-
- News
- Books
Featured Books
- smt007 Magazine
Latest Issues
Current IssueSpotlight on India
We invite you on a virtual tour of India’s thriving ecosystem, guided by the Global Electronics Association’s India office staff, who share their insights into the region’s growth and opportunities.
Supply Chain Strategies
A successful brand is built on strong customer relationships—anchored by a well-orchestrated supply chain at its core. This month, we look at how managing your supply chain directly influences customer perception.
What's Your Sweet Spot?
Are you in a niche that’s growing or shrinking? Is it time to reassess and refocus? We spotlight companies thriving by redefining or reinforcing their niche. What are their insights?
- Articles
- Columns
- Links
- Media kit
||| MENU - smt007 Magazine
Mycronic Announces the Acquisition of Vi TECHNOLOGY
February 21, 2018 | Barry Matties, I-Connect007Estimated reading time: 7 minutes
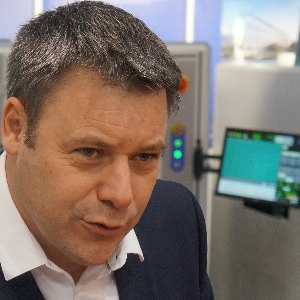
Recently, at productronica, Mycronic announced the acquisition of Vi TECHNOLOGY with the intent of combining VIT’s inspection technology with Mycronic’s jetting capabilities. In an interview with I-Connect007, Olivier Pirou, Managing Director of VIT, discusses more about the merger and how this will help VIT contend in such a competitive environment.
Barry Matties: Olivier, please tell us a little bit about what's going on.
Olivier Pirou: It's a very recent acquisition that the Mycronic group did, and this is the meeting of two converging strategic views. The one from VI Technology being positioned as an inspection integrated solution provider compliant with Industry 4.0 requirements. And Mycronic ambition to play a major role in this era, and we figured out that joining forces quite nicely with the process equipment portfolio that Mycronic has been commercializing for a long time, and the inspection & process control technology that VI technology is bringing to the table. So together we will enable a full line solution offering. This new acquisition that really set the path to the Industry 4.0 synergies and greater value proposition that we are looking to further develop soon. So, that's the rationale behind it.
Matties: Can you tell me a little bit about how you came to this position?
Pirou: I've been with VI technology for 13 years, and before that I was working a major EMS player. Within VI Technology I've been in the company from product management, marketing, R&D as well, and for the last seven years I’ve run operations with our former CEO. So that's the position I'm in, and within Mycronic world, VIT will remain a legal entity fully integrated in the group. I will be the Managing Director for this activity. Of course, the first synergies are intending to leverage the sales channel and the R&D efforts, so that will really bring a lot of exciting opportunities for both partners.
Matties: So you grew up at VI?
Pirou: Yes, before that I worked eight years for Sanmina-SCI, in France. I developed in the program and key account management, working for instance for Philips at the time coordinating eight different operations throughout the world.
Matties: So with your background from Sanmina-SCI, and more importantly with VIT from all the different positions that you've held, R&D and such, you're in a perfect position to really lead this company it sounds like. You have a depth of knowledge that nobody else would have.
Pirou: This is effectively very exciting, and I know the company very well. I’m really excited to develop the company further and the projects of VI Technology within the Mycronic group.
Matties: One of the things that has caught my attention over at Mycronic is their jet printing, and then the inspection technology here; how do you merge these two together when you’re making your presentation to your customers?
Pirou: What we usually encounter in printing work is that 70% of the defects come from the printing process. This is where 3D SPI developed. Actually, the PI system that you see behind you is kind of a revolution. It’s a new generation SPI system and on top of excellent inspection capabilities and excellent speed, what it brings uniquely is the ease of use. this machine is an auto-programmed machine, it’s so easy to use in any kind of environment, from high volume to low volume line mix, especially when quality is mission critical for customers in high reliability applications like medical and military space, this is a very innovative piece of equipment. It ties on so nicely with the jetting technology that it will overcome many of the intrinsic obstacles of printing, and the idea is not to control the process into a full process solution, but work together to optimize the first pass yield of the line.
Matties: When you look at the process in its totality, you're eliminating so many steps that even still, there may be advantage.
Pirou: Sure. A lot of people are looking in terms of capacity or component per hour, where everybody should also look at the utilization rate of the asset that they've bought. In this new industry era, customization, built to order is getting even more than important even in the high-volume space and low-volume, high-mix. The utilization rate, because the changeovers are so frequent, is getting very important.
Matties: In the inspection space, there's a lot of competition, and a lot of different technologies. What do you see happening here? Is there room for everybody? Does adding Mycronic maybe give you an advantage above the others?
Pirou: This is an arena with surprisingly quite fierce competition. I think the fierce competition also came worldwide from the shift of the industry encountered in the last 20 years from the West and the East, with the emergence of new players, and I would say historical players remained very strong. Because we manage to adapt to this shift through, of course, price competitiveness, but through innovation, differentiation and technology differentiation. This is the game that VIT has played the last few years to be able to compete in a stiff environment, by differentiating through innovation.
We invested a lot of money in technology to bring this auto-programmed machine. We did that for the SPI system, and we did that for the SIGMA web-based software suite that is really easy to use. We also are transferring this technology to our last 3D AOI system, which has been known to be so reliable and so helpful in this kind of environment where high reliability is required. So, we managed through this strategy to be again in the lead path. This is very important because the industry is really going towards autonomation, meaning an autonomous system. This cannot be done through degrading or simplifying too much, or degrading the metrology, the accuracy or the repeatability of the system.
Actually, it’s on the contrary. Now you are in a world where you need accurate data, clean data, so that from this data you can automate. You cannot automate with awkward data. And it's called ‘big data’ because the machine is actually generating as much data in a day than a small bank. You need to have clean data and this enables then actionable information.
Matties: Something that you can actually go back and improve your process with. What drives the technology and how do the customers play in the development of that technology?
Pirou: In the inspection space it is quite simple. First, it's cycle time. The inspection technology is an unproductive technology. It cannot be bottleneck in the SMT line. So, we have to follow the pace of high speed lines, and the productivity per square meter is increasing everywhere. It is really very important to be fast. Secondly, the quality requirements are getting stringent, and to some extent, even more stringent sometimes than the IPC 610 class 3 requirements.
We transition from inspection to metrology to automatic optical metrology. So, you need to have that capability. Last but not least, if that went well, ease of use is getting more and more important. Those are really the three priorities in our business.
Matties: What's your favorite part of your job?
Pirou: I’m really excited to bring people together to deliver such a system. This is what is really exciting in our industry, and especially in vision because. We need to be state of the art from the electronics to the acquisition computing, vision, algorithms, optics obviously. To make such a system, it's really great to assemble all these technologies, and it's even more exciting when you reach a global footprint in terms of operations and service. To be able to deploy all these technologies to the customers. So, trying to bring all this talent together to serve the market is really exciting for me.
Matties: How will the relationship with Mycronic work? How do the cultures fit?
Pirou: You pointed out a very important point. The success of the position also greatly relies not only on product but a lot of on people, and on culture. At least from the first step that I have had within the Mycronic group there is this compatibility of cultures and values that we share, this passion for technology, this passion for people, this passion for business. This fits very well with how VI Technology developed over the years. So, we are now part of the European group with a management culture that is highly compatible and rooted also in an innovation DNA that we share. To me, this is really a good match.
Matties: That’s probably the first and most important aspect to a merger. There must be alignment.
Pirou: With productronica, this is really a perfect timing for all of us to spread the good news. Even between our teams now they’re getting integrated and they will be a seamless team soon. It's exciting on both sides to put the machines together to deliver better value and to either advocate the advantage of jet printing or the quality of the PI measurement systems. So that really is a great combination.
Matties: Well congratulations, this is very exciting news.
Pirou: Thank you.
Testimonial
"The I-Connect007 team is outstanding—kind, responsive, and a true marketing partner. Their design team created fresh, eye-catching ads, and their editorial support polished our content to let our brand shine. Thank you all! "
Sweeney Ng - CEE PCBSuggested Items
ViTrox Unveils Smart 3D AOI Solutions, Pioneering Dual-Sided Inspection and Robotic Vision Solutions for Back-end Assembly Processes
08/04/2025 | ViTroxViTrox, which strives to be the World’s Most Trusted Technology Company, proudly announces the launch of its new-generation innovations in Automated Optical Inspection (AOI) technology for back-end assembly processes.
TRI Unveils New Platform for Diverse Board Sizes
07/14/2025 | TRITest Research, Inc. (TRI), the leading test and inspection systems provider for the electronics manufacturing industry, proudly introduces a new size configuration for SPI and AOI Models.
Smarter Machines Use AOI to Transform PCB Inspections
06/30/2025 | Marcy LaRont, PCB007 MagazineAs automated optical inspection (AOI) evolves from traditional end-of-process inspections to proactive, in-line solutions, the integration of AI and machine learning is revolutionizing defect reduction and enhancing yields, marking a pivotal shift in how quality is managed in manufacturing.
SolderKing’s Successful Approach to Modern Soldering Needs
06/18/2025 | Nolan Johnson, I-Connect007Chris Ward, co-founder of the family-owned SolderKing, discusses his company's rapid growth and recent recognition with the King’s Award for Enterprise. Chris shares how SolderKing has achieved these award-winning levels of service in such a short timeframe. Their secret? Being flexible in a changing market, technical prowess, and strong customer support.
ZETWERK Enhances Manufacturing Capabilities with TRI
06/04/2025 | TRITest Research, Inc. (TRI), the leading test and inspection systems provider for the electronics manufacturing industry, is pleased to announce that ZETWERK Electronics has integrated TRI's Automated Optical Inspection (AOI) and Solder Paste Inspection (SPI) solutions into its state-of-the-art manufacturing facility in Tamil Nadu.