-
- News
- Books
Featured Books
- smt007 Magazine
Latest Issues
Current IssueWhat's Your Sweet Spot?
Are you in a niche that’s growing or shrinking? Is it time to reassess and refocus? We spotlight companies thriving by redefining or reinforcing their niche. What are their insights?
Moving Forward With Confidence
In this issue, we focus on sales and quoting, workforce training, new IPC leadership in the U.S. and Canada, the effects of tariffs, CFX standards, and much more—all designed to provide perspective as you move through the cloud bank of today's shifting economic market.
Intelligent Test and Inspection
Are you ready to explore the cutting-edge advancements shaping the electronics manufacturing industry? The May 2025 issue of SMT007 Magazine is packed with insights, innovations, and expert perspectives that you won’t want to miss.
- Articles
- Columns
- Links
- Media kit
||| MENU - smt007 Magazine
AOI Capabilities Study with 03015 Components
June 14, 2017 | David Geiger, et al., Flex InternationalEstimated reading time: 4 minutes
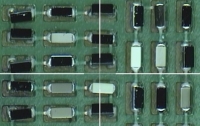
Abstract
Automated optical inspection (AOI) is advantageous in that it enables defects to be detected early in the manufacturing process, reducing the cost of repair as the AOI systems identify the specific components that are failing removing the need for any additional test troubleshooting. Because of this, more electronic contract manufacturing services (EMS) companies are implementing AOI into their SMT lines to minimize repair costs and maintain good process and product quality, especially for new component types. This project focuses on the testing of component package 03015 which is challenging for AOI.
Highly-automated and effective test methods are becoming a more and more important topic in our industry today. Advances in modern manufacturing technologies have been making factories smarter, safer, and also more environmentally sustainable. Finding and implementing smart machines which provide real time information is critical to success. Currently, we have been successful in using 2D/3D AOI for production; however not for the upcoming 03015 components. Therefore, we are working with AOI vendors to ensure successful testing of this component type, with a special emphasis on optimizing algorithm threshold settings to detect defects.
We have been working with five AOI vendors with five test vehicles (PCBAs). Each PCBA board has 246 components with three different pitch sizes (100 µm, 150 µm, 200 µm). The results of Attribute GR&R, Defect Escapes, and False Call PPM (parts per million) will be presented.
Based on the data which we received up to now, every set of data (five sets—still waiting for results of AOI System 3) is from the algorithms of 2D AOI, although some machines have the 3D AOI capability. These machines have shown different levels of performance. AOI System 5’s results have an excellent acceptable level for Attribute GR&R; both AOI System 5 and AOI System 6 have only several percentage points of a Defect Escape rate. However, this study is just in its infancy; more improvement and testing will be performed. We will continue to provide new test results from all suppliers.
Introduction
The printed circuit board assembly (PCBA) industry has long embraced the smaller, lighter, faster mantra for electronic devices, especially in recent years. With the increasing use of smaller components, more consideration is required to study and implement changes; not only for SMT processes, but also for testing. There have been some studies conducted for SPI (solder paste inspection) with 03015 components, however, there are very few recommended practices for AOI.
The 03015 [0.3 mm x 0.15 mm] device is a microchip component. For reference, please note that a human hair is approximately 0.1mm. To ensure a successful implementation of the 03015 components, besides for these three critical areas—placement equipment, assembly materials, and process control—the capabilities of machines used to test these component types is another critical consideration. Now, 3D SPI is more commonly used in the SMT process, and 3D AOI is quickly catching up.
During the initial stage of our study, we first tested these five boards with 03015 components on our 2D AOI machine in our Milpitas manufacturing site. Next, we provided the boards to the R&D labs of five AOI vendors who all have 3D AOI machines. Working with various R&D engineers, it was obvious this was a challenging task for their current AOI systems, especially for 3D AOI systems due to component reflection.
Our test data and results showed that the 2D AOI machines have different capabilities in detecting defects for 03015, such as misalignment, tombstoning, and shorts. While the defect escape percentage decreased, false call PPM increased, therefore, optimized programming should be based on test data analysis.
Experiments
In total, we asked five AOI vendors (R&D engineers) to work on this project. We received four sets of test data—AOI System 3 data is to be provided later. The test procedure is the same for all machines with five boards.
Test Vehicle
Figure 1: Company Miniaturized Test Vehicle
Five boards with 03015 components were tested on the AOI machines. Figure 1 is our test vehicle, which has three areas for different pitch sizes. The pitch areas are indicated as different color arrows: red color (A – 100 µm), yellow color (B – 150 µm), and blue color (C – 200 µm).
The 03015 component was a production resistor: 292 µm, 143 µm, and 100 µm corresponding to its length, width, and height, respectively, as shown in Figure 2, where area A is without fab mask. There are a total of 87, 81, and 78 components in areas A, B, and C, respectively. The pad size (length, width) is 150 µm by 150 µm on the PCB fab. Figure 3 shows pictures for area A (right column), area B (center column), and area C (left column); after print (top row), after placement (center row), and after reflow (bottom row). There are different colors for optical pictures due to 03015 component reflection, which increased AOI testing difficulty.
Figure 2: Three areas of 03015 components.
Figure 3: Optical picture: after print (top), after placement (center), and after reflow (bottom).
To read the full version of this article, which appeared in the June 2017 issue of SMT Magazine, click here.
Suggested Items
Driving Innovation: Direct Imaging vs. Conventional Exposure
07/01/2025 | Simon Khesin -- Column: Driving InnovationMy first camera used Kodak film. I even experimented with developing photos in the bathroom, though I usually dropped the film off at a Kodak center and received the prints two weeks later, only to discover that some images were out of focus or poorly framed. Today, every smartphone contains a high-quality camera capable of producing stunning images instantly.
Hands-On Demos Now Available for Apollo Seiko’s EF and AF Selective Soldering Lines
06/30/2025 | Apollo SeikoApollo Seiko, a leading innovator in soldering technology, is excited to spotlight its expanded lineup of EF and AF Series Selective Soldering Systems, now available for live demonstrations in its newly dedicated demo room.
Indium Corporation Expert to Present on Automotive and Industrial Solder Bonding Solutions at Global Electronics Association Workshop
06/26/2025 | IndiumIndium Corporation Principal Engineer, Advanced Materials, Andy Mackie, Ph.D., MSc, will deliver a technical presentation on innovative solder bonding solutions for automotive and industrial applications at the Global Electronics A
Fresh PCB Concepts: Assembly Challenges with Micro Components and Standard Solder Mask Practices
06/26/2025 | Team NCAB -- Column: Fresh PCB ConceptsMicro components have redefined what is possible in PCB design. With package sizes like 01005 and 0201 becoming more common in high-density layouts, designers are now expected to pack more performance into smaller spaces than ever before. While these advancements support miniaturization and functionality, they introduce new assembly challenges, particularly with traditional solder mask and legend application processes.
Knocking Down the Bone Pile: Tin Whisker Mitigation in Aerospace Applications, Part 3
06/25/2025 | Nash Bell -- Column: Knocking Down the Bone PileTin whiskers are slender, hair-like metallic growths that can develop on the surface of tin-plated electronic components. Typically measuring a few micrometers in diameter and growing several millimeters in length, they form through an electrochemical process influenced by environmental factors such as temperature variations, mechanical or compressive stress, and the aging of solder alloys.