-
- News
- Books
Featured Books
- smt007 Magazine
Latest Issues
Current IssueIntelligent Test and Inspection
Are you ready to explore the cutting-edge advancements shaping the electronics manufacturing industry? The May 2025 issue of SMT007 Magazine is packed with insights, innovations, and expert perspectives that you won’t want to miss.
Do You Have X-ray Vision?
Has X-ray’s time finally come in electronics manufacturing? Join us in this issue of SMT007 Magazine, where we answer this question and others to bring more efficiency to your bottom line.
IPC APEX EXPO 2025: A Preview
It’s that time again. If you’re going to Anaheim for IPC APEX EXPO 2025, we’ll see you there. In the meantime, consider this issue of SMT007 Magazine to be your golden ticket to planning the show.
- Articles
- Columns
Search Console
- Links
- Media kit
||| MENU - smt007 Magazine
Real Time with...SMTAI 2020: MacDermid Alpha’s Single-Step Metalization Paper
September 30, 2020 | Real Time with...SMTAIEstimated reading time: 5 minutes
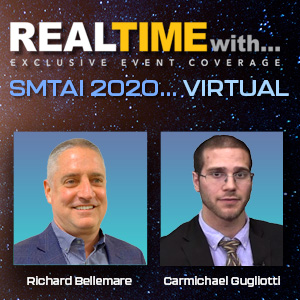
Nolan Johnson talks with MacDermid Alpha Electronics Solutions about a new process for filling through-holes with copper in a single step. Carmichael Gugliotti, the primary author and an applications specialist, and Richard Bellemare, director of electrolytic metalization, address why this new process matters and what’s in Gugliotti’s technical paper presentation for SMTAI.
Nolan Johnson: Nolan Johnson here for virtual Real Time with… SMTAI, and today. I’m talking with MacDermid Alpha’s Carmichael Gugliotti and Rich Bellemare. Carmichael is a metallization application manager, and Rich is the director of electrolytic metallization. Our topic is the paper that you’ve submitted to SMTA International, the technical conference, titled “Single-Step Metallization Process for Filling Through-Holes With Copper.” Let’s start with why that matters.
Carmichael Gugliotti: Thanks for having me, Nolan. There are two main things that we use the single-step through-hole fill process for. One of them is for thermal management, and then the other big one is for any layer. It makes a much more solid base to build up layers after that initial inner layer is created on the circuit board.
Johnson: What sorts of fabrication applications lend themselves to this? Where would this be a concern for the fabricator?
Rich Bellemare: Primarily, where this would fit in is the couple of segments that Carmichael had mentioned. For the core layer of through-hole filling, this is targeting the IC substrate market, where you’re looking to have very stable, flat surfaces in that core layer upon which to build further layers. This is critical to densify circuitry. The other one is in the thermal management, where you’re targeting some of the thicker types of panels—such as the LED market, where you’re trying to draw the way from actively heat-generating components—forestalling their life and making the whole system more reliable.
Johnson: Is it a fair representation for me to say that really you’re looking at making a planar a surface as possible?
Gugliotti: Yes, that’s a big part of it. The single-step process is one of the best we have now for creating a flat surface across the entire circuit board, rather than just having these holes that have these big dimples that we’re really struggling to build on.
Bellemare: There’s a lot of disadvantages nowadays with the way through-holes are filled. A lot of them were done with DC plating or plugging with paste and planarizing. All these things add a lot of extra steps, and a lot of extra copper needs to be dealt with later on in the fabrication process.
Johnson: Walk me through the research. You got started on this specifically looking for a single-step process, or was this just a result of the work you were doing?
Gugliotti: Yes, we started off initially with a DC process, which really worked well for thin boards. But as boards got more difficult, they got more holes on them, or they got thicker. It really was kind of limited. Either it took an excessive amount of time, or the capability just wasn’t there. We got lots of cavities.
We then moved into a two-step process and were working with that for a little while, but then you have a lot of equipment. You have a lot of taking the panels in and out of tanks, moving them around. This process kind of combines the best of both worlds. It has a pretty wide availability, can use a lot of different through-hole sizes and panel thicknesses, and can all be done in this single-step process.
Johnson: What was key in getting from a two-step process to the single-step process?
Gugliotti: The big addition is we have a novel leveler that we added into our single-step process, and this allows us to keep that bridge capability we had initially, fill those vias, and make that flat surface on the profile of the hole.
Johnson: This is an application obviously that has a place in the market. Who’s your target customer for this? And is this available for production type customers now?
Bellemare: Yes, it is available as a production process. It’s a process that’s just being released into the marketplace. Again, our target initially is more for the IC substrate to simplify the manufacturing process and give the process the biggest capability possible. We’re going with the single-step through-hole filling process.
Johnson: In this conversation, we’ve talked both about board and about IC substrate. Help me connect the dots there for you. Is this something that fits both in on the IC side and the PCB side?
Bellemare: This is the IC substrate, as far as the organic substrate that you’re attaching the dies to. The IC substrate dies, you’re attaching those to the organic substrate, which is what we’re calling the IC substrate. What’s important there is densification of circuitry, as you’re trying to keep these organic substrates as thin as possible. It all goes into keeping as little surface coppers possible when you plate and being able to fill these holes without the need for planarization. Because as all these dimensions become tighter and tighter, you can’t use mechanical planarization anymore because of registration issues and feature sizes of an IC substrate.
Johnson: Great. Thanks, gentlemen. That has certainly been enlightening. I look forward to catching your presentation, Carmichael, at the SMTAI technical presentations. It’s one I’m excited to find out more about, as will the rest of our readers. Thanks for taking the time to talk with me.
Gugliotti: Thank you.
Bellemare: It’s our pleasure.
Johnson: Nolan Johnson here for Real Time with… SMTAI.
View more show-related content at Real Time with… SMTAI 2020 virtual.
I-Connect007 continues to deliver original reporting and coverage of the electronics design, electronics manufacturing, and contract manufacturing industries, including up-to-date information from the companies, associations, and supply chains globally. Find the latest news and information at I-Connect007.com.
Suggested Items
Elephantech: For a Greener Tomorrow
04/16/2025 | Marcy LaRont, PCB007 MagazineNobuhiko Okamoto is the global sales and marketing manager for Elephantech Inc., a Japanese startup with a vision to make electronics more sustainable. The company is developing a metal inkjet technology that can print directly on the substrate and then give it a copper thickness by plating. In this interview, he discusses this novel technology's environmental advantages, as well as its potential benefits for the PCB manufacturing and semiconductor packaging segments.
Trouble in Your Tank: Organic Addition Agents in Electrolytic Copper Plating
04/15/2025 | Michael Carano -- Column: Trouble in Your TankThere are numerous factors at play in the science of electroplating or, as most often called, electrolytic plating. One critical element is the use of organic addition agents and their role in copper plating. The function and use of these chemical compounds will be explored in more detail.
IDTechEx Highlights Recyclable Materials for PCBs
04/10/2025 | IDTechExConventional printed circuit board (PCB) manufacturing is wasteful, harmful to the environment and energy intensive. This can be mitigated by the implementation of new recyclable materials and technologies, which have the potential to revolutionize electronics manufacturing.
Connect the Dots: Stop Killing Your Yield—The Hidden Cost of Design Oversights
04/03/2025 | Matt Stevenson -- Column: Connect the DotsI’ve been in this industry long enough to recognize red flags in PCB designs. When designers send over PCBs that look great on the computer screen but have hidden flaws, it can lead to manufacturing problems. I have seen this happen too often: manufacturing delays, yield losses, and designers asking, “Why didn’t anyone tell me sooner?” Here’s the thing: Minor design improvements can greatly impact manufacturing yield, and design oversights can lead to expensive bottlenecks. Here’s how to find the hidden flaws in a design and avoid disaster.
Real Time with... IPC APEX EXPO 2025: Tariffs and Supply Chains in U.S. Electronics Manufacturing
04/01/2025 | Real Time with...IPC APEX EXPOChris Mitchell, VP of Global Government Relations for IPC, discusses IPC's concerns about tariffs on copper and their impact on U.S. electronics manufacturing. He emphasizes the complexity of supply chains and the need for policymakers to understand their effects.