-
- News
- Books
Featured Books
- pcb007 Magazine
Latest Issues
Current IssueThe Hole Truth: Via Integrity in an HDI World
From the drilled hole to registration across multiple sequential lamination cycles, to the quality of your copper plating, via reliability in an HDI world is becoming an ever-greater challenge. This month we look at “The Hole Truth,” from creating the “perfect” via to how you can assure via quality and reliability, the first time, every time.
In Pursuit of Perfection: Defect Reduction
For bare PCB board fabrication, defect reduction is a critical aspect of a company's bottom line profitability. In this issue, we examine how imaging, etching, and plating processes can provide information and insight into reducing defects and increasing yields.
Voices of the Industry
We take the pulse of the PCB industry by sharing insights from leading fabricators and suppliers in this month's issue. We've gathered their thoughts on the new U.S. administration, spending, the war in Ukraine, and their most pressing needs. It’s an eye-opening and enlightening look behind the curtain.
- Articles
- Columns
- Links
- Media kit
||| MENU - pcb007 Magazine
Streamlining Inspection and Verification
January 23, 2020 | Barry Matties, I-Connect007Estimated reading time: 4 minutes
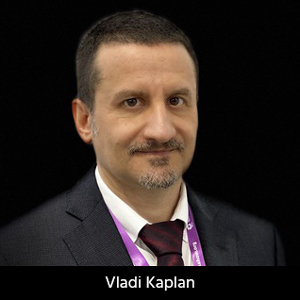
Barry Matties speaks with Vladi Kaplan, VP of marketing for CIMS, about the company’s newest verification station, the benefits operators will see from its colorized real-time video, and how it makes verification much faster and much more efficient for companies pushing 100% inspection.
Barry Matties: Congratulations on some new equipment you’re showing at the International Electronics Circuit Exhibition in Shenzhen, China. First, can you give us a quick overview of CIMS?
Vladi Kaplan: We are an AOI equipment manufacturer and used to be known as Camtek. A little over two years ago, we were spun off of Camtek. For two years already, we have been a completely independent company, but the basis of our technology and the types of equipment that we are selling are the same. Of course, we have improved quite a lot, came up with a lot of new models, and are doing well.
Matties: And you’re introducing some new technology at this show.
Kaplan: Everything that we are showing this time is all about drill inspection. We have families of models for laser via inspection, which is a very hot topic right now, mainly driven by new demands from end-users for 100% inspection of laser vias. On top of that, there are various types of laser vias requiring inspection. Most recently, we see a new process of a direct laser via that drills all the way through the panels. It is similar to a mechanical drill, but with a laser, so our customers are looking for an inspection solution for that as well. Therefore, we have launched a dedicated model for the inspection of these type of products.
For this particular solution, we are using LED-based illumination called ViaLight™ that is built inside the table. It works in combination with our traditional illumination called Microlight™ illuminating the PCB surface from the top. With this dual illumination setup, we are able to see the entire full image of the drill, both from the inside and outside.
Matties: There must be a big need for it for you to invest in producing a machine like this.
Kaplan: We believe that we are right at the beginning of that kind of demand. We anticipate growth, and there’s a lot of interest, so we developed this solution based on emerging market demand. Since we have a reputation of a company that can develop a complex AOI solution quickly, we have customers coming to us and asking us to meet that specific demand. We have big hopes for this system.
Matties: More and more HDI work is taking place. Is that what you see as driving the anticipation for this?
Kaplan: Yes. As far as inspection goes, as I mentioned before, laser via inspection is a big part of it. Years ago, it used to be sampling purely for some calibration purposes. Right now, companies are pushing 100% inspection, which is why we focus on that, so there is a big, new inspection market for us out there.
Matties: The market has been down in Asia for a bit over the last few months. What do you see now?
Kaplan: We see a lot of optimism. Based on the attendance of these shows, we don’t see a downturn but the opposite. People are expecting a ramp up, and we feel like the market is picking up.
Matties: There’s a lot of talk about 5G. Is it a driving factor based on the conversations you’re having?
Kaplan: It’s a big component of it, and there’s a lot of anticipation. China is moving ahead of the rest of the world in 5G. There is a lot of government encouragement and investment in this area, so it’s going to help all of us.
Matties: Absolutely. One of the other pieces of equipment you have is for inspection, and another is a verification system.
Kaplan: This is a new type of verification system called VVR, which stands for virtual verification and repair. The idea is to make verification more efficient than it used to be. This system s a combination of virtual and physical verification. By virtual verification, I mean grabbing defects’ images from the AOI machine and feeding them to our verification station. The first step is to go through those images to quickly filter out obvious false calls. The defects’ pictures that VVR operator sees are post-processed grey-level images from AOI, but you can’t tell that they are. Those images look just like a video with very natural color. We can achieve that natural look by using our unique post-processing technology that runs on every image grabbed by AOI. This way, VVR operators can see all the defects in a matrix, and in 90% of cases, can easily tell which are false calls and which are true defects.
The idea is to give an operator the opportunity to look at all of those images at once. They can set up as many as they want on one screen and choose those that they want to have a closer look at. For example, if they see a potential defect, such as something that could be either dust or a pinhole, they simply click to move the live video to that area. Then, they make a final judgment on whether it’s a defect or not. This sequence makes verification much faster and more efficient.
To read this entire interview, which appeared in the January 2020 issue of PCB007 Magazine, click here.
Suggested Items
Microchip Expands Space-Qualified FPGA Portfolio with New RT PolarFire® Device Qualifications and SoC Availability
07/10/2025 | MicrochipContinuing to support the evolving needs of space system developers, Microchip Technology has announced two new milestones for its Radiation-Tolerant (RT) PolarFire® technology: MIL-STD-883 Class B and QML Class Q qualification of the RT PolarFire RTPF500ZT FPGA and availability of engineering samples for the RT PolarFire System-on-Chip (SoC) FPGA.
Infineon Advances on 300-millimeter GaN Manufacturing Roadmap as Leading Integrated Device Manufacturer (IDM)
07/10/2025 | InfineonAs the demand for gallium nitride (GaN) semiconductors continues to grow, Infineon Technologies AG is poised to capitalize on this trend and solidify its position as a leading Integrated Device Manufacturer (IDM) in the GaN market.
Bell to Build X-Plane for Phase 2 of DARPA Speed and Runway Independent Technologies (SPRINT) X-Plane Program
07/09/2025 | Bell Textron Inc.Bell Textron Inc., a Textron Inc. company, has been down-selected for Phase 2 of Defense Advanced Research Projects Agency (DARPA) Speed and Runway Independent Technologies (SPRINT) X-Plane program with the objective to complete design, construction, ground testing and certification of an X-plane demonstrator.
2025 ASEAN IT Spending Growth Slows to 5.9% as AI-Powered IT Expansion Encounters Post-Boom Normalization
06/26/2025 | IDCAccording to the IDC Worldwide Black Book: Live Edition, IT spending across ASEAN is projected to grow by 5.9% in 2025 — down from a robust 15.0% in 2024.
DownStream Acquisition Fits Siemens’ ‘Left-Shift’ Model
06/26/2025 | Andy Shaughnessy, I-Connect007I recently spoke to DownStream Technologies founder Joe Clark about the company’s acquisition by Siemens. We were later joined by A.J. Incorvaia, Siemens’ senior VP of electronic board systems. Joe discussed how he, Rick Almeida, and Ken Tepper launched the company in the months after 9/11 and how the acquisition came about. A.J. provides some background on the acquisition and explains why the companies’ tools are complementary.