-
-
News
News Highlights
- Books
Featured Books
- smt007 Magazine
Latest Issues
Current IssueWhat's Your Sweet Spot?
Are you in a niche that’s growing or shrinking? Is it time to reassess and refocus? We spotlight companies thriving by redefining or reinforcing their niche. What are their insights?
Moving Forward With Confidence
In this issue, we focus on sales and quoting, workforce training, new IPC leadership in the U.S. and Canada, the effects of tariffs, CFX standards, and much more—all designed to provide perspective as you move through the cloud bank of today's shifting economic market.
Intelligent Test and Inspection
Are you ready to explore the cutting-edge advancements shaping the electronics manufacturing industry? The May 2025 issue of SMT007 Magazine is packed with insights, innovations, and expert perspectives that you won’t want to miss.
- Articles
- Columns
- Links
- Media kit
||| MENU - smt007 Magazine
Laserssel Brings High-speed Soldering to New Application Areas
June 10, 2019 | Barry Matties, I-Connect007Estimated reading time: 5 minutes
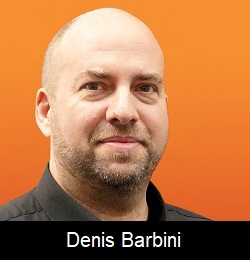
Barry Matties spoke with Denis Barbini, general manager of Laserssel, about the Korean company’s new laser-selective reflow solution aimed at reducing a typical reflow oven’s 10-minute cycle down to just 10 seconds as well as the overall benefits manufacturers could see from streamlining this process.
Barry Matties: Denis, can you tell us a little bit about Laserssel?
Denis Barbini: We are a soldering company focused on using laser technology in a novel way. We started in 2015 performing research and development for this revolutionary technique. We investigated the potential for integration into electronics assembly, and that’s why we are serving the semiconductor, SMT, and rework markets today.
Matties: This is a specialty process. Is the idea that the machine streamlines the hand soldering process?
Barbini: We’re addressing current customer problems with mass soldering, mass convection of reflow of soldering, and wave soldering. We’re taking common defects, such as warpage for a fine-pitch assembly where it is increasingly challenging to achieve proper coalescence, and optimizing those processes to eliminate the warpage to get excellent yield and reliability. We’re also able to process niche applications like flex-on-flex and flex-on-rigid in an automated, in-line process rather than having to utilize hand soldering.
We are identifying industry segments and applications to automate processes where assemblers have had problems over the last few years. The industry is undergoing an explosion of applications, such as new components and designs for IoT and wearables. This requires different ways of soldering. You can’t just use a reflow oven or a wave soldering machine. This technique is very conducive to providing a solution to the current and future assembly challenges.
Matties: In terms of streamlining the process, what are some of the measurable benefits that people will get?
Barbini: Some benefits include improved quality of the soldering joint, reliability of the product, increased units per hour (UPH), and minimized defects with a lower cost of operation in terms of electricity and no inert atmosphere required compared to typical forced convection ovens. When I look at the work that we’ve done, it’s primarily flex-on-flex and automotive batteries, semiconductor devices with pitches of less than 40 microns and die thickness less than 100 microns, and SMT assembly of temperature-sensitive components. While the industry is identifying the potential for low-temperature solders to address specific assembly challenges, this technique mitigates or even eliminates those challenges with SAC alloys. We are enabling them to get that into a mass production environment so that they don’t have to worry about using all of the techniques that are slower and a little bit more cumbersome.
Matties: How long has this equipment been in the marketplace?
Barbini: For the past two and a half years.
Matties: How many installs do you have currently?
Barbini: Now, we have around 40 machines worldwide.
Matties: What has the feedback been?
Barbini: It’s always too good to be true. When we look at semiconductor, their cycle of integrating new technology takes a couple of years. We started with them three years ago, and last week, we installed a new machine at a semiconductor fabrication house where they are now soldering their products in mass volume. We are very excited about that, but it takes time to integrate new technology into the marketplace because we’re comparing joints that were formed by reflow soldering, which everyone knows really well. Today, we are enabling a paradigm shift using our area laser. We can still get high UPH and as good or better quality than reflow.
Matties: This is suitable for what volume of their work? Is 100% of their work running through this, or is it very selective and somewhat niche?
Barbini: Right now, Laserssel is targeting specific applications. However, we see that depending on the application itself, we can potentially solder an entire board in less time than a reflow process. While there is a way to solder the entire product, we’re not out there to replace reflow soldering; we are here to provide customers with solutions to their current challenges and enable them to solder new types of applications that they never thought they could do before.
Matties: What are the general questions that people have about this technology?
Barbini: The first question is usually, “Is my joint quality that’s being formed going to be better or worse?” Because everyone’s used to a certain microstructure, intermetallics, and coalescence. Moreover, we’re taking a process that takes six minutes for reflow and turning it into less than 10 seconds. The next question is, “Are we getting the same dynamics?” about the physical operations taking place in reflow compared to our machine, which is why we’ve taken the time to conduct a two-year study to do just that.
Matties: Do their customers care that it’s going through this process versus a reflow?
Barbini: Initially, the questions come up, so yes, they do.
Matties: How do you satisfy those questions?
Barbini: We’re doing evaluations. Currently, we have two demo centers in the U.S. and one in South Korea. We’re doing a lot of evaluations to prove to the customer that we can do it in an automated fashion with quality.
Matties: Going back to what you just said earlier, it’s typically a 10-minute cycle versus 10 seconds.
Barbini: We’re using the AREA laser. Traditional spot lasers aim at a spot where it applies all of the energy and solders one lead at a time. That’s visible, right? But we’re not doing that. We’re taking that energy and distributing that over an area. It could be 80 by 80 mm or as small as 600 by 300 microns, and the uniform density of energy will solder all of those components equally in that area. By doing that, if you’re giving an 80 by 80 mm, there are a handful of applications that are much smaller than that—such as sensors or automotive or medical applications—so we can process that very quickly.
To read the full article, which appeared in the June 2019 issue of SMT007 Magazine, click here.
Suggested Items
Silicon Mountain Contract Services Enhances SMT Capabilities with New HELLER Reflow Oven
07/17/2025 | Silicon Mountain Contract ServicesSilicon Mountain Contract Services, a leading provider of custom electronics manufacturing solutions, is proud to announce a significant upgrade to its SMT production capability with the addition of a HELLER 2043 MK5 10‑zone reflow oven to its Nampa facility.
Knocking Down the Bone Pile: Addressing End-of-life Component Solderability Issues, Part 4
07/16/2025 | Nash Bell -- Column: Knocking Down the Bone PileIn 1983, the Department of Defense identified that over 40% of military electronic system failures in the field were electrical, with approximately 50% attributed to poor solder connections. Investigations revealed that plated finishes, typically nickel or tin, were porous and non-intermetallic.
SHENMAO Strengthens Semiconductor Capabilities with Acquisition of PMTC
07/10/2025 | SHENMAOSHENMAO America, Inc. has announced the acquisition of Profound Material Technology Co., Ltd. (PMTC), a premier Taiwan-based manufacturer of high-performance solder balls for semiconductor packaging.
KYZEN to Highlight Understencil and PCB Cleaners at SMTA Querétaro Expo and Tech Forum
07/09/2025 | KYZEN'KYZEN, the global leader in innovative environmentally responsible cleaning chemistries, will exhibit at the SMTA Querétaro Expo & Tech Forum, scheduled to take place Thursday, July 24, at Centro de Congresos y Teatro Metropolitano de Querétaro.
Driving Innovation: Direct Imaging vs. Conventional Exposure
07/01/2025 | Simon Khesin -- Column: Driving InnovationMy first camera used Kodak film. I even experimented with developing photos in the bathroom, though I usually dropped the film off at a Kodak center and received the prints two weeks later, only to discover that some images were out of focus or poorly framed. Today, every smartphone contains a high-quality camera capable of producing stunning images instantly.