Documenting Your Flex Circuit Design
September 16, 2020 | Tony Plemel, Flexible Circuit TechnologiesEstimated reading time: 1 minute
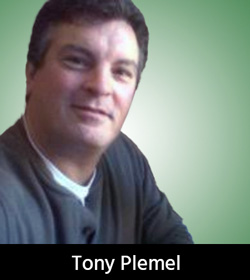
As a flex circuit applications engineer, when I receive an RFQ, the first thing I do is look at the customer’s data and review their manufacturing notes. Quite often, I find notes that supersede IPC specifications in manufacturing documents, as customers often believe these added notes and associated specifications will make the circuit more robust. However, these non-standard IPC manufacturing specifications/notes can wreak havoc on the manufacturing process and can actually lead to a less robust circuit.
For example, a customer will sometimes specify additional copper plating, believing it will result in a more reliable circuit. In reality, that type of requirement can make the circuit less reliable, more difficult to manufacture, and more expensive. When manufacturing yields go down, the price goes up!
In taking a deeper dive into manufacturing notes and the potential issues that they can create, let’s use a three-layer multilayer flexible circuit as an example. The first note on a manufacturing print is usually “Manufacture to IPC6013, Class 2, Type 3.” This note should always be included; I cannot stress that enough!
Unfortunately, in the continued review of the documentation, I often find one or more additional conflicting notes further down in the manufacturing notes that overrule IPC6013 specifications.
Copper Plating
One example would be “Minimum copper plating shall be 0.0015”.” This note supersedes the IPC-6013 specification in Table 1.
Table 1: IPC-6013 copper plating requirements.
PCB designers who are not well-versed in flex circuit manufacturing may not know that exceeding IPC-6013 of 984 µin (0.000984”) can cause the circuit to be less reliable and possibly cause problems later in the manufacturing process. Having a specified requirement this large (0.000516” thicker) will require the plating line at the factory to plate more than 0.0015” to ensure the minimum plating is 0.0015” thick.
To read this entire article, which appeared in the September 2020 issue of Design007 Magazine, click here.
Suggested Items
I-Connect007 Editor’s Choice: Five Must-Reads for the Week
07/18/2025 | Nolan Johnson, I-Connect007It may be the middle of the summer, but the news doesn’t quit, and there’s plenty to talk about this week, whether you’re talking technical or on a global scale. When I have to choose six items instead of my regular five, you know it’s good. I start by highlighting my interview with Martyn Gaudion on his latest book, share some concerning tariff news, follow that up with some promising (and not-so-promising) investments, and feature a paper from last January’s inaugural Pan-European Design Conference.
Elephantech Launches World’s Smallest-Class Copper Nanofiller
07/17/2025 | ElephantechJapanese deep-tech startup Elephantech has launched its cutting-edge 15 nm class copper nanofiller – the smallest class available globally. This breakthrough makes Elephantech one of the first companies in the world to provide such advanced material for commercial use.
Copper Price Surge Raises Alarms for Electronics
07/15/2025 | Global Electronics Association Advocacy and Government Relations TeamThe copper market is experiencing major turbulence in the wake of U.S. President Donald Trump’s announcement of a 50% tariff on imported copper effective Aug. 1. Recent news reports, including from the New York Times, sent U.S. copper futures soaring to record highs, climbing nearly 13% in a single day as manufacturers braced for supply shocks and surging costs.
I-Connect007 Editor’s Choice: Five Must-Reads for the Week
07/11/2025 | Andy Shaughnessy, Design007 MagazineThis week, we have quite a variety of news items and articles for you. News continues to stream out of Washington, D.C., with tariffs rearing their controversial head again. Because these tariffs are targeted at overseas copper manufacturers, this news has a direct effect on our industry.I-Connect007 Editor’s Choice: Five Must-Reads for the Week
Digital Twin Concept in Copper Electroplating Process Performance
07/11/2025 | Aga Franczak, Robrecht Belis, Elsyca N.V.PCB manufacturing involves transforming a design into a physical board while meeting specific requirements. Understanding these design specifications is crucial, as they directly impact the PCB's fabrication process, performance, and yield rate. One key design specification is copper thieving—the addition of “dummy” pads across the surface that are plated along with the features designed on the outer layers. The purpose of the process is to provide a uniform distribution of copper across the outer layers to make the plating current density and plating in the holes more uniform.