-
- News
- Books
Featured Books
- smt007 Magazine
Latest Issues
Current IssueIntelligent Test and Inspection
Are you ready to explore the cutting-edge advancements shaping the electronics manufacturing industry? The May 2025 issue of SMT007 Magazine is packed with insights, innovations, and expert perspectives that you won’t want to miss.
Do You Have X-ray Vision?
Has X-ray’s time finally come in electronics manufacturing? Join us in this issue of SMT007 Magazine, where we answer this question and others to bring more efficiency to your bottom line.
IPC APEX EXPO 2025: A Preview
It’s that time again. If you’re going to Anaheim for IPC APEX EXPO 2025, we’ll see you there. In the meantime, consider this issue of SMT007 Magazine to be your golden ticket to planning the show.
- Articles
- Columns
Search Console
- Links
- Media kit
||| MENU - smt007 Magazine
Perfect Placement of Connectors and Pins: 3D Measurement of Swash Circumference and Embedment Depth
July 29, 2016 | Jens Mille and Jens Kokott, Goepel Electronic GmbHEstimated reading time: 5 minutes
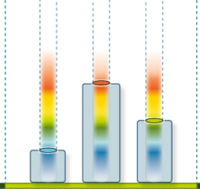
Where the production of electrical PCBs is concerned, manufacturers are faced with steadily increasing miniaturization and higher packing density. Coupled with this, increased requirements are placed on production and testing technologies. The same applies to the manufacturers of connection technology such as connectors and individual pins. Here, too, an increasing number of contacts have to be accommodated in ever smaller areas.
Packing densities in particular repeatedly create challenges in terms of testability, especially when high components such as connectors are fitted in close proximity to other components.
Connectors are also included in the scope of testing, and their design means that they have completely different handling and testing requirements. In addition to the traditional solder joint inspection, the mechanical integrity of the pins must also be checked. Two parameters are of interest in this context: On the one hand, the lateral location of the pin tip, and on the other hand, its height.
The horizontal as well as the vertical position of each individual pin must be tested if these connectors are to be used to establish an electrical connection to other assemblies in a subsequent automated process, or they are precisely fitted into a housing. Automated installation is no longer possible if the pins were deformed through mechanical influences during the preliminary stages.
The examination of the pin displacement on a lateral plane is called swash circumference testing. Swash circumference testing can be carried out using orthogonal inspection. This can generally already be ensured through standard 2D AOI systems. However, it must be considered that the pins, whose diameter is often smaller than one millimetre, have a tip that is only a few tenths of a millimetre in size. The illumination of the test object is therefore of key importance for the reliable detection of the characteristic. The AOI systems of GÖPEL of electronic GmbH have been successfully used for this testing task for many years, due to their multi-spectral and multidirectional lighting.
Measurement of Embedment Depth: a Particular Challenge
There is, however, a sharp increase in requirements when the height of the pin tip has to be determined. This test task is known as embedment depth or press-in depth. As the name of the test task indicates, it is not possible to meet these requirements using the usual two-dimensional measurement and testing technology, as orthogonal inspection cannot provide information on height. This problem cannot even be resolved by using suitable cameras for testing, because the deformation of the pins and PCB is unknown prior to the test, and it is often difficult to detect the pin tip. The reverse conclusion is: An additional testing dimension is required!
Figure 1: Possible errors on a connector pin.
Attempts to solve this problem using fringe projection often failed because of uncooperative surfaces, which do not provide reliable measuring signals as they are strongly reflective. Neither is it possible to use a triangulation process to carry out measurements into connector housings, as the walls of the housing literally put the interior parts into the shade. This can be partly compensated for through the use of several projectors or cameras, but, if not before, it becomes apparent that it cannot be used for measurements into holes when determining the press-in depth of a pin into a PCB (e.g., pressfit technology) or into other objects (e.g., connector housings).
3D Measurements Based on TMSA technology
One such technology that makes it possible to carry out 3D measurements even into deep holes with very small diameters (
TMSA features a white light source coupled into a telecentric measuring lens developed specially for this purpose. As a result, there is no angle between the light source and the sensors (in contrast to the triangulation process), which means that the lighting and signal beam path are identical. This configuration has the advantage that no shadows are created on high components, making it possible to carry out reliable measurements into deep gaps between components or into holes.
With this arrangement, the lens now differentiates the individual light wavelengths, so that only a small wavelength range is focused and reflected back, depending on the distance between the measuring lens and the surface to be measured. The reflected light or measuring signal is associated with a height value based on the evaluation of the respective intensity. Since this lens projects individual measurement points onto the PCB, the spot array must be moved for a wide-area recording of measurement values. Depending on the increment, this makes it possible to implement different lateral resolutions during scanning, so that they are freely configurable based on the requirements of the measuring task.
Figure 2: TMSA technology.
The technology also enables measurement values to be generated regardless of the reflection characteristics of the respective surfaces, making it possible to check features independently of the layout.
Where connectors or individual pins are concerned, errors such as bent connection contacts, too deep pin insertion into the housing, or portruding pins can occur. These may cause missed insertion of counterparts in subsequent processes. In a worst-case scenario, the assembly is unusable as a result.
Page 1 of 2
Suggested Items
Hunting for Clues: Feng Xue Solving Circuit Board 'Crimes' With AOI Standard
05/08/2025 | Linda Stepanich, IPCWhen residents in sleepy English villages needed a top-tier detective to solve a murder, they called on Belgian super-sleuth Hercule Poirot, author Agatha Christie’s fictional detective famous for using his “little grey cells” to solve crimes. In the same way, IPC standards development committees, when creating a standard to detect defects in circuit boards using Automated Optical Inspection (AOI), call on IPC A-Team, Hercule.
Real Time with... IPC APEX EXPO 2025: TRI Innovation—Transforming Semiconductor Inspection with AI Technology
04/25/2025 | Real Time with...IPC APEX EXPONolan Johnson talks with David Chiu, USA Sales Manager for TRI Innovation. TRI uses advanced technology to tackle challenges in inspecting tiny components. Their AI programming reduces coding time by 75%, enhancing efficiency in inspections. Collaborating with Nvidia, TRI integrates GPU technology to improve product development and encourages customers to share data for better AI performance.
Koh Young Installs 24,000th Inspection System at Fabrinet Chonburi
04/23/2025 | Koh YoungKoh Young, the global leader in True 3D measurement-based inspection and metrology solutions, proudly announces the installation of its 24,000th inspection system at Fabrinet Chonburi in Thailand. This advanced facility is operated by Fabrinet Co., Ltd., a global provider of advanced manufacturing services, specializing in complex optical, electro-optical, and electronic products
Real Time with... IPC APEX EXPO 2025: A Close Look at Inspection Technologies in the EMS Industry with Viscom
04/16/2025 | Real Time with...IPC APEX EXPOJuan Briceno, VP Viscom Americas, sits down with Kelly Dack for this interview. Viscom is a leader in inspection technologies for the EMS industry covering various inspection equipment like AOI and X-ray systems. Juan highlights Viscom's role in quality assurance. The discussion includes the impact of artificial intelligence on manufacturing processes and the benefits of 3D inspection techniques for defect detection. The importance of quality control and problem identification through AI is also emphasized.
Upgrade and Set Sail: The New ViTrox Exhibition Center Opens Up New Innovative Experiences
04/02/2025 | ViTroxViTrox, committed to becoming the world's most trusted technology company, is pleased to announce that its showroom in Shenzhen, China has been completely upgraded and reopened.