-
- News
- Books
Featured Books
- smt007 Magazine
Latest Issues
Current IssueIntelligent Test and Inspection
Are you ready to explore the cutting-edge advancements shaping the electronics manufacturing industry? The May 2025 issue of SMT007 Magazine is packed with insights, innovations, and expert perspectives that you won’t want to miss.
Do You Have X-ray Vision?
Has X-ray’s time finally come in electronics manufacturing? Join us in this issue of SMT007 Magazine, where we answer this question and others to bring more efficiency to your bottom line.
IPC APEX EXPO 2025: A Preview
It’s that time again. If you’re going to Anaheim for IPC APEX EXPO 2025, we’ll see you there. In the meantime, consider this issue of SMT007 Magazine to be your golden ticket to planning the show.
- Articles
- Columns
Search Console
- Links
- Media kit
||| MENU - smt007 Magazine
Bumping of QFNs/LGAs and Other Leadless Devices for More Consistent Rework
August 9, 2016 | Bob Wettermann, BEST Inc.Estimated reading time: 2 minutes
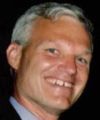
The Challenge
Leadless devices are now the greatest package style by volume (Yole Development Market Survey) being placed by electronics assemblers worldwide. These packages, due to a variety of factors, are challenging to rework. Among the greatest challenges this package presents are the solder voiding primarily on the ground plane, the inability to clean underneath the devices post rework, and the difficulty in getting similar standoff heights on both the IO and center ground. These challenges along with their increasing complexity and ever smaller package sizes challenge even the most skilled rework technicians.
In addition to the above rework challenges, the package style itself remains very difficult to inspect post reflow for a variety of reasons. As there are rarely any visible solder joints due to in most instances a lack of a solderable sidewall on the IO pads of the device, as well as the very low standoff distances between the bottom of the device and the PCB, there is very little visual inspection which can occur. This means that the reliance on a skilled x-ray technician as well as a capable x-ray system is in order.
Types of Rework Methods Available
Of the various methods for reworking leadless devices, the bumping method (Figure 1), when appropriate for the board and part at hand, is the process with the greatest first pass yield, the one with the greatest standoff distance for cleaning flux residue from underneath the device and the one with the greatest assurance of minimizing voiding.
Figure 1: Bumped leadless device prior to placement.
"Bumped" 2 x 2mm QFN Package, 0.5mm pitch, 0.2mm Wide Pads
There are numerous methods being used to rework leadless devices; either guided by the older IPC 7711 5.4.1 process guidelines or by the newest stenciling techniques. The older of these methods includes solder paste printing on the site location of the PCB followed by the placement and reflow of the device. The newer methods including IPC 7711 procedures 5.8.1.1 and 5.8.1.2 includes the device pads being “bumped” followed by their placement. The device, post “bumping”, can be placed using a rework system using paste flux or with a properly-designed “capture” stencil which has apertures that can locate and capture the “bumps” on the PCB.
Both of these latter methods for reworking leadless devices were popularized using polyimide stencils. In these methods, a polyimide stencil is placed over the land patterns on the bottom of the device. Solder paste is then squeegeed in to the apertures. The device is then reflowed. Post reflow, the stencil is peeled off leaving “bumps” on the bottom of the device (mini metal stencils can also be used when appropriate). Because the reflow is done in air, the flux volatiles can escape, thereby having the “bumped” part nearly free of voids. In addition, these stencils are thicker than the initial manufacturing stencils meaning that the final standoff height is greater when compared to traditional printing and placement. This bumping technique also greatly simplifies placement of the leadless device as a lower-skilled technician or even first-timer, when following the instructions properly, can produce the “bumps” for placement.
To read this entire article, which appeared in the August 2016 issue of SMT Magazine, click here.
Suggested Items
Indium’s Karthik Vijay to Present on Dual Alloy Solder Paste Systems at SMTA’s Electronics in Harsh Environments Conference
05/06/2025 | Indium CorporationIndium Corporation Technical Manager, Europe, Africa, and the Middle East Karthik Vijay will deliver a technical presentation on dual alloy solder paste systems at SMTA’s Electronics in Harsh Environments Conference, May 20-22 in Amsterdam, Netherlands.
SolderKing Achieves the Prestigious King’s Award for Enterprise in International Trade
05/06/2025 | SolderKingSolderKing Assembly Materials Ltd, a leading British manufacturer of high-performance soldering materials and consumables, has been honoured with a King’s Award for Enterprise, one of the UK’s most respected business honours.
Knocking Down the Bone Pile: Gold Mitigation for Class 2 Electronics
05/07/2025 | Nash Bell -- Column: Knocking Down the Bone PileIn electronic assemblies, the integrity of connections between components is paramount for ensuring reliability and performance. Gold embrittlement and dissolution are two critical phenomena that can compromise this integrity. Gold embrittlement occurs when gold diffuses into solder joints or alloys, resulting in mechanical brittleness and an increased susceptibility to cracking. Conversely, gold dissolution involves the melting away of gold into solder or metal matrices, potentially altering the electrical and mechanical properties of the joint.
'Chill Out' with TopLine’s President Martin Hart to Discuss Cold Electronics at SPWG 2025
05/02/2025 | TopLineBraided Solder Columns can withstand the rigors of deep space cold and cryogenic environments, and represent a robust new solution to challenges facing next generation large packages in electronics assembly.
BEST Inc. Reports Record Demand for EZReball BGA Reballing Process
05/01/2025 | BEST Inc.BEST Inc., a leader in electronic component services, is pleased to announce they are experiencing record demand for their EZReball™ BGA reballing process which greatly simplifies the reballing of ball grid array (BGA) and chip scale package (CSP) devices.