-
- News
- Books
Featured Books
- pcb007 Magazine
Latest Issues
Current IssueThe Hole Truth: Via Integrity in an HDI World
From the drilled hole to registration across multiple sequential lamination cycles, to the quality of your copper plating, via reliability in an HDI world is becoming an ever-greater challenge. This month we look at “The Hole Truth,” from creating the “perfect” via to how you can assure via quality and reliability, the first time, every time.
In Pursuit of Perfection: Defect Reduction
For bare PCB board fabrication, defect reduction is a critical aspect of a company's bottom line profitability. In this issue, we examine how imaging, etching, and plating processes can provide information and insight into reducing defects and increasing yields.
Voices of the Industry
We take the pulse of the PCB industry by sharing insights from leading fabricators and suppliers in this month's issue. We've gathered their thoughts on the new U.S. administration, spending, the war in Ukraine, and their most pressing needs. It’s an eye-opening and enlightening look behind the curtain.
- Articles
- Columns
- Links
- Media kit
||| MENU - pcb007 Magazine
Vertical Conductive Structures, Part 2: VeCS and Micro-machining
July 10, 2019 | Joan Tourné, NextGIn Technology BVEstimated reading time: 4 minutes
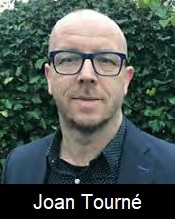
Editor's Note: Click here to read Part 1.
Micro-machining is used every day in circuit board manufacturing with both drill and routing bits. Micro-machining is a very broad term for techniques used to shape an object. I introduce this term because micro-machining, in combination with the fabrication and processing of objects in 2.5D and 3D is not commonly used in circuit board manufacturing. But vertical conductive structure (VeCS) technology will change that.
Today, the industry has available to it the infrastructure needed to shape circuits in a different way and to create new functions and applications, such as higher density connections between internal and external layers and tuned connections that minimize signal distortion. VeCS is a multi-depth slot element currently achieved with CNC machines (part of today’s infrastructure) using drill and router bits to create the shapes (Figure 1). The objective is to create a new structure that makes the vertical connections using the board real estate differently so that we do not comprise isolation.
CAF/electron migration are the primary constraints in reducing the distance between vertical connections (via hole, microvia, etc.). By using micro-machining, we can create structures that are less–or not at all–sensitive to these isolation defects. VeCS-1, as described in the first article of this series, is a slot going through the circuit from top to bottom. In this article, I will focus on VeCS-2 technology (blind slots) as more micro-machining techniques are required for VeCS-2 than VeCS-1.
Note that the examples in this article all focus on slots with the same depth. In a later article on VeCS, we will see multi-depth slots connecting signals, not only connecting the signal from the outside layers to the internal layer but from, for example, layer 3 to layer 10 creating an internal layer transition. Also, in future articles, we will address transparent layer transitions where more micro-machining techniques will come into play to define the different depths as well as the sequence of processing. It would be preferred to have machine codes defined that determined the depths and sequence of the processing. CAM systems need to accommodate the rules and process sequences to minimise the potential for error in engineering and fabrication.
Figure 1: The basic VeCS element shown from the bottom side using two traces and a power connection at the far end of the slot. Terms for the wide structures are cross route and bottom route.
The VeCS slot shown in Figure 2 is close to a 2.7 mm depth in a 3.0 mm product. The plating is split at the bottom of the deep slot creating two potentials. This particular slot is part of a test coupon, and therefore, has a connection on every layer. This would not be representative of a typical design.
Figure 2: Basic high aspect ratio VeCS-2 element.
If we use the VeCS for an internal layer transition (no connection at the top layer) we micro-machine the vertical trace away in the same process step as we do the cross route. Building on part one of this series where I introduced the VeCS slot, I will introduce some additional features under the topic of micromachining.
Power VeCS
Electronics design applications constantly need more power and current, which opposes the need to make the features smaller, increasing resistance. These opposing constraints still apply to VeCS. With Power-VeCS, the vertical copper trace is shaped so that the cross section is larger, giving it a lower conductivity. Figure 3 shows the use of a half round cylinder extending from the side wall of the slot on the top layers (adding this construct on every layer compromises the routing channel).
We create the lower resistance connection by a combination of the vertical trace shapes with a stackup where Layer 2 (green) and Layer 3 (red) are a power/ground layer. In this manner, we create a lower resistance connection while keeping the connection to all ground and power in the same position. This prevents the shifting of ground and power. And at the same time, we keep the CAF bridge in place.
Data Size
One difference between using micro-machining and the traditional PCB data sets can be the number of lines of machine-code/G-code required. For some designs, the amount of programming code can easily exceed the memory capacity of the current generation CNC machines. To reduce the number of lines of CNC code required, one could always write a specific machine code that defines a slot using a sequence of numbers for slot length and depth. Naturally, this makes the process more complex in that data files need to be cut up with correspondingly increased potential for error.
Micro-machining Experiences
Depth control is one of the challenges in setting up the VeCS-2 slots process. Dielectric tolerances are a critical parameter when setting the depth. Dielectric measurement across the panel needs to be performed to set the correct depth. The layer below the slot needs to have isolation thick enough to accommodate the tolerance of the Z-axis on the CNC machine. This tolerance needs to be in the region of ±0.02 mm. It should be noted also that the type of pressure foot as well as resetting the Z-axis counter through contact with the surface are important in achieving good depth tolerances. Later in this series, I will introduce layer detection. This technique prevents what would otherwise be a complex, time-consuming, and somewhat inaccurate depth-setting process. Similar techniques will also be used for back drilling and depth-control drilling.
To read the full article, which appeared in the June 2019 issue of PCB007 Magazine, click here.
Suggested Items
I-Connect007 Editor’s Choice: Five Must-Reads for the Week
07/11/2025 | Andy Shaughnessy, Design007 MagazineThis week, we have quite a variety of news items and articles for you. News continues to stream out of Washington, D.C., with tariffs rearing their controversial head again. Because these tariffs are targeted at overseas copper manufacturers, this news has a direct effect on our industry.I-Connect007 Editor’s Choice: Five Must-Reads for the Week
Digital Twin Concept in Copper Electroplating Process Performance
07/11/2025 | Aga Franczak, Robrecht Belis, Elsyca N.V.PCB manufacturing involves transforming a design into a physical board while meeting specific requirements. Understanding these design specifications is crucial, as they directly impact the PCB's fabrication process, performance, and yield rate. One key design specification is copper thieving—the addition of “dummy” pads across the surface that are plated along with the features designed on the outer layers. The purpose of the process is to provide a uniform distribution of copper across the outer layers to make the plating current density and plating in the holes more uniform.
Trump Copper Tariffs Spark Concern
07/10/2025 | I-Connect007 Editorial TeamPresident Donald Trump stated on July 8 that he plans to impose a 50% tariff on copper imports, sparking concern in a global industry whose output is critical to electric vehicles, military hardware, semiconductors, and a wide range of consumer goods. According to Yahoo Finance, copper futures climbed over 2% following tariff confirmation.
Happy’s Tech Talk #40: Factors in PTH Reliability—Hole Voids
07/09/2025 | Happy Holden -- Column: Happy’s Tech TalkWhen we consider via reliability, the major contributing factors are typically processing deviations. These can be subtle and not always visible. One particularly insightful column was by Mike Carano, “Causes of Plating Voids, Pre-electroless Copper,” where he outlined some of the possible causes of hole defects for both plated through-hole (PTH) and blind vias.
Trouble in Your Tank: Can You Drill the Perfect Hole?
07/07/2025 | Michael Carano -- Column: Trouble in Your TankIn the movie “Friday Night Lights,” the head football coach (played by Billy Bob Thornton) addresses his high school football team on a hot day in August in West Texas. He asks his players one question: “Can you be perfect?” That is an interesting question, in football and the printed circuit board fabrication world, where being perfect is somewhat elusive. When it comes to mechanical drilling and via formation, can you drill the perfect hole time after time?