, which means no stresses are exerted on the board material. With the use of a laser, cutting any board shape can be accommodated, and the changeover to different boards is very quick as the process is completely computer controlled.
Laser System
The three main parts of a laser cutting system are the laser, the X-Y table for panel movement and the scanner to move and locate the beam.
Figure 2: Example of a laser depaneling system in an in-line setting for automatic loading and unloading.
To cut various materials, several types of lasers are available. These have varied from CO2 at about 10 um wavelength available for well more than 20 years to UV lasers at about 350 nm wavelength showing up around 10 years ago. About 20 years ago the Nd:YAG lasers at 1054 nm wavelength were introduced to be used in stainless steel stencil cutting systems.
As the wavelength gets shorter the lasers have been more difficult to be produced economically, which has led to the gradual timewise availability of the different systems. Shorter wavelength lasers and those with very short pulse widths have typically been much more expensive, which is why it has taken time to get them deployed in the industry.
Infrared lasers can be called “hot” lasers as they heat and burn a path in the material to be cut. With UV lasers it is possible to ablate the material. A short high-energy pulse enters the top layer of the material and evaporates and explosively removes a layer of the material. By going over the same path several times, ultimately a cut is obtained through the material. As very little heat is produced by the UV beam, there is very little or no burned material on the edges of the cut depending on how the laser is being used (Figure 3).
Figure 3: Infrared cut versus ultra violet cut.
Depending on the wavelength of the light, some materials reflect it and some are completely transparent. For the ablation method to work, the laser beam has to penetrate into the material to be cut. Figure 4 shows how various circuit board constituents react with different wavelengths. To be able to ablate all of them the UV laser is a good choice. UV lasers (wavelength ~350 nm) have become economically attractive only for the past 10 years.
Page 1 of 6
Suggested Items
LPKF Reports Results for Full Year 2024
03/27/2025 | LPKFThe technology company LPKF Laser & Electronics SE published today its annual report for 2024. Despite the challenging economic conditions for the German mechanical engineering industry, LPKF was able to maintain its revenue slightly below the previous year's level at EUR 122.9 million.
Queen's University Belfast Enhances RF Research with LPKF ProtoLaser R4
03/26/2025 | LPKFThe Centre for Wireless Innovation (CWI) at Queen's University Belfast relies on the state-of-the-art LPKF ProtoLaser R4 to conduct RF research with high-precision structuring of sensitive materials.
Real Time with... IPC APEX EXPO 2025: LPKF's Advancements in Laser Depaneling Technology
03/25/2025 | Real Time with...IPC APEX EXPOIn this recent interview, Jake Benz from LPKF Laser and Electronics discusses advancements in laser depaneling technology, focusing on speed and quality. He highlights the previous negative reputation of laser depaneling and shares insights from nearly two decades of experience. As customer needs evolve, traditional companies are exploring laser technology.
Peter Mümmler to Become New CFO at LPKF
01/20/2025 | LPKF Laser & ElectronicsLPKF Laser & Electronics SE is pleased to announce that Peter Mümmler will be joining the Management Board as Chief Financial Officer with effect from 1 April 2025, with an initial contract term of 3 years.
Altus Sees Growing Interest for Laser Depanelling Solutions
11/04/2024 | Altus GroupAltus Group, a leading distributor of capital equipment in the UK and Ireland, has seen an increasing interest in laser depaneling systems from LPKF in 2024.