-
- News
- Books
Featured Books
- pcb007 Magazine
Latest Issues
Current IssueSales: From Pitch to PO
From the first cold call to finally receiving that first purchase order, the July PCB007 Magazine breaks down some critical parts of the sales stack. To up your sales game, read on!
The Hole Truth: Via Integrity in an HDI World
From the drilled hole to registration across multiple sequential lamination cycles, to the quality of your copper plating, via reliability in an HDI world is becoming an ever-greater challenge. This month we look at “The Hole Truth,” from creating the “perfect” via to how you can assure via quality and reliability, the first time, every time.
In Pursuit of Perfection: Defect Reduction
For bare PCB board fabrication, defect reduction is a critical aspect of a company's bottom line profitability. In this issue, we examine how imaging, etching, and plating processes can provide information and insight into reducing defects and increasing yields.
- Articles
- Columns
- Links
- Media kit
||| MENU - pcb007 Magazine
Spirit Circuits: Building a New Factory in Romania...
August 23, 2016 | Barry Matties, I-Connect007Estimated reading time: 10 minutes
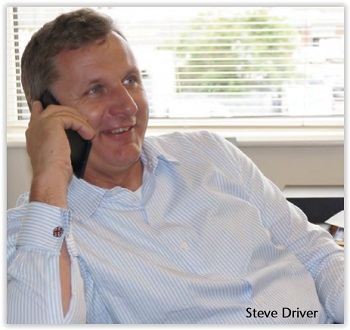
Recently I sat down with Managing Director Steve Driver of Spirit Circuits. We discussed the company’s future, and the interesting decision to build a new facility in Craiova, Romania, and how Whelen’s Alex Stepinski influenced the design.
Barry Matties: Steve, we’re sitting at your facility in what appears to be a sunny day here in England.
Steve Driver: Absolutely. Every day is sunny in England.
Matties: That’s why I carry my umbrella.
Driver: It’s a myth. The rain’s a myth.
Matties: I just went on a nice tour of your facility, and it looks like you guys are doing some interesting things with metal backed boards here, but you’re also setting up a new facility in Romania at the moment. Let’s just jump right into that, since I’ve already spoken with your managing director, Martin Randall, about what you’re doing here. Tell me about what you are planning to do in the future, in Romania.
Driver: The Romanian project is customer-driven. We have a dominance in the LED PCB sector. More than 30% of our business revenues here are on LED boards. We have a high demand for metal backed PCBs, single-sided PCBs using CEM-1 or FR-4 laminates. Nobody wants to make it any more. It’s expensive to come from China because the freight is killing it. The freight is 20–25% of the landed cost. So we’re building our first plant in Romania and it’s going to be for single-sided PCB manufacturing. We have the building ready. The containers are being loaded with the equipment now. Pilot production will be around the September/October time frame. We have 12 employees here from Romania being trained, with another four arriving on the 30th.
Matties: What sort of manufacturing is this? You were talking about a fully automated process, is that the idea?
Driver: For Phase 1, no. Phase 1 is using all the equipment we’ve got. We have made several acquisitions over the last few years, so we’ve got a whole bunch of PCB equipment around us. That is going to be installed in the next few months. It will be a standard shop using standard technology—screen printing, photo mechanical, etching, drilling, routing—with some new equipment from Viking and Technic. For Phase 2 we plan to install the Lunaris machine from Mutracx and have a digital section of the factory. This will be Q1 2017. Then we have a plan for Phase 3 to build a turnkey digital PTH shop.
Matties: That’s still pretty close. That’s a pretty aggressive timeline from Phase 1 to Phase 3.
Driver: It is, and we are 14–15 months into this project. The due diligence and the bureaucracy and getting everything organized has been a lot slower than we’d perhaps have liked. We are building a bespoke single-side PCB shop. There is already a lot of competition in the PTH and multilayer market. We feel that Spirit Circuits has had a good model here for the last 15–16 years on 1–8 layer quick-turn. Over eight layers we’ve got strong competition in the UK anyway so we’ve concentrated on the lower end, but do it well, do it quick, and with a specialism in thermal management. We have very good thermal engineers working for us and we give customers an educated choice on what materials they choose to use. We don’t ally ourselves with any one particular manufacturer of materials, but we do extensive testing and we do design and offer some assembly as well.
Matties: Why did you choose that location over this one?
Driver: The footprint in Romania is the attraction. Most people want to say it’s the labor cost. Currently the labor cost is of course an attraction, but it won’t stay that way, as it didn’t in Poland or the Czech Republic. It’s the actual footprint. The building, the land and the utilities are all low-cost. It’s a low-cost central Eastern European location. To put it in context, the electricity is one-third of the cost per kilowatt hour to that of the UK, water is one-third of the cost of the UK, and the local government taxes are one-tenth of the cost. Our total cost of operation is so much less expensive than being here. Why Romania? Also in Romania, location is pretty important. A lot of our business is dealing with contract manufacturers in the Czech Republic, Germany, Hungary, and France. Probably 40% of our business now is in Europe and we see more of our customers moving over into the central and Eastern European locations. Romania itself wasn’t our first choice. We looked at other countries like Bulgaria and Macedonia, but we’ve had very good encouragement from the educated workforce that’s available in Romania. There is also the opportunity for European funding, which we haven’t had any yet but that we’re hoping to get. We’re coming down into the Southwest of Romania, whereas in the Northwest at the moment there is quite good development there. We’ve got big companies like Flextronics and Kimball that are already very well established up in Timisoara. We’re down in Dolj County at a town called Craiova, where there is still some government assistance available and where there’s still around 10% unemployment. We have our first 16 employees here. None of them have PCB experience. They are here at Spirit for two to three months for training. There isn’t any significant PCB manufacturing in Romania so we are completely starting from zero with our skill base and knowledge base.
Matties: That could be a big plus actually.
Driver: I’d like to think so. We want to be a little bit disruptive with some of our processes and not have any preconceived ideas. We are also very keen to work with the universities. We’ve aligned ourselves with a couple of universities where there are some very intelligent young people coming out of university with not very good prospects in the towns that they are living in. There are some very large companies in Craiova that have shed lots of jobs, so we are able to offer some encouragement to these people.
Matties: Aside from perhaps economics, why wouldn’t you start with the Phase 3 model? I understand you have the equipment in hand.
Driver: We don’t have the demand and the risk is mitigated in what we’re doing because everything that we’re going to be making in Romania we currently buy in China, so we’re going there with an order book. If we were to start with something different to what we currently have as orders, we’d then have to go and fill the plant, whereas we are building this now where one customer already satisfies one shift. Our whole objective of this is to repatriate some of the work that we’re doing in China, where we have a very small margin, and give our customers better agility. If we bring product by sea, you’re typically looking at 10–12 week total lead times, and customers are changing their minds during that period. Bring it by air and we lose the margin on the freight, so we’re doing this with a known order book. That’s what is mitigating the risk and that’s the attraction.
Page 1 of 2
Suggested Items
IPC-CFX, 2.0: How to Use the QPL Effectively
07/02/2025 | Chris Jorgensen, Global Electronics AssociationIn part one of this series, we discussed the new features in CFX Version 2.0 and their implications for improved inter-machine communication. But what about bringing this new functionality to the shop floor? The IPC-CFX-2591 QPL is a powerful technical resource for manufacturers seeking CFX-enabled equipment. The Qualified Product List (QPL) helps streamline equipment selection by listing models verified for CFX compliance through a robust third-party virtual qualification process.
Technica USA Announces New Strategic Partnership with I.T.C. Intercircuit Production GmbH
06/24/2025 | Technica USATechnica USA is pleased to announce a new distribution and representative agreement with I.T.C. Intercircuit Production GmbH, a globally recognized manufacturer of advanced equipment for the PCB manufacturing industry.
Smart Automation: The Power of Data Integration in Electronics Manufacturing
06/24/2025 | Josh Casper -- Column: Smart AutomationAs EMS companies adopt automation, machine data collection and integration are among the biggest challenges. It’s now commonplace for equipment to collect and output vast amounts of data, sometimes more than a manufacturer knows what to do with. While many OEM equipment vendors offer full-line solutions, most EMS companies still take a vendor-agnostic approach, selecting the equipment companies that best serve their needs rather than a single-vendor solution.
Mesa West, Advanced West Announce Strategic Partnership
06/15/2025 | I-Connect007Mesa West is proud to announce that they have officially joined forces with Advanced West. This strategic partnership brings together two industry leaders, uniting strengths to better serve customers through enhanced capabilities, expanded offerings, and continued commitment to quality.
Evolve Manufacturing Celebrates 100 Years of Combined Leadership in Medical Device Manufacturing
05/26/2025 | Evolve ManufacturingEvolve Manufacturing Inc., a leading provider of end-to-end contract manufacturing services for medical device and life sciences instrument companies, proudly celebrates 100 years of combined medical device leadership among its expert team.