-
- News
- Books
Featured Books
- design007 Magazine
Latest Issues
Current IssueShowing Some Constraint
A strong design constraint strategy carefully balances a wide range of electrical and manufacturing trade-offs. This month, we explore the key requirements, common challenges, and best practices behind building an effective constraint strategy.
All About That Route
Most designers favor manual routing, but today's interactive autorouters may be changing designers' minds by allowing users more direct control. In this issue, our expert contributors discuss a variety of manual and autorouting strategies.
Creating the Ideal Data Package
Why is it so difficult to create the ideal data package? Many of these simple errors can be alleviated by paying attention to detail—and knowing what issues to look out for. So, this month, our experts weigh in on the best practices for creating the ideal design data package for your design.
- Articles
- Columns
- Links
- Media kit
||| MENU - design007 Magazine
Excerpt: The Printed Circuit Designer’s Guide to…Flex and Rigid-Flex Fundamentals
June 25, 2018 | Dave Lackey and Anaya Vardya, American Standard CircuitsEstimated reading time: 8 minutes
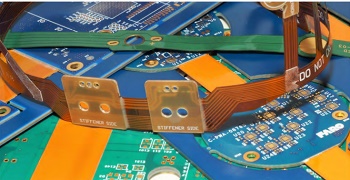
Designing Flex Circuits for First-Pass Success, Part 1
The design process is arguably the most important part of the flex circuit procurement process. The decisions made in the design process will have a lasting impact, for better or worse, throughout the manufacturing cycle. In advance of providing important details about the actual construction of the flex circuit, it is of value to provide some sort of understanding of the expected use environment for the finished product.
The electronics industry serves several different markets that do not always share the same product acceptability or reliability expectations. For this reason, the electronics industry, through IPC and other standards organizations, has developed a classification system that specifies what is expected of products for different classes. The system of classification is not intended to be a measure of quality. Rather, quality is a matter of conformance to a set of established requirements for a product in a given application. Therefore, quality products can be created in each of the classifications within the system. It is generally accepted that there are three classes of product. These have been defined by IPC standards as follows:
- Class 1 – Consumer products and products for non-critical applications where cost is normally the primary driver.
- Class 2 – Higher-order products in terms of quality and reliability expectations, including telecommunications, computers and general industrial.
- Class 3 – High-reliability applications including military, aerospace, automotive and medical products.
By defining the class of the product being designed, the purchaser is letting the manufacturer know what added controls to apply to the manufacturing process and the level of care they will need in the inspection process to ensure that the customer gets the product that is best suited to the application.
The following are discussions on matters of high importance to achieving first-pass success in securing quality flexible circuits from a flex circuit vendor.
It is important to provide some information about the operational requirements for the flex circuit, especially if the circuit is to be used in a dynamic flexing application, such as for a disk drive read/write head assembly. The reason for this is the circuit vendor needs to provide a plan for proper layout strategy for manufacturing; a plan which accounts for the grain direction of the copper foil during the manufacturing process. This is because there is a measurable difference in terms of flexing performance between the machine and transverse directions of the copper foil.
Fabrication Specification Details
After the basic circuit design layout is completed, the next most important piece of information required is the fabrication specification. This document communicates to the fabricator all the pertinent details for the physical construction of the circuit and what is needed and expected in the final product. If this information is incomplete or inaccurate, or if a customer has requirements that cannot be reasonably met by a competent manufacturer, time will be unnecessarily lost, at a cost to both the customer and the vendor. For this reason, it is vitally important that the fabrication specifications are checked and rechecked before putting them out for bid. In the sage words of the master carpenter, “Measure twice, cut once.”
Manufacturing Tolerances
Manufacturing system operators need not only the dimensions of the part they are to manufacture, but also the tolerance for the important features of the product. With flexible circuits, this is something that must be done with thought, care, and consideration of the realities of flexible circuit materials.
With some features, design tolerances may be critical for the performance, fit, or further processing of the product (line widths, spaces, hole sizes, physical separation of features, positional accuracy, etc.). In these cases, the manufacturer can often employ methods to deal with the requirement on a localized basis. In the case of other features, the tolerance may be less critical, significantly less critical, or even non-critical. An important thing to keep in mind is that flexible materials are not as dimensionally stable as rigid materials, and while local features may be held in tight tolerance relative to each other, features from end to end may be less predictable. Given that flexible circuits are normally installed in some 3D form after assembly, the tight tolerances on planar measurements are often not necessary. If there are questions about a tolerance callout, the designer should contact the manufacturing engineer. It is always best to solve the problem before it becomes a problem.
Unclear Layer Designation (Rigid or Flex)
The purpose of a product specification is to provide clear, unambiguous instructions on the product’s construction. In the case of a multilayer circuit design, this is vitally important. The relationship of internal circuit layers relative to one another has become increasingly important in not only assuring that correct interconnections are being made, but also in product performance, especially with controlled impedance designs and signal integrity issues. Several different systems have been developed over the years to help assure that there is no uncertainty in the order of the circuit layers in the final construction. The fabricators engineering staff can provide recommendations if needed. Note the thickness and construction of each core in Figure 1.
Figure 1: Example of four-layer flex construction.
Page 1 of 2
Suggested Items
Silicon Mountain Contract Services Enhances SMT Capabilities with New HELLER Reflow Oven
07/17/2025 | Silicon Mountain Contract ServicesSilicon Mountain Contract Services, a leading provider of custom electronics manufacturing solutions, is proud to announce a significant upgrade to its SMT production capability with the addition of a HELLER 2043 MK5 10‑zone reflow oven to its Nampa facility.
Knocking Down the Bone Pile: Addressing End-of-life Component Solderability Issues, Part 4
07/16/2025 | Nash Bell -- Column: Knocking Down the Bone PileIn 1983, the Department of Defense identified that over 40% of military electronic system failures in the field were electrical, with approximately 50% attributed to poor solder connections. Investigations revealed that plated finishes, typically nickel or tin, were porous and non-intermetallic.
SHENMAO Strengthens Semiconductor Capabilities with Acquisition of PMTC
07/10/2025 | SHENMAOSHENMAO America, Inc. has announced the acquisition of Profound Material Technology Co., Ltd. (PMTC), a premier Taiwan-based manufacturer of high-performance solder balls for semiconductor packaging.
KYZEN to Highlight Understencil and PCB Cleaners at SMTA Querétaro Expo and Tech Forum
07/09/2025 | KYZEN'KYZEN, the global leader in innovative environmentally responsible cleaning chemistries, will exhibit at the SMTA Querétaro Expo & Tech Forum, scheduled to take place Thursday, July 24, at Centro de Congresos y Teatro Metropolitano de Querétaro.
Driving Innovation: Direct Imaging vs. Conventional Exposure
07/01/2025 | Simon Khesin -- Column: Driving InnovationMy first camera used Kodak film. I even experimented with developing photos in the bathroom, though I usually dropped the film off at a Kodak center and received the prints two weeks later, only to discover that some images were out of focus or poorly framed. Today, every smartphone contains a high-quality camera capable of producing stunning images instantly.