-
- News
- Books
Featured Books
- smt007 Magazine
Latest Issues
Current IssueWhat's Your Sweet Spot?
Are you in a niche that’s growing or shrinking? Is it time to reassess and refocus? We spotlight companies thriving by redefining or reinforcing their niche. What are their insights?
Moving Forward With Confidence
In this issue, we focus on sales and quoting, workforce training, new IPC leadership in the U.S. and Canada, the effects of tariffs, CFX standards, and much more—all designed to provide perspective as you move through the cloud bank of today's shifting economic market.
Intelligent Test and Inspection
Are you ready to explore the cutting-edge advancements shaping the electronics manufacturing industry? The May 2025 issue of SMT007 Magazine is packed with insights, innovations, and expert perspectives that you won’t want to miss.
- Articles
- Columns
- Links
- Media kit
||| MENU - smt007 Magazine
The Complex World of Soldering
May 1, 2017 | Stephen Las Marias, I-Connect007Estimated reading time: 11 minutes
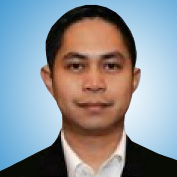
Industry veteran Happy Holden and Saline Lectronics Senior Process Engineer Cathy Cox discuss the various challenges and issues that users face in soldering, including the lack of a "one-size-fits-all" approach in the process, and some key factors that the PCB assembly industry should consider when it comes to different applications and markets.
Stephen Las Marias: What do you think are the greatest challenges when it comes to soldering in PCB assembly?
Cathy Cox: I would have to say our challenges are temperature. Temperature is a big problem with the flex boards. With the circuit board being so thin, actually getting the right temperature to be able to run them through a reflow is definitely a challenge.
Happy Holden: Picking a final finish that’s compatible with the solder that you picked in the flux. There’s no one answer that fits all. So picking that, and then you might say defending it—when people are selling different combinations—is a pretty big challenge, especially when not all the criteria for evaluation and testing is readily available. I've come to learn that the wetting balance really isn’t reliable to use that much anymore.
Our end-use applications are so diverse that when you talk about any particular subject, it’s tough for people to apply. ‘Does this apply to me or is he talking about the other guy over there?’ For instance, flex assembly and soldering is a particular challenge; but when I think of soldering, I think of rigid boards and I think of standard size thinner ones. When you get to really thick—over 2 mm—type boards, getting lead-free solder up to a milling temperature is a real challenge. There, you have to worry about the materials you built the boards for. It’s a huge industry, and how you carve it up is part of the challenge.
My life for years has been in automotive electronics. The company I work for is one of the highest volume assembler of automotive electronics in the Western hemisphere. Soldering is not really a problem except for new devices, QFNs and things like that that are coming on the market. It’s a process that’s running extremely smooth.
Las Marias: Do you think lead-free soldering continues to be an issue when it comes to reliability?
Holden: The industry has already moved to lead-free soldering. That was done a long time ago. It’s only the military and avionics and a few hold outs that haven’t moved to lead free. I talked to people at the APEX show that were in the military, and they realize that their time is running short because they have fewer and fewer people who support them. If you're going to lead free then, unlike tin lead where there wasn’t much variety, now you’ve got a whole proliferation of solders and different compatibility with final finishes, and different suitability for reliability life. That’s one reason why it’s so difficult because depending on what you’re assembling for, the answers maybe different.
Cox: I totally agree with Happy. At Saline Lectronics, the majority of our customers are doing lead free. Lead free is definitely more of a challenge with flex boards just due to the temperature. Getting good solder joints is definitely a challenge, but it’s a challenge that most companies are up for, so it's good. We need new things in our industry.
Las Marias: Do miniaturization, increased board densities, and shrinking component sizes impact the soldering process from your perspective?
Cox: I don't know if they necessarily affect it from what I can see. We deal with a lot of the 0201s. We're pretty excited to get our hands on 01005s and start playing with them and see if our pick-and-place machines can handle them. We'll need more precise placements to be able to make sure you get a good solder joint. It will be a little bit more challenging for an operator to manually inspect a board with solder joints being so small. But we have our high-tech AOI equipment, so that should not be a problem for us.
Patty Goldman: So, you don’t see very many of those types of components?
Cox: We see very small components all the time, but the smaller they get will be a challenge. I don't think it’s a challenge that’s going to stop us from doing anything. It’s just a different way of looking at it; it’s a different way of manufacturing it. You have to have more precise placement, make sure the thickness on your solder paste machines are proper, and I think it’s going to be awesome.
Goldman: What's your biggest bugaboo, then?
Cox: Our biggest with flex boards would actually be our pallets that we use in surface mount to keep our boards flat during the reflow. We can set pallets up for all different types of boards, but getting one to fit completely flat in there every time, and make sure the components are going to sit flat when they go through reflow, is a challenge. Most of the time, it's the bigger components that we see issues with because there’s a bigger area to have a bubble in the flex board.
Las Marias: Is solder jetting catching up with the paste printing process?
Holden: My last six years have been in high-volume production, and solder paste printing and the integral AOI machines are going to be tough to match in terms of jetting. Jetting may be much more applicable to high-mix, low-volume, but for the high-volume automobile market, mobile phones, consumer products, paste printing is pretty well defined and highly robust. Jetting maybe coming along, but it will have a hard time matching the fancy step stencils and some of the other techniques developed in stencil printing. But it may be totally adequate for high mix. I’ve never seen or we’ve never used any jetting equipment except for inkjet printing or solder mask printing in the PCB area. I don’t have a lot of experience with it, but any kind of jetting like that, be it inkjet, solder mask, or solder, really has not met the needs of volume manufactures to be cost effective, not yet. It’s for the prototype or high mix.
Las Marias: Does solder paste selection or qualification still matter today despite the standard solder types used in certain applications?
Holden: Yes, because they’re constantly improving solder paste and things like that. You're kind of always evaluating tweaks and minor improvements to see what it does, especially when one of our focuses in the past has been voiding and the micro-voiding you had with lead free. We haven't rejected products but we'd liked to eliminate it. Those are constantly minor tweaks in the formulation of the solder paste and the refill profile.
Las Marias: I understand solder voiding is still a big issue in the industry. Cathy, how do you tackle voiding?
Cox: We go with Indium solder paste. We have a really good connection with them. They help us through a lot of our issues with incisions, voids, stuff like that. We have been trying a few things here in our shop with changing the amount of paste that we put on a stencil, removing the mask around the pads so that the air can actually escape between the component and the solder pad. We've seen some success with that. The IPC standard keeps getting more and more vague on voiding under QFNs or even in through-hole components. We took it upon ourselves to kind of set our own standards, making sure that we have anything under 25% under a component or within a barrel fill. With our window pane and with reducing the solder mask around the pads, we’ve been successful in minimizing voiding to about 25% with our QFNs, BGAs.
Page 1 of 2
Suggested Items
Seeing a Future in Mexico
07/09/2025 | Michelle Te, I-Connect007The Global Electronics Association (formerly known as IPC) has been instrumental in fostering a partnership with Guanajuato, a state north of Mexico City with 12 industrial clusters and close to 150 companies involved in electronics. This past spring, Alejandro Hernández, the undersecretary for investment promotion in Guanajuato, attended IPC APEX EXPO 2025 at the invitation of IPC Mexico Director Lorena Villanueva, where he met with several companies to discuss the opportunities available in Mexico. He is inviting electronics-related companies seeking long-term investment in a centrally located area with access to highways, railways, and ports.
The Global Electronics Association Releases IPC-8911: First-Ever Conductive Yarn Standard for E-Textile Application
07/02/2025 | Global Electronics AssociationThe Global Electronics Association announces the release of IPC-8911, Requirements for Conductive Yarns for E-Textiles Applications. This first-of-its-kind global standard establishes a clear framework for classifying, designating, and qualifying conductive yarns—helping to address longstanding challenges in supply chain communication, product testing, and material selection within the growing e-textiles industry.
IPC-CFX, 2.0: How to Use the QPL Effectively
07/02/2025 | Chris Jorgensen, Global Electronics AssociationIn part one of this series, we discussed the new features in CFX Version 2.0 and their implications for improved inter-machine communication. But what about bringing this new functionality to the shop floor? The IPC-CFX-2591 QPL is a powerful technical resource for manufacturers seeking CFX-enabled equipment. The Qualified Product List (QPL) helps streamline equipment selection by listing models verified for CFX compliance through a robust third-party virtual qualification process.
The Knowledge Base: A Conference for Cleaning and Coating of Mission-critical Electronics
07/08/2025 | Mike Konrad -- Column: The Knowledge BaseIn electronics manufacturing, there’s a dangerous misconception that cleaning and coating are standalone options, that they operate in different lanes, and that one can compensate for the other. Let’s clear that up now. Cleaning and conformal coating are not separate decisions. They are two chapters in the same story—the story of reliability.
Advancing Aerospace Excellence: Emerald’s Medford Team Earns Space Addendum Certification
06/30/2025 | Emerald TechnologiesWe’re thrilled to announce a major achievement from our Medford, Oregon facility. Andy Abrigo has officially earned her credentials as a Certified IPC Trainer (CIT) under the IPC J-STD-001 Space Addendum, the leading industry standard for space and military-grade electronics manufacturing.