-
- News
- Books
Featured Books
- pcb007 Magazine
Latest Issues
Current IssueVoices of the Industry
We take the pulse of the PCB industry by sharing insights from leading fabricators and suppliers in this month's issue. We've gathered their thoughts on the new U.S. administration, spending, the war in Ukraine, and their most pressing needs. It’s an eye-opening and enlightening look behind the curtain.
The Essential Guide to Surface Finishes
We go back to basics this month with a recount of a little history, and look forward to addressing the many challenges that high density, high frequency, adhesion, SI, and corrosion concerns for harsh environments bring to the fore. We compare and contrast surface finishes by type and application, take a hard look at the many iterations of gold plating, and address palladium as a surface finish.
It's Show Time!
In this month’s issue of PCB007 Magazine we reimagine the possibilities featuring stories all about IPC APEX EXPO 2025—covering what to look forward to, and what you don’t want to miss.
- Articles
- Columns
Search Console
- Links
- Media kit
||| MENU - pcb007 Magazine
Schmid: Bringing Integrated Solutions to the Market
January 8, 2018 | Barry Matties, I-Connect007Estimated reading time: 9 minutes
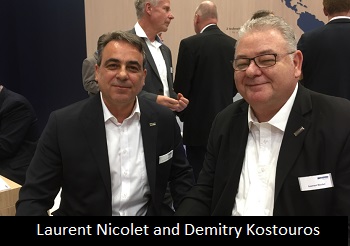
With China’s recent shift towards quality, the next generation of PCB fabrication equipment must target yields and include the ability to track those yields, says Schmid’s Laurent Nicolet and Demitry Kostouros. Barry Matties recently sat down with these two gentlemen to talk more about the market shift and Schmid’s introduction of their new vertical line aimed at carving a niche in the market.
Barry Matties: Another trade show…how is this one going for you and for Schmid?
Laurent Nicolet: Yes, another strong trade show. It's a lot of trade shows in a short period, but productronica is very important because we are a German company. We represent Germany, which was a very important market for us. An important part of our turnover is done in Germany and we are presenting our newest, mainly our new generation of vertical line, which is really something. I would say the challenges we experienced with generation one have been solved with generation two.
Matties: Such as?
Nicolet: One big point is the utility consumption, a 20% reduction globally, and the 30% price reduction. The machines really become more affordable for everybody. On the machine we present a new concept with single panel handling. With digital requirements on the substrate market we really tranform our thinking to single panel handling through a frame and a tray.
Matties: The machine itself is for which process?
Nicolet: Actually, we show a developer for the modified semi-additive process (mSAP), which is one of the critical processes in the market today. Immediately available are lines for surface preparation or bond process, flash etching, resist developing and solder mask developing, and now we are finalizing the stripping and metallization processes. In the near future we will have continuity with our new plating development where we will integrate immersion process in the vertical line.
Matties: Nice, so it's a modular system; people can pick and choose, "I want this or that," and it pulls it together?
Kostouros: Yes, it's a modular system but it's also very well factory-integrated because you will find that Schmid is involved not only in processing equipment but also automation, handling, and intralogistics systems. The name of the game here is integration of advanced technologies for the IC substrate market and the HDI-plus market. And going to market with processes that address the touch-free panel space. As you will see here in our booth, there's our ready-to-market solution in our Infinity V+ technology. It's plug and play. The modular space-saving, energy-saving, smaller overall environmental footprint aspect of V+ provides flexibility to the customer for all spray applications, immersion applications and touch-free frame transport for sub-25micron thick panels. So we're looking forward to speaking to all the advanced players in the industry.
Matties: Is this primarily for a quick-turn environment such as Europe or North America?
Nicolet: I would say it's really for mass production and that means mainly Asia. Some companies in the U.S. will be interested, but mainly it's Asia. And mainly focused in the beginning on the substrate market or the mSAP processes. Soon, a lot of other markets and other segments of the PCB production will slowly move in that direction because they need to go to more volume of less than 50-micron line and space. And below that, the subtractive process is not very capable. So sooner or later they will go that direction.
Matties: China is a highly competitive market; how do you go there and be successful?
Nicolet: In China, there are two types of companies. I would say the Western companies, which are active in China that have a very good understanding of the relationships between price, technology and quality. And then you have Chinese companies moving towards higher quality and yields, looking more in depth at investing in higher quality machines to improve yield performance in their factories. We experience more competition in Asia where the local vendors sell their machine per meters pricing. X meters of developer costs X USD…. But this is for low cost applications.
Matties: You mentioned automation—that's also very big in China as well?
Kostouros: Automation technology is also part of the diversified DNA of Schmid. Unlike most other suppliers, we can provide solutions that are not necessarily tied to chemical wet processing. Besides our wet processing equipment we can provide solutions that include handling automation, intralogistics and vacuum such as plasma desmearing applications. By integrating these technologies we are answering our customer’s full spectrum market requirements that are not being fully addressed by existing equipment providers.
Matties: Part of the automation is what we can see at the booth here?
Nicolet: Yes, I would say that is just for demonstration, to have the demo system running continuously. But we are looking at a proven intralogistics solution such as AGV. Due to heavier PCB production we may need to transport at least a 60-panel stack from process to process on the manufacturing floor. This system what we show here can be an alternative to current technologies to reach a cleanroom, or to change from one manufacturing area to another.
Matties: So we have an issue coming out on new technologies, and when you're developing a piece of equipment, what drives the technology? You mentioned lower consumption of electricity and lower cost, but what's the impetus behind the design?
Nicolet: First, it's what is required in the market in the future. Not just tomorrow, but after that. And then make the machine relatively flexible so that we can reach the after-tomorrow target.
The main driver for us is trying to show the yield. That is one of the drivers for the future. The yield requirements of high-end PCBs, if they have embedded components, anything like that, it's getting very high. And if we talk about 0.1% yield gain for the customer, it's a huge amount at the end of the year.
So, it's really the manufacturing quality, and the quality of the transport of the panel, because we learned that handling is the big cure for yield. We’ve worked on this single panel process to be sure to increase the yield.
Matties: When you talked about lowering the costs by 30%, how did you achieve that?
Nicolet: We completely reworked the design of the our vertical system, now named the Infinity V+. We have tried to combine and standardize components as well as simplify design aspects of our system. This reduces the manufacturing costs. We have enhanced the spray design as well as the immersion zones and have completely reworked the frame clamping system. We had to make a very simple clamping system, which can follow the panel through all the processes—very important. And in comparison of the previous one, we reduced ten times the cost of the clamper.
Page 1 of 2
Suggested Items
'Chill Out' with TopLine’s President Martin Hart to Discuss Cold Electronics at SPWG 2025
05/02/2025 | TopLineBraided Solder Columns can withstand the rigors of deep space cold and cryogenic environments, and represent a robust new solution to challenges facing next generation large packages in electronics assembly.
BEST Inc. Reports Record Demand for EZReball BGA Reballing Process
05/01/2025 | BEST Inc.BEST Inc., a leader in electronic component services, is pleased to announce they are experiencing record demand for their EZReball™ BGA reballing process which greatly simplifies the reballing of ball grid array (BGA) and chip scale package (CSP) devices.
Indium Wins EM Asia Innovation Award
05/01/2025 | Indium CorporationIndium Corporation, a leading materials provider for the electronics assembly market, recently earned an Electronics Manufacturing (EM) Asia Innovation Award for its new high-reliability Durafuse® HR alloy for solder paste at Productronica China in Shanghai.
Summit Interconnect Hollister Elevates PCB Prototyping with New TiTAN Direct Imaging System from Technica USA
05/01/2025 | Summit Interconnect, Inc.Summit Interconnect’s Hollister facility has recently enhanced its quick-turn PCB prototyping capabilities by installing the TiTAN PSR-H Direct Imaging (DI) system.
KOKI Expands U.S. Sales Coverage with Multiple New Representatives
04/29/2025 | KOKIKOKI, a global leader in advanced soldering materials and process optimization services, is pleased to announce the expansion of its U.S. sales network with the addition of three new manufacturers’ representative firms: Assembled Product Specialists, Diversitech Reps Inc., and Eagle Electronics.