-
- News
- Books
Featured Books
- smt007 Magazine
Latest Issues
Current IssueIntelligent Test and Inspection
Are you ready to explore the cutting-edge advancements shaping the electronics manufacturing industry? The May 2025 issue of SMT007 Magazine is packed with insights, innovations, and expert perspectives that you won’t want to miss.
Do You Have X-ray Vision?
Has X-ray’s time finally come in electronics manufacturing? Join us in this issue of SMT007 Magazine, where we answer this question and others to bring more efficiency to your bottom line.
IPC APEX EXPO 2025: A Preview
It’s that time again. If you’re going to Anaheim for IPC APEX EXPO 2025, we’ll see you there. In the meantime, consider this issue of SMT007 Magazine to be your golden ticket to planning the show.
- Articles
- Columns
Search Console
- Links
- Media kit
||| MENU - smt007 Magazine
How to Prevent Solder Bridges During Printed Circuit Board Assembly
August 5, 2016 | Richard Barratt, JJS ManufacturingEstimated reading time: 4 minutes
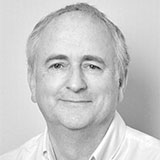
Solder bridges, or "shorts" as they are also known, occur when solder unintentionally connects one electronic component lead to another.
Unfortunately, these are bad news for electronics manufacturers.
They can be difficult to spot – particularly where fine pitch components are involved – and, if unresolved, can end up causing serious damage to the component and/or circuit board.
Thankfully, a large number of solder bridges can be easily prevented. And while preventive measures may end up costing you a small amount of additional time and money, the long term payback can be significant. In this short article, we will look at some of the most common root causes that lead to solder bridges and how to prevent these from occurring.
Root cause
The majority of solder bridges are the result of less than ideal printed circuit board (PCB) design. As demand for smaller/faster technology increases, electronic component manufacturers continue to reduce the package size of their components. Have you seen inside an Apple Watch? It’s mind blowing! Original equipment manufacturers (OEMs), therefore, have an ongoing challenge and sometimes the layout of the circuit board can be compromised in order to get a new product out to market. Of course, issues can also occur during the assembly process but, provided a robust New Product Introduction (NPI) process exists within the company, these should be confined to the first batch.
Issues that can lead to solder bridges include:
- Lack of/insufficient solder resist between pads.
- Pad to gap ratio - especially when the pitch of the device is 0.5mm or below.
- Excessive solder paste applied due to incorrect stencil specification.
- A poor seal between the solder stencil and the PCB, resulting in uneven paste distribution.
- Incorrect stencil thickness.
- Poor registration of the solder screen compared to the PCB.
- Surface mount component placement errors.
One of the most common issues we see relates to the lack of solder resist around fine pitch components. Recently, we saw an issue with a QFN (quad-flat no-leads) package and, following a thorough investigation, found that the resist had been applied in "blocks" around the leads of the device, rather than between each one individually. While this would have been easier for the PCB manufacturer, and arguably helps improve yield, the necessary barrier between lead was not created, which resulted in bridging.
Prevention
It’s important, therefore, to specify and then verify with the bare board manufacturer that they are able to apply solder resist between each lead. If they can’t, due to tight tolerances, a design change may be required around that particular component. Obviously, this is never ideal - particularly when the pressure is on to deliver product out to market - but the alternative could be hours of expensive rework or, worse still, a large number of customer complaints.
When it comes to solder stencil design, we have found that 5 thou (0.127mm) thickness, laser cut, stainless steel stencils, generally work well for 0.5mm pitch devices and 0603 case sizes. For QFNs, 0402 case sizes, resistor networks and 0.4mm pitch devices, we would, however, recommend using laser cut nickel stencils for enhanced paste release and reducing the thickness to 4 thou (0.1mm).
You can use the following formulas to select an appropriate stencil thickness:
Aspect Ratio = Aperture Width (W) / Stencil Thickness (T).
Area Ratio = Area of Pad (LxW) / Area of Aperture Walls (2 x (LxW) x T)
(where L is the aperture length).
Clearly, these are guidelines based on our own experience - you need to ensure any specifications you agree with your stencil supplier produce the levels of quality you expect. If you are experiencing bridging as a result of incorrect placement or excessive paste, you may need to reduce the thickness of the stencil, aperture or change the finish.
In the majority of cases, the standard tooling (designed to hold stencils in place) designed within screen printers is adequate. However, if you are manufacturing a particularly thin PCB, which also contains a number of fine pitch components, you may find the PCB isn’t rigid/flat enough during printing. In these circumstances, it is recommended that dedicated tooling is created, which provides adequate support where needed so that the board remains perfectly flat when printed.
And finally, to eliminate solder bridges occurring during the reflow process, you must always ensure that the oven profile you use meets the specification of the solder paste.
Hopefully, this article has proved useful. Although solder bridges can cause serious headaches for some electronics manufacturers, the majority can be prevented relatively easily. So if you are an OEM looking into outsourcing and have any concerns around the issue, make sure the electronics manufacturing services (EMS) provider you partner with has demonstrable design for manufacture (DFM) experience. Small design changes to the bare board or solder stencil might cost you several hundred pounds but reworking batches of failing PCBAs could end up costing thousands. And that’s before taking into consideration the impact it has on your reputation.
Richard Barratt is a Principal NPI Engineer at JJS Manufacturing.
The post originally appeared on the JJS Manufacturing blog which can be found here.
Suggested Items
Indium’s Karthik Vijay to Present on Dual Alloy Solder Paste Systems at SMTA’s Electronics in Harsh Environments Conference
05/06/2025 | Indium CorporationIndium Corporation Technical Manager, Europe, Africa, and the Middle East Karthik Vijay will deliver a technical presentation on dual alloy solder paste systems at SMTA’s Electronics in Harsh Environments Conference, May 20-22 in Amsterdam, Netherlands.
SolderKing Achieves the Prestigious King’s Award for Enterprise in International Trade
05/06/2025 | SolderKingSolderKing Assembly Materials Ltd, a leading British manufacturer of high-performance soldering materials and consumables, has been honoured with a King’s Award for Enterprise, one of the UK’s most respected business honours.
Knocking Down the Bone Pile: Gold Mitigation for Class 2 Electronics
05/07/2025 | Nash Bell -- Column: Knocking Down the Bone PileIn electronic assemblies, the integrity of connections between components is paramount for ensuring reliability and performance. Gold embrittlement and dissolution are two critical phenomena that can compromise this integrity. Gold embrittlement occurs when gold diffuses into solder joints or alloys, resulting in mechanical brittleness and an increased susceptibility to cracking. Conversely, gold dissolution involves the melting away of gold into solder or metal matrices, potentially altering the electrical and mechanical properties of the joint.
'Chill Out' with TopLine’s President Martin Hart to Discuss Cold Electronics at SPWG 2025
05/02/2025 | TopLineBraided Solder Columns can withstand the rigors of deep space cold and cryogenic environments, and represent a robust new solution to challenges facing next generation large packages in electronics assembly.
BEST Inc. Reports Record Demand for EZReball BGA Reballing Process
05/01/2025 | BEST Inc.BEST Inc., a leader in electronic component services, is pleased to announce they are experiencing record demand for their EZReball™ BGA reballing process which greatly simplifies the reballing of ball grid array (BGA) and chip scale package (CSP) devices.