-
- News
- Books
Featured Books
- pcb007 Magazine
Latest Issues
Current IssueThe Hole Truth: Via Integrity in an HDI World
From the drilled hole to registration across multiple sequential lamination cycles, to the quality of your copper plating, via reliability in an HDI world is becoming an ever-greater challenge. This month we look at “The Hole Truth,” from creating the “perfect” via to how you can assure via quality and reliability, the first time, every time.
In Pursuit of Perfection: Defect Reduction
For bare PCB board fabrication, defect reduction is a critical aspect of a company's bottom line profitability. In this issue, we examine how imaging, etching, and plating processes can provide information and insight into reducing defects and increasing yields.
Voices of the Industry
We take the pulse of the PCB industry by sharing insights from leading fabricators and suppliers in this month's issue. We've gathered their thoughts on the new U.S. administration, spending, the war in Ukraine, and their most pressing needs. It’s an eye-opening and enlightening look behind the curtain.
- Articles
- Columns
- Links
- Media kit
||| MENU - pcb007 Magazine
The PCB Norsemen: The Velocity of Technology— What Does It Really Mean?
July 2, 2018 | Jan Pedersen, ELMATICAEstimated reading time: 2 minutes
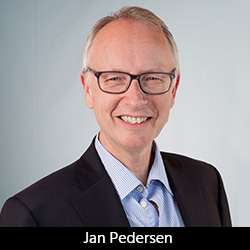
Speed and Direction— Where Are we Going?
The subtitle of IPC APEX EXPO 2018 was “Succeed at The Velocity of Technology.” What did IPC mean by this?
I have not asked the IPC staff what this phrase meant in real terms, but I have my own interpretation. For me, the velocity of technology has two components: speed and direction. The technology in electronics develops faster than ever. A user of mobile phones or computers may not understand the rate at which electronics changes, but if you see the development of components and the complexity of today’s packages, you understand the speed.
Driving a car is probably one of the areas where the user comes in direct touch with the technology development. And we understand the speed when we see how fast we get new versions of smartphones and other gadgets. But in what direction are we going? We all know that size and weight reduction is good. We get more function into the same space. At the same time, we increase the functionality— a mobile phone today can do more than a desktop computer did some years ago. It has a better camera than the reasonably good full-size digital camera we still have in our drawers.
I am a PCB geek. For me, it is interesting to see how technology development has affected the PCB, and in which direction we move. How do we see the velocity of technology in PCBs?
(Almost) Born and Raised in a PCB Plant
I was born in a PCB plant outside Oslo in June 1958. Norway had no PCB factories at that time, so my father saw the potential and started to etch boards in a garage using silkscreened etching resist and ferric chloride etchant. The boards had to be used fast to avoid corrosion; we only had a simple lacquer to protect the copper.
Time went by and at 20-something I was set to lead a small PTH plant. We started to use photoimageable plating resist and infrared re flow for tin-lead (those machines typically had a small fire every week). At that time, we had no RoHS, REACH or ISO 14000 or really any environmental awareness. I have some stories that are better told in more private circles.
In 1992, I joined Elmatica and during the ‘90s we saw some development of PCB technology but mostly just a slight miniaturization. Frankly speaking, the PCB technology itself has not changed that much today either. We still print and etch. We still drill, but we use a laser in addition to the mechanical drills. We still print solder mask, we still plate copper to achieve required thickness and through-hole connections. So, we have seen some changes, but not the speed or change of direction as in other technologies.
The velocity of PCB technology today is still, from my point of view, not at the same rate as we see in components. The introduction of smaller components has almost out-challenged the PCB. But only just. And, we are still in the same direction, so we cannot brag too much about the velocity of the PCB technology.
To read the full version of this article which originally appeared in the May 2018 issue of PCB007 Magazine, click here.
Suggested Items
Hands-On Demos Now Available for Apollo Seiko’s EF and AF Selective Soldering Lines
06/30/2025 | Apollo SeikoApollo Seiko, a leading innovator in soldering technology, is excited to spotlight its expanded lineup of EF and AF Series Selective Soldering Systems, now available for live demonstrations in its newly dedicated demo room.
Indium Corporation Expert to Present on Automotive and Industrial Solder Bonding Solutions at Global Electronics Association Workshop
06/26/2025 | IndiumIndium Corporation Principal Engineer, Advanced Materials, Andy Mackie, Ph.D., MSc, will deliver a technical presentation on innovative solder bonding solutions for automotive and industrial applications at the Global Electronics A
Fresh PCB Concepts: Assembly Challenges with Micro Components and Standard Solder Mask Practices
06/26/2025 | Team NCAB -- Column: Fresh PCB ConceptsMicro components have redefined what is possible in PCB design. With package sizes like 01005 and 0201 becoming more common in high-density layouts, designers are now expected to pack more performance into smaller spaces than ever before. While these advancements support miniaturization and functionality, they introduce new assembly challenges, particularly with traditional solder mask and legend application processes.
Knocking Down the Bone Pile: Tin Whisker Mitigation in Aerospace Applications, Part 3
06/25/2025 | Nash Bell -- Column: Knocking Down the Bone PileTin whiskers are slender, hair-like metallic growths that can develop on the surface of tin-plated electronic components. Typically measuring a few micrometers in diameter and growing several millimeters in length, they form through an electrochemical process influenced by environmental factors such as temperature variations, mechanical or compressive stress, and the aging of solder alloys.
SolderKing’s Successful Approach to Modern Soldering Needs
06/18/2025 | Nolan Johnson, I-Connect007Chris Ward, co-founder of the family-owned SolderKing, discusses his company's rapid growth and recent recognition with the King’s Award for Enterprise. Chris shares how SolderKing has achieved these award-winning levels of service in such a short timeframe. Their secret? Being flexible in a changing market, technical prowess, and strong customer support.