-
-
News
News Highlights
- Books
Featured Books
- design007 Magazine
Latest Issues
Current IssueAll About That Route
Most designers favor manual routing, but today's interactive autorouters may be changing designers' minds by allowing users more direct control. In this issue, our expert contributors discuss a variety of manual and autorouting strategies.
Creating the Ideal Data Package
Why is it so difficult to create the ideal data package? Many of these simple errors can be alleviated by paying attention to detail—and knowing what issues to look out for. So, this month, our experts weigh in on the best practices for creating the ideal design data package for your design.
Designing Through the Noise
Our experts discuss the constantly evolving world of RF design, including the many tradeoffs, material considerations, and design tips and techniques that designers and design engineers need to know to succeed in this high-frequency realm.
- Articles
- Columns
- Links
- Media kit
||| MENU - design007 Magazine
Seven Tips for Your Next Stackup Design
February 1, 2021 | Eric Bogatin, University of Colorado, BoulderEstimated reading time: 4 minutes
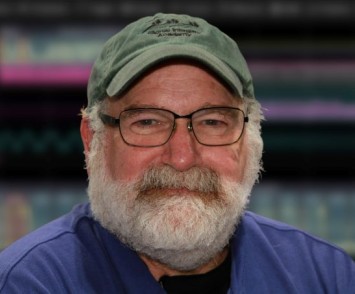
If interconnects were transparent, the stackup in your board would just be about how many layers you would need to route all the connections between components. In fact, some test boards that are strictly testing continuity and isolation do exactly this. Each layer is a dense packing of narrow signal traces connecting an array of pogo pin pads on the top side to an array of connectors to an ATE on the bottom side.
But rarely do we have the luxury of designing a board just for connectivity. When interconnects are not transparent, we must engineer them to reduce the noise they can generate. This is where design for signal integrity, power integrity and EMC—collectively high-speed digital engineering—are so important.
Seven Tips for Stackup
1. An important element in reducing the noise contributions from the interconnects comes from the stackup of the board and the layer assignments. The very first step is to engineer all signal layers with at least one adjacent plane as the return path. This will reduce the crosstalk between the signal-return paths: the microstrip traces on the outer layers and stripline traces on the inner layers.
2. The striplines can be either one signal layer between two planes or two signal layers between two planes. With two signal layers between two planes, there is the danger of excessive crosstalk if signals on adjacent layers are routed broadside to each other.
3. To avoid this problem, it is best to route the adjacent signal layers in dual stripline stackups orthogonally. One signal layer is routed in the x-direction, the other in the y-direction.
4. When interconnects must distribute 10 A of current or less, traces as wide as 200 mils can carry the 10 A of current in 1 oz copper with an acceptable temperature rise. But, with larger currents, like 20 A or more, it may be necessary to use wide planes to distribute the current from the power generators to the power consumers on a board. This is when some of the planes should be allocated as dedicated power planes.
The challenge is balancing the requirements of power distribution with the requirements for reduced crosstalk from signals changing return planes.
In principle, a signal line will see exactly the same characteristic impedance if the return plane is at ground potential or 12 V potential or anywhere in between. The problem with using a different voltage plane than ground to carry return current is when the signals change layers.
5. When a signal trace switches layers, we use a via to carry the signal current. If the return plane also changes, we will achieve the lowest crosstalk between all the signals switching layers when we also provide a via to carry the return current from the starting plane(s) to the final plane(s). This is a lowimpedance via shorting between the two different return planes. This is only possible if the return planes are the same voltage. If they are at different voltages, we can’t add a shorting via between them. This is a strong motivation to only use ground planes as the return planes for signals.
6. At best, if the two planes are a different voltage, we can add shorting vias between the two planes with a DC blocking capacitor between them. The loop inductance through a DC blocking capacitor can be as much as 5x higher impedance of a direct shorting via. It is a poor approximation to a shorting via, but the best we can do.
7. When signals change return planes and the planes are at different voltages, we run the risk of launching high bandwidth return currents into the cavity formed by the two planes. This is a source of long-range crosstalk and potentially a source of radiated emissions noise. One solution to reduce the noise in the power-ground cavity is by using very thin dielectric in these layers. This suggests that when power planes are used, they should be paired with closely spaced adjacent ground planes.
Once the order of the signal layers and planes is set, the dimensions can be calculated based on the line width of signal traces, the dielectric constant of the laminates used, and the target single-ended or differential impedance. This is where a 2D field solver comes in handy to define the cross section of microstrip traces, single layer stripline and dual layer strip line traces.
If you don’t follow these tips, it does not mean your board will not work. Unfortunately, there is no way of knowing if your stackup design will work or not unless you do a detailed analysis based on the driver models and 3D electromagnetic analysis of all the worst-case signal and power paths. Implementing these tips is about risk reduction.
They are part of a balanced diet of best stackup design practices, best signal routing design practices, and best power distribution design practices. And like all design guidelines, buyer beware. Always consider the best design practices, but also always do your own analysis.
This article appeared in the January 2021 issue of Design007 Magazine.
Suggested Items
The Evolution of Picosecond Laser Drilling
06/19/2025 | Marcy LaRont, PCB007 MagazineIs it hard to imagine a single laser pulse reduced not only from nanoseconds to picoseconds in its pulse duration, but even to femtoseconds? Well, buckle up because it seems we are there. In this interview, Dr. Stefan Rung, technical director of laser machines at Schmoll Maschinen GmbH, traces the technology trajectory of the laser drill from the CO2 laser to cutting-edge picosecond and hybrid laser drilling systems, highlighting the benefits and limitations of each method, and demonstrating how laser innovations are shaping the future of PCB fabrication.
Day 2: More Cutting-edge Insights at the EIPC Summer Conference
06/18/2025 | Pete Starkey, I-Connect007The European Institute for the PCB Community (EIPC) summer conference took place this year in Edinburgh, Scotland, June 3-4. This is the third of three articles on the conference. The other two cover Day 1’s sessions and the opening keynote speech. Below is a recap of the second day’s sessions.
Day 1: Cutting Edge Insights at the EIPC Summer Conference
06/17/2025 | Pete Starkey, I-Connect007The European Institute for the PCB Community (EIPC) Summer Conference took place this year in Edinburgh, Scotland, June 3-4. This is the second of three articles on the conference. The other two cover the keynote speeches and Day 2 of the technical conference. Below is a recap of the first day’s sessions.
Preventing Surface Prep Defects and Ensuring Reliability
06/10/2025 | Marcy LaRont, PCB007 MagazineIn printed circuit board (PCB) fabrication, surface preparation is a critical process that ensures strong adhesion, reliable plating, and long-term product performance. Without proper surface treatment, manufacturers may encounter defects such as delamination, poor solder mask adhesion, and plating failures. This article examines key surface preparation techniques, common defects resulting from improper processes, and real-world case studies that illustrate best practices.
RF PCB Design Tips and Tricks
05/08/2025 | Cherie Litson, EPTAC MIT CID/CID+There are many great books, videos, and information online about designing PCBs for RF circuits. A few of my favorite RF sources are Hans Rosenberg, Stephen Chavez, and Rick Hartley, but there are many more. These PCB design engineers have a very good perspective on what it takes to take an RF design from schematic concept to PCB layout.