-
- News
- Books
Featured Books
- smt007 Magazine
Latest Issues
Current IssueWhat's Your Sweet Spot?
Are you in a niche that’s growing or shrinking? Is it time to reassess and refocus? We spotlight companies thriving by redefining or reinforcing their niche. What are their insights?
Moving Forward With Confidence
In this issue, we focus on sales and quoting, workforce training, new IPC leadership in the U.S. and Canada, the effects of tariffs, CFX standards, and much more—all designed to provide perspective as you move through the cloud bank of today's shifting economic market.
Intelligent Test and Inspection
Are you ready to explore the cutting-edge advancements shaping the electronics manufacturing industry? The May 2025 issue of SMT007 Magazine is packed with insights, innovations, and expert perspectives that you won’t want to miss.
- Articles
- Columns
- Links
- Media kit
||| MENU - smt007 Magazine
Solder Mask Evolves into a Truly Additive Process
September 9, 2019 | John Fix, Taiyo America Inc.Estimated reading time: 3 minutes
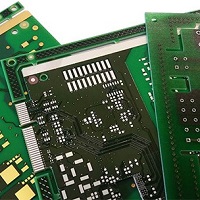
As I write this article, it is the eve of high school graduation for my oldest son, Tom. It’s easy to reflect on his life that spans just short of 18 years. As parents, we all remember the milestones of our child(ren): when they were born and their first words, steps, days of school, etc. His high school graduation means he now embarks on the specialized educational path of his choice. For my wife and I, we have fantastic memories and look forward to seeing what Tom’s future holds.
I started with Taiyo America 18 years ago. And yes, 18 years can be a lifetime for some (like Tom), or short for others, like my wife and me. It’s all just a perception of time. Of course, technology can change significantly in a short period of time as well, which is not a perception; it’s a reality that we see every day. Changing technology has a dramatic effect on how we live our lives. As a young parent, I thought it was incredible to have a video baby monitor. Now, the norm is to have an app to monitor your baby’s every move from your smartphone. In the electronics world, 18 years have delivered changes from flip phones to smartphones, 2G to 5G, and plated through-holes to blind vias. In the automotive world, Tesla didn’t even start development until 2004; now, we have self-driving vehicles.
However, the 5G era is creating quite a bit of work for many PCB engineers as the materials required to keep up with the speed, frequency, and latency requirements need to be defined and qualified. Solder mask, for example, now becomes a truly additive process. There are several solder mask properties to investigate, including digital solder mask technology, process step removal, environmental extremes, heat management, crack reduction, and via filling, just to name a few. In this article, I will begin to explore the "hows" and the "whys" involved in making solder mask a strictly additive process.
Going Digital
One of the most important ones was the property function of imaging the material. PCBs have much tighter space requirements as devices get smaller and more processing is required that pushes PCB manufacturers to implement some form of digital printing into their process. Taiyo has spent several years in developing not only laser direct imaging (LDI) solder mask for the very popular Orbotech Paragon machine, but we have also designed direct imaging (DI) solder mask for various other DI equipment options that are now available.
These LDI/DI solder masks offer excellent advantages over traditional liquid photo-imageable (LPI) solder mask processes with regards to registration, tight tolerances, and fine dams. However, the true leap in digital solder mask technology is inkjet solder mask. For the past several years, Taiyo has worked with inkjet equipment manufacturers such as Orbotech and Notion Systems, just to name a couple, pushing this technology into the marketplace.
Inkjet solder mask allows you to enjoy the many advantages of LDI/DI, such as registration, no artwork generation or the waste/cost associated with it, and the capability to do fine features. You also gain the benefit of not leaving solder mask in the hole or on the pad because inkjet solder mask will never leave residue on pads or in the plated through-holes. This new solder mask application method truly becomes an additive process.
Process Optimization
In becoming an additive process, solder mask can now remove multiple steps in the current process. No more waste development solution that must be deposed of and no more artwork generations waste disposition. Tack drying and the associated solvent that is dissipated into the environment is gone. Thus, inkjet solder mask not only saves you money in processing cost, but you are making the environment greener. When would you have ever thought you would have heard that statement before—a PCB process that is environmentally friendly? Although the cost savings will vary from PCB manufacturer to manufacturer due to labor cost, markets served, board technology, etc., it is obvious there is money to be saved and opportunities to be taken.
To read the full article, which appeared in the August 2019 issue of SMT007 Magazine, click here.
Suggested Items
Driving Innovation: Direct Imaging vs. Conventional Exposure
07/01/2025 | Simon Khesin -- Column: Driving InnovationMy first camera used Kodak film. I even experimented with developing photos in the bathroom, though I usually dropped the film off at a Kodak center and received the prints two weeks later, only to discover that some images were out of focus or poorly framed. Today, every smartphone contains a high-quality camera capable of producing stunning images instantly.
Hands-On Demos Now Available for Apollo Seiko’s EF and AF Selective Soldering Lines
06/30/2025 | Apollo SeikoApollo Seiko, a leading innovator in soldering technology, is excited to spotlight its expanded lineup of EF and AF Series Selective Soldering Systems, now available for live demonstrations in its newly dedicated demo room.
Indium Corporation Expert to Present on Automotive and Industrial Solder Bonding Solutions at Global Electronics Association Workshop
06/26/2025 | IndiumIndium Corporation Principal Engineer, Advanced Materials, Andy Mackie, Ph.D., MSc, will deliver a technical presentation on innovative solder bonding solutions for automotive and industrial applications at the Global Electronics A
Fresh PCB Concepts: Assembly Challenges with Micro Components and Standard Solder Mask Practices
06/26/2025 | Team NCAB -- Column: Fresh PCB ConceptsMicro components have redefined what is possible in PCB design. With package sizes like 01005 and 0201 becoming more common in high-density layouts, designers are now expected to pack more performance into smaller spaces than ever before. While these advancements support miniaturization and functionality, they introduce new assembly challenges, particularly with traditional solder mask and legend application processes.
Knocking Down the Bone Pile: Tin Whisker Mitigation in Aerospace Applications, Part 3
06/25/2025 | Nash Bell -- Column: Knocking Down the Bone PileTin whiskers are slender, hair-like metallic growths that can develop on the surface of tin-plated electronic components. Typically measuring a few micrometers in diameter and growing several millimeters in length, they form through an electrochemical process influenced by environmental factors such as temperature variations, mechanical or compressive stress, and the aging of solder alloys.