-
- News
- Books
Featured Books
- pcb007 Magazine
Latest Issues
Current IssueSales: From Pitch to PO
From the first cold call to finally receiving that first purchase order, the July PCB007 Magazine breaks down some critical parts of the sales stack. To up your sales game, read on!
The Hole Truth: Via Integrity in an HDI World
From the drilled hole to registration across multiple sequential lamination cycles, to the quality of your copper plating, via reliability in an HDI world is becoming an ever-greater challenge. This month we look at “The Hole Truth,” from creating the “perfect” via to how you can assure via quality and reliability, the first time, every time.
In Pursuit of Perfection: Defect Reduction
For bare PCB board fabrication, defect reduction is a critical aspect of a company's bottom line profitability. In this issue, we examine how imaging, etching, and plating processes can provide information and insight into reducing defects and increasing yields.
- Articles
- Columns
- Links
- Media kit
||| MENU - pcb007 Magazine
The Story Behind the News: Ventec’s IMS Manufacturing Capabilities in China Doubled
September 19, 2016 | Pete Starkey, I-Connect007Estimated reading time: 10 minutes
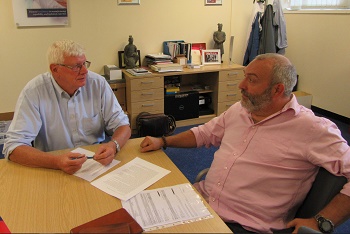
In this interview conducted at Ventec Europe’s headquarters in Leamington Spa, UK, Ventec Europe & USA COO Mark Goodwin sat down with I-Connect007 Technical Editor Pete Starkey to share the details of Ventec International Group’s $2 million equipment investment. With this injection of new equipment, Ventec doubles its IMS material manufacturing capacity in China.
Starkey: Mark, your news release announced that Ventec International Group has invested 2 million dollars, which doubles your capacity to manufacture insulated metal substrate materials in Jiangyin, China. I first saw your IMS manufacturing facility in Suzhou back in 2011, and it was evident then that Ventec had gone to great lengths to address all of the critical factors specific to meeting, and in many cases surpassing, the demands the market was making at that time. What changes have you seen in the last five years?
Goodwin: The first big change was to move on beyond prepreg technology, which was based on our core capability proven over many years of laminate production, using glass fabrics loaded with thermally conductive resin systems, bonded between aluminium as the heat sink and copper as the conductor. The big limitation with that construction is that glass is a very good thermal, as well as electrical insulator, and because our objective is to get the heat out of products, we need thermal conductivity as well as electrical insulation between the heat sink and the conductor. So the major development in technology from what you saw in 2011 to where we are today is that, as well as producing the lower 1.6−2.2-watt thermal performance materials based on woven glass prepreg, we now produce a range of materials, our B-Series, with un-reinforced thermally conductive dielectrics, in the 3.0−10.0-watt range. Taking the glass out significantly improves the thermal conductivity of the insulation layer, and hence you can get heat from the component to the heatsink much more efficiently, particularly useful in high power LED lighting applications.
Starkey: So how has the market demand grown?
Goodwin: Frankly speaking, I don’t have a good handle on the global demand numbers. I know what the demand is for our products—hence we’ve doubled our capacity! Our materials are heading more and more into the automotive lighting space—this is the big driver for us. And the baseline technology for this is a 3-watt material with a dielectric thickness in the range 50 to 100 microns, depending on the customer’s electrical breakdown strength and hi-pot requirements. Obviously the dielectric thickness influences both the electrical and the thermal performance of the material. The thinner the dielectric, the lower the thermal impedance, and vice versa.
Starkey: And would I be right in assuming that in the case of these thin-dielectric materials, when you haven’t got the benefit of the glass fabric to effectively act as a mechanical spacer, you rely very heavily on advances in process engineering and process control to maintain the critical insulation thickness?
Goodwin: That’s been a big driver in the investment we’ve just made. It’s not just been a matter of increasing capacity, we’ve obviously made engineering changes to the equipment to give us tighter control over dielectric thickness, particularly at the 50-micron level. You need better thickness control at this level both to maintain the insulating capabilities of the material—not forgetting that you’ve got the treatment side of the copper foil to fully encapsulate—and to achieve the thermal impedance characteristics the customer requires. This is an ongoing challenge; there are still plans for improvement and we will make further process control enhancements as we continue to run the new equipment. I do know that when we put in the third line we will probably make more engineering changes in line with the ongoing requirements of a developing market.
Starkey: Something that was apparent to me from early on, and I know that your OEM technology team has made a lot of progress in this area, was the challenge of educating the designer in understanding what were the real material characteristics and how to meaningfully define thermal conductivity. In some cases, I believe they were not sure exactly what they were asking for.
Goodwin: I see much less of that today, predominantly because we’re working, not exclusively, but largely, in the automotive lighting sector. The engineering teams at these suppliers of LED lighting, as well as product lines like E-motors and DC power converters, to the automotive business, tend to have a higher level of engineering capability than typical manufacturers of domestic or municipal lighting, which was the business we were talking about five years ago. The guys we’re working with now have a good understanding of materials and a clear vision of what they are trying to achieve. They are pushing us in two directions: thinner dielectrics and higher thermal conductivity. We can make down to 50 microns and up to 10.0 watts per metre kelvin, although the combination of 10.0 watts and 50 microns is probably the practical limit of our technology at the moment and I’m not sure we could deliver it in volume—but we certainly can at 75 microns.
Starkey: What challenges have been encountered and overcome in the IMS manufacturing process to achieve the ultimate in product quality?
Goodwin: The challenges have been two-fold. We have already talked about thickness control in coating. The other challenge is controlling the flow, and hence maintaining thickness control, over the full area of the bonded IMS panel. To produce a sandwich of copper foil, un-reinforced dielectric and aluminium, you’ve obviously got to have some flow. You can’t afford any micro-voids because these would be potential sites for short circuits between aluminium and copper, and you have to maintain hi-pot capability. For example, at the end of our new line everything is edge-linished to remove the copper from the edge of the panel, so that we can do in-line hi-pot testing on every B-series panel produced.
Starkey: Mark, talking about panels, what panel size is typical in manufacture?
Goodwin: The general demand is for sizes like 600 mm x 500 mm or 610 mm x 510 mm. In the B-series, we produce up to 610 mm width and the length in the machine direction is limited only by the size of the press plates, typically 1225 mm. We normally bond the material as two half-sheet panels on full-sheet copper & press plates.
Page 1 of 2
Suggested Items
I-Connect007 Editor’s Choice: Five Must-Reads for the Week
07/18/2025 | Nolan Johnson, I-Connect007It may be the middle of the summer, but the news doesn’t quit, and there’s plenty to talk about this week, whether you’re talking technical or on a global scale. When I have to choose six items instead of my regular five, you know it’s good. I start by highlighting my interview with Martyn Gaudion on his latest book, share some concerning tariff news, follow that up with some promising (and not-so-promising) investments, and feature a paper from last January’s inaugural Pan-European Design Conference.
Elephantech Launches World’s Smallest-Class Copper Nanofiller
07/17/2025 | ElephantechJapanese deep-tech startup Elephantech has launched its cutting-edge 15 nm class copper nanofiller – the smallest class available globally. This breakthrough makes Elephantech one of the first companies in the world to provide such advanced material for commercial use.
Copper Price Surge Raises Alarms for Electronics
07/15/2025 | Global Electronics Association Advocacy and Government Relations TeamThe copper market is experiencing major turbulence in the wake of U.S. President Donald Trump’s announcement of a 50% tariff on imported copper effective Aug. 1. Recent news reports, including from the New York Times, sent U.S. copper futures soaring to record highs, climbing nearly 13% in a single day as manufacturers braced for supply shocks and surging costs.
I-Connect007 Editor’s Choice: Five Must-Reads for the Week
07/11/2025 | Andy Shaughnessy, Design007 MagazineThis week, we have quite a variety of news items and articles for you. News continues to stream out of Washington, D.C., with tariffs rearing their controversial head again. Because these tariffs are targeted at overseas copper manufacturers, this news has a direct effect on our industry.I-Connect007 Editor’s Choice: Five Must-Reads for the Week
Digital Twin Concept in Copper Electroplating Process Performance
07/11/2025 | Aga Franczak, Robrecht Belis, Elsyca N.V.PCB manufacturing involves transforming a design into a physical board while meeting specific requirements. Understanding these design specifications is crucial, as they directly impact the PCB's fabrication process, performance, and yield rate. One key design specification is copper thieving—the addition of “dummy” pads across the surface that are plated along with the features designed on the outer layers. The purpose of the process is to provide a uniform distribution of copper across the outer layers to make the plating current density and plating in the holes more uniform.