-
- News
- Books
Featured Books
- pcb007 Magazine
Latest Issues
Current IssueVoices of the Industry
We take the pulse of the PCB industry by sharing insights from leading fabricators and suppliers in this month's issue. We've gathered their thoughts on the new U.S. administration, spending, the war in Ukraine, and their most pressing needs. It’s an eye-opening and enlightening look behind the curtain.
The Essential Guide to Surface Finishes
We go back to basics this month with a recount of a little history, and look forward to addressing the many challenges that high density, high frequency, adhesion, SI, and corrosion concerns for harsh environments bring to the fore. We compare and contrast surface finishes by type and application, take a hard look at the many iterations of gold plating, and address palladium as a surface finish.
It's Show Time!
In this month’s issue of PCB007 Magazine we reimagine the possibilities featuring stories all about IPC APEX EXPO 2025—covering what to look forward to, and what you don’t want to miss.
- Articles
- Columns
Search Console
- Links
- Media kit
||| MENU - pcb007 Magazine
Electrolytic Plating: Filling Vias and Through-holes
May 28, 2019 | M. Özkök, S. Lamprecht, A. Özkök, D. Akingbohungbe, and M. Dreiza, Atotech Deutschland Gmbh; and A. Stepinski, Greensource FabricationEstimated reading time: 4 minutes
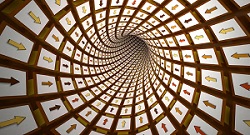
The electronics industry is further progressing in terms of smaller, faster, smarter, and more efficient electronic devices. This continuously evolving environment caused the development of various electrolytic copper processes for different applications over the past several decades.
This article describes the reasons for development and a roadmap of dimensions for copper-filled through-holes, microvias, and other copper-plated structures on PCBs. It will also discuss aspect ratios, dimensions, and results of plated through-holes used today in high-volume manufacturing for microvia and throughhole filling with electroplated copper. Furthermore, this article will also show feasibility studies of new electroplated structures for future applications, such as copper pillar plating on IC substrates.
Four Main Drivers
Four main drivers forced the chemical supply industry to introduce new electrolytic copper processes with the new feature of “filling” capability over the years. The first driver is the continuous miniaturization of electronics. The first blind microvias were introduced with HDI technology in the late 1980s and early 1990s. In 1996, the IC substrate market started to fill the microvias.
“Plugging” technologies were introduced to stack the microvias to save space or create via-in-pad structures. This plugging technology with conductive paste is very expensive because of the additional process steps required. In addition, this technology faced several disadvantages, such as “blow out,” outgassing, smear, and other quality concerns. To achieve the necessary miniaturization benefits, the industry has been leaning towards the completely copper filled blind microvia rather than a plugged microvia as the leading edge solution. Today, copper-filled microvias are the standard for almost all HDI PCB manufacturers.
The second driver is the thermal management on a substrate. One source said it this way:
“As the power and packing density of electronic components increase, the amount of waste heat generated in a small space also rises greatly. This results in dangerously high temperatures, and thus increases the failure risk of electronic devices. Today, 55% of electronic component failures are caused by increased temperatures alone.”
Solutions were needed to integrate features with high thermal conductivity to manage the heat transfer on the substrates from one side to the other to minimize hot spots on the electronic devices over a lifetime. Higher-performing chips tend to generate local hot spots, resulting in material degradation and premature field failure. Integration of thermal vias in high-performance electronics can minimize the occurrence of hot spots; therefore, their utilization in the industry has become more widespread.
In the beginning, thermal vias were nothing more than standard conformal vias, but the thermal conductivity was not good enough. Following that, plugging pastes were introduced to enhance the thermal conductivity of a standard through-hole. But in this case, similar disadvantages of plugging appeared. Meanwhile, complete copper-filled through-holes were realized in 2006 by bridge plating or X-plating technology.
Today, completely copper-filled through-hole structures are at the leading edge of technology for thermal via structures because copper has almost the best thermal conductivity—and it has to be plated, nonetheless.
The third driver is signal frequency. Electronic signal frequencies in an electronic package or inside of a PCB are increasing over time and continue to do so. Stacked microvias and fan-out vias are becoming more and more of a disadvantage for the transmission of high-frequency signals due to creating resistances at high frequencies. Thus, the push of high-frequency applications further increased the demand for technologies like copper-filled through holes. Right now, 5G infrastructure is already using the copper-filled through-hole technology in the field of smartphones.
Figure 1: Patented “SuperFilling” technology.
The fourth driver, especially for through-hole filling, is the quality-and-yield aspect. The alternatives for electroplated copper-filled through-holes require many additional process steps or new materials, such as plugging paste. Each of these additional process steps or materials introduces a variety of risks and manufacturing problems, resulting in a lower yield. Therefore, the “one-step” solution to fill through-holes with copper is the preferred solution without introducing new materials into the PCB.
Microvia Filling With Copper
The filling of microvias with copper was established as a standard in PCB HDI production more than 20 years ago. For example, there was the introduction of supervia filling technology with very low plated-copper thickness on the surface (Figure 1).
Figure 2: Plugged and capped microvia.
Meanwhile, the copper filling of microvias replaced many other filling technologies, such as plugging and capping realized by paste printing and overplating with copper (Figure 2). Both technologies—plugging and capping and copper- filled microvias—enable the so-called via-in-pad structure, which has the advantage for PCB designers. The advantages of the via-in-pad designs are also useful for high-speed designs.
Additionally, copper-filled microvias have significant advantages over plugging technology. For instance, the material inside the microvia is copper while other materials have the potential to outgas or introduce different CTE values. Moreover, voids in copper-filled microvias are far less common than with poorly controlled conventional plugging methods.
The development and introduction of copper-filled microvias opened the door to introduce any layer HDI technology, which enables copper-filled through-holes by stacking the copper-filled microvias. This kind of feature enables HDI board designers the flexibility to create complex signal paths through the PCB by just using copper filled microvias.
Today, almost all critical dimensions of microvias may be filled inclusion-free with copper.
To read the full article, which was published in the April 2019 issue of PCB007 Magazine, click here.
Suggested Items
Elephantech: For a Greener Tomorrow
04/16/2025 | Marcy LaRont, PCB007 MagazineNobuhiko Okamoto is the global sales and marketing manager for Elephantech Inc., a Japanese startup with a vision to make electronics more sustainable. The company is developing a metal inkjet technology that can print directly on the substrate and then give it a copper thickness by plating. In this interview, he discusses this novel technology's environmental advantages, as well as its potential benefits for the PCB manufacturing and semiconductor packaging segments.
Trouble in Your Tank: Organic Addition Agents in Electrolytic Copper Plating
04/15/2025 | Michael Carano -- Column: Trouble in Your TankThere are numerous factors at play in the science of electroplating or, as most often called, electrolytic plating. One critical element is the use of organic addition agents and their role in copper plating. The function and use of these chemical compounds will be explored in more detail.
IDTechEx Highlights Recyclable Materials for PCBs
04/10/2025 | IDTechExConventional printed circuit board (PCB) manufacturing is wasteful, harmful to the environment and energy intensive. This can be mitigated by the implementation of new recyclable materials and technologies, which have the potential to revolutionize electronics manufacturing.
Connect the Dots: Stop Killing Your Yield—The Hidden Cost of Design Oversights
04/03/2025 | Matt Stevenson -- Column: Connect the DotsI’ve been in this industry long enough to recognize red flags in PCB designs. When designers send over PCBs that look great on the computer screen but have hidden flaws, it can lead to manufacturing problems. I have seen this happen too often: manufacturing delays, yield losses, and designers asking, “Why didn’t anyone tell me sooner?” Here’s the thing: Minor design improvements can greatly impact manufacturing yield, and design oversights can lead to expensive bottlenecks. Here’s how to find the hidden flaws in a design and avoid disaster.
Real Time with... IPC APEX EXPO 2025: Tariffs and Supply Chains in U.S. Electronics Manufacturing
04/01/2025 | Real Time with...IPC APEX EXPOChris Mitchell, VP of Global Government Relations for IPC, discusses IPC's concerns about tariffs on copper and their impact on U.S. electronics manufacturing. He emphasizes the complexity of supply chains and the need for policymakers to understand their effects.