-
- News
- Books
Featured Books
- smt007 Magazine
Latest Issues
Current IssueWhat's Your Sweet Spot?
Are you in a niche that’s growing or shrinking? Is it time to reassess and refocus? We spotlight companies thriving by redefining or reinforcing their niche. What are their insights?
Moving Forward With Confidence
In this issue, we focus on sales and quoting, workforce training, new IPC leadership in the U.S. and Canada, the effects of tariffs, CFX standards, and much more—all designed to provide perspective as you move through the cloud bank of today's shifting economic market.
Intelligent Test and Inspection
Are you ready to explore the cutting-edge advancements shaping the electronics manufacturing industry? The May 2025 issue of SMT007 Magazine is packed with insights, innovations, and expert perspectives that you won’t want to miss.
- Articles
- Columns
- Links
- Media kit
||| MENU - smt007 Magazine
Reflow Your Solder and Your Data for Industry 4.0
June 11, 2019 | Nolan Johnson, I-Connect007Estimated reading time: 4 minutes
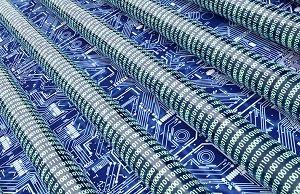
I-Connect007 Managing Editor Nolan Johnson recently spoke with KIC President and Founder Phil Kazmierowicz and Manager of Applications and Sales MB “Marybeth” Allen as they each transitioned into new roles in the KIC leadership team. The conversation ultimately turned to the current dynamics in the industry, particularly Industry 4.0 and streamlining processes.
To kick off the discussion, Johnson posed this question: "Generally speaking, there are two key parts to improving the efficiencies: faster, more accurate throughput, and increased uptime. From your perspective, watching the reflow process, what do you see as the greatest activity in the market for reducing the likelihood of the reflow process becoming the facility’s bottleneck?"
Kasmierowicz, Allen, and Johnson then delved into this question throughout a series of conversations and emails, which have been edited into the discussion that follows.
Faster, More Accurate Throughput
On the topic of throughput, Allen wrote, "A key component to an efficient manufacturing operation is optimization throughout the factory. One of the most effective ways to optimize is via software. Trial and error are a thing of the past. Optimization software not only assists with productivity but also defines and improves the process for the highest quality result. The optimization process for reflow starts in the early stages of setting up a product for solder reflow."
Allen continued, "Finding the correct recipe for a reflow oven to produce a PCB within the current, very tight, lead-free process windows could take significant amounts of both resources and time. Our predictive software tools assist a customer to find this recipe very quickly, likely in just two passes, which significantly reduces the amount of time just to set up a profile. In addition, our predictive software can give a customer an in-spec profile without even running a trial PCB. These two functions alone provide solutions for fast profiling for a high-quality product and within the specifications of the factory’s requirements, which include faster throughput, lower energy costs, and, of course, difficult and challenging assemblies with a variety of process windows between components and solder paste."
Phil Kazmierowicz explained the details. "Once the specification was defined mathematically, we invented the process window index, or PWI, which represents profile quality with a single number. In this way, oven recipes could be compared, allowing us to develop a software tool that we called Auto-Predict (now known as Navigator). This completely eliminates the guesswork as the software automatically finds an oven recipe that will process the board in spec.
"Our next group of products is used once you’re ready to start production," said Kazmierowicz. "How do you know boards or parts were processed correctly? We monitor the temperature and speed along the oven conveyor during production. We can say, ‘Based on these inputs, your output is still within the range that is going to work, and your boards are being processed in spec.’ Or we can identify problems, such as if zone eight and nine changed significantly. Our setup tools help the customer find the correct oven recipe and our automatic systems continuously monitor production. Simply trusting that no changes to the oven have occurred since you last attached thermocouples to your board or silicon—however long ago—is just not enough. Now, more customers want our monitoring capabilities."
Less Downtime
Allen summarized downtime as follows. "We all know that one of the worst things to hear in a factory is ‘downtime’ because this has a direct link to lost money/profits, delay in delivery, unhappy managers, owners, and most importantly, customers. With so much automation, there still tends to be the possibility of downtime in the reflow process. A reflow-related defect found by an AOI machine requires immediate action, for example. One of the investigative steps may be to run a profile to determine if there was any change in the reflow oven to determine if the fault is due to a process change, human intervention, or something else entirely."
"This downtime may be significantly reduced if a reflow process inspection (RPI) system is in use," explained Allen. "This RPI system will continuously monitor the conditions at the product level, provide the customer with data for each reflowed PCB, and notify the customer if a change is taking place and to what degree. If the current conditions are changing to a point where product entering the oven would not be in spec, a notification will take place and be automatically documented, and defective assemblies may be avoided. If there’s a defect found at AOI, you can rule out the oven.
Allen further detailed, "Planning for changeover downtime plays a role in optimization. With the knowledge of what products will be run on a given day, shift, oven, and their related profiles, the software can assist with the optimized plan to limit this changeover time in the reflow oven. An example is starting with SnPb assemblies and/or lower temperature profiles and working up to higher temperatures rather than the reverse, which takes time for oven cool down."
To read the full article, which appeared in the June 2019 issue of SMT007 Magazine, click here.
Suggested Items
Driving Innovation: Direct Imaging vs. Conventional Exposure
07/01/2025 | Simon Khesin -- Column: Driving InnovationMy first camera used Kodak film. I even experimented with developing photos in the bathroom, though I usually dropped the film off at a Kodak center and received the prints two weeks later, only to discover that some images were out of focus or poorly framed. Today, every smartphone contains a high-quality camera capable of producing stunning images instantly.
Hands-On Demos Now Available for Apollo Seiko’s EF and AF Selective Soldering Lines
06/30/2025 | Apollo SeikoApollo Seiko, a leading innovator in soldering technology, is excited to spotlight its expanded lineup of EF and AF Series Selective Soldering Systems, now available for live demonstrations in its newly dedicated demo room.
Indium Corporation Expert to Present on Automotive and Industrial Solder Bonding Solutions at Global Electronics Association Workshop
06/26/2025 | IndiumIndium Corporation Principal Engineer, Advanced Materials, Andy Mackie, Ph.D., MSc, will deliver a technical presentation on innovative solder bonding solutions for automotive and industrial applications at the Global Electronics A
Fresh PCB Concepts: Assembly Challenges with Micro Components and Standard Solder Mask Practices
06/26/2025 | Team NCAB -- Column: Fresh PCB ConceptsMicro components have redefined what is possible in PCB design. With package sizes like 01005 and 0201 becoming more common in high-density layouts, designers are now expected to pack more performance into smaller spaces than ever before. While these advancements support miniaturization and functionality, they introduce new assembly challenges, particularly with traditional solder mask and legend application processes.
Knocking Down the Bone Pile: Tin Whisker Mitigation in Aerospace Applications, Part 3
06/25/2025 | Nash Bell -- Column: Knocking Down the Bone PileTin whiskers are slender, hair-like metallic growths that can develop on the surface of tin-plated electronic components. Typically measuring a few micrometers in diameter and growing several millimeters in length, they form through an electrochemical process influenced by environmental factors such as temperature variations, mechanical or compressive stress, and the aging of solder alloys.