-
- News
- Books
Featured Books
- pcb007 Magazine
Latest Issues
Current IssueInventing the Future with SEL
Two years after launching its state-of-the-art PCB facility, SEL shares lessons in vision, execution, and innovation, plus insights from industry icons and technology leaders shaping the future of PCB fabrication.
Sales: From Pitch to PO
From the first cold call to finally receiving that first purchase order, the July PCB007 Magazine breaks down some critical parts of the sales stack. To up your sales game, read on!
The Hole Truth: Via Integrity in an HDI World
From the drilled hole to registration across multiple sequential lamination cycles, to the quality of your copper plating, via reliability in an HDI world is becoming an ever-greater challenge. This month we look at “The Hole Truth,” from creating the “perfect” via to how you can assure via quality and reliability, the first time, every time.
- Articles
- Columns
- Links
- Media kit
||| MENU - pcb007 Magazine
PCB Manufacturing (R)evolution in the Making
April 11, 2018 | Stephen Las Marias, I-Connect007Estimated reading time: 16 minutes
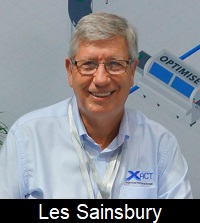
At the recent HKPCA and IPC Show 2017 in Shenzhen, China, I was able to interview Les Sainsbury, CEO, and Andrew Kelley, CTO, of XACT PCB, as well as Alex Stepinski, vice president of Whelen Engineering’s PCB Fab Business Unit, to discuss process evolution and technology developments in the PCB manufacturing industry.
Stephen Las Marias: Les, for anyone who’s not familiar with XACTPCB , give us a quick background.
Les Sainsbury: There's sometimes some confusion around XACT because we have a software system but we're not software people. We consider ourselves unique; we're actually PCB manufacturing guys….. We developed the software system to solve PCB manufacturing problems. We are currently the world leader in PCB registration control systems. Very specifically our target market are companies manufacturing technology product, if I can use very broad terms, HLC ,HDI , Flex and Flex Rigid boards.
Our first sale was about 10 years ago; now, having enjoyed enormous success we have a leadership position in the PCB manufacturing world. For XACT to accurately control registration processes in real time, we have to interface with other manufacturing systems and machines, it’s part of our DNA. Guess what? As an industry we have started to talk about Industry 4.0, Smart Manufacturing, Smart Factory, and other terminology’s where interfaces between machines, equipment and systems are critical. XACT has always connected to machines and equipment so that we can access data, so we find ourselves today in a very enviable position to take advantage of Smart Manufacturing initiatives that require communication between discrete machines and devices.
As there is no current IPC standard for PCB manufacturing in terms of machines communicating with each other, we have had to develop a very open business model for writing interfaces; we look to connect to everything and so can control everything. An easy thing to say, but very difficult to execute as it relies so much on a mix of experience, technology and capabilities.
We have an intelligent manufacturing system that collects data, models behavior patterns, and actually predicts in real time. Critical to our capability is we have to have reliable and accurate data. To this end you've got to have reliable and accurate machines. Which begs a question as we are here in China “Is the China market ready?”. From XACT’s experience we would have to say its work in progress, historically domestic manufacturers do seem to have gone with lower cost machinery (a just enough approach). Therefore, capability becomes an issue with regards to being able to do many of the things necessary to move towards a real “ lights out operation “ , but certainly you can start diming the lights. PCB manufacturing does not lend itself easily to 4.0 and mass process automation specifically, because to date, real traceability at an inner layer processing level has not been possible. Frankly for most people you build it, you get to the end of the line, electrically test and go, “Oh, it doesn't work.”
Las Marias: How long have you been in China?
Sainsbury: Our first Chinese customer was booked in 2006? Back then being a startup, we used local agents supplemented by regular sales visits from the UK. As we grew it became obvious that we needed our own local staff, this move has resulted in a lot of success and momentum. We have a sales cycle that frankly requires experts, we have seen this in the USA and Europe, China is no different — we are pcb registration experts engaging with the customers experts.
Las Marias: Has the market evolved in that time ?
Sainsbury: Obviously the market has changed. Today the Chinese government says 2025 initiative, Industry 4.0, all those Smart Factory terms, senior management are influenced by this and are asking us to advise them how we do it. The guys on the shop floor are going, ‘Yeah, we’ve heard there’s a new machine, a new system.’ In practical terms I think we will meet in the middle. Some companies will go full lights out, others will implement automation, others some aspects of smart factory. We can do that. The great thing about our system is you can implement on a step-by-step basis. You don’t have to do the whole factory. There’s a model that says you can incrementally get to be a lights-out factory. It’s a pretty long road. I'm not quite sure we're going to get there in my life time. Certainly it will get more automated.
Las Marias: What is the challenge in convincing people to adapt those advanced technologies?
Sainsbury: It depends on the level. I think, if you’re engaging with senior management, ‘convincing’ is an absolute word. I think they’re receptive to it and would like to know more. We’re seeing real manufacturing challenges coming from today’s designs and there’s recognition that better equipment and intelligent systems are needed. A people only approach of attracting and retaining skilled people ,training them to manufacture today’s challenging products in a repeatable manner is no longer a sustainable strategy.
Even if senior management in China recognize the need I think the general workforce in China still has a culture of “a glass ceiling”, when it comes to transmitting new ideas/needs upwards. The engineers might know, but they’re not willing to tell their boss that they need to change. In the West, we don’t seem to be as uncomfortable in pushing our bosses when change is required. Obviously, China will get there, but the cultural aspect just seems to slow that whole development process down. But we recognize it, so we try to work with it. At the management level, I think there's certainly a ‘we’re not sure what to do, but a realization that we need to be doing something.
Las Marias: Are you seeing competition here for your industry?
Sainsbury: If you look at our core business registration control, it’s a very complicated process issue and therefore requires a sophisticated solution. Our system is intelligence driven, based on bespoke algorithms that we have developed over many years, it looks at behavioral patterns. We see no one in our market place reaching the levels of capability that we have, in our experience normally the customers “”human expert”” is the competition.
Now, to move that up a level to Smart Manufacturing you’re talking many aspects, I think there are many unforeseen challenges, we don’t know yet because it’s not been done before .The big question in my mind is confusion .Are you confused about Smart Manufacturing? Why? Because you hear so many phrases like China 2025, 4.0 and other Smart Factory initiatives such as cyber physical systems. The customer has to be confused. He knows, he wants to be more automated, but then automation itself means different things to different people.
Many companies say they are automated when in reality they have automated their material handling with conveyors that may have a robot stacking. In our mind, that's not automation. Automation is process control, automation not material handling.
So where do XACT see itself in this emerging landscape? We’re not an MES system. We’re not an ERP system. There isn’t a neat acronym to describe what we do; we would describe ourselves as “a PCB shop floor intelligent process control company”. We do not solve the entire 4.0 puzzle but we do see ourselves as a very important piece of the future PCB manufacturing 4.0 challenge. We are very much on the factory floor, very much talking to the engineers and saying, ‘How are we going to solve this problem? How can we help you?’
That's not for every shop of course. We are focused on providing PCB companies the ability to adopt a step-by-step approach to smart manufacturing. We don't try to promote, ‘We can solve your entire manufacturing problems.’ No, we solve the basics first, and then we integrate with your MES, ERP or PRE-CAM or CAM system. Our core products already communicate with all those installed systems so we have a solid foundation to build upon for anyone wishing to implement a Smart Manufacturing project.
Page 1 of 2
Testimonial
"The I-Connect007 team is outstanding—kind, responsive, and a true marketing partner. Their design team created fresh, eye-catching ads, and their editorial support polished our content to let our brand shine. Thank you all! "
Sweeney Ng - CEE PCBSuggested Items
KIC Expands Footprint in Mexico to Deliver Faster, Localized Support
08/29/2025 | KICKIC, a leading provider of thermal process solutions for electronics manufacturing, has announced the expansion of its service capabilities in Mexico.
SEMICON Europa 2025 Spotlights Global Collaborations for European Economic Resilience
08/28/2025 | SEMISEMICON Europa 2025, co-located with productronica, will return to Munich from November 18-21 to mark its 50th anniversary, bringing together global industry leaders, innovators, and policymakers to strengthen Europe’s position in the global semiconductor landscape. Registration is open.
North American EMS Industry Shipments Down 4.1% in July
08/27/2025 | Global Electronics AssociationThe Global Electronics Association announced today the July 2025 findings from its North American Electronics Manufacturing Services (EMS) Statistical Program. The book-to-bill ratio stands at 1.23.
SIA Statement on Semiconductor Tariffs Announcement
08/27/2025 | SIAThe Semiconductor Industry Association (SIA) released the following statement from SIA President and CEO John Neuffer regarding President Trump’s semiconductor tariff announcement.
SMTA Elects New Board Members
08/27/2025 | SMTAThe SMTA is pleased to announce its election results for the Global Board of Directors for the term beginning October 19, 2025. Elizabeth Benedetto, HP Inc.; Pratish Patel, Electronic Interconnect; and Sutharshan Suppiramaniam, SMT Elite Corporation, have been newly elected to the Board of Directors for the term 2025-2028.