-
- News
- Books
Featured Books
- pcb007 Magazine
Latest Issues
Current IssueThe Hole Truth: Via Integrity in an HDI World
From the drilled hole to registration across multiple sequential lamination cycles, to the quality of your copper plating, via reliability in an HDI world is becoming an ever-greater challenge. This month we look at “The Hole Truth,” from creating the “perfect” via to how you can assure via quality and reliability, the first time, every time.
In Pursuit of Perfection: Defect Reduction
For bare PCB board fabrication, defect reduction is a critical aspect of a company's bottom line profitability. In this issue, we examine how imaging, etching, and plating processes can provide information and insight into reducing defects and increasing yields.
Voices of the Industry
We take the pulse of the PCB industry by sharing insights from leading fabricators and suppliers in this month's issue. We've gathered their thoughts on the new U.S. administration, spending, the war in Ukraine, and their most pressing needs. It’s an eye-opening and enlightening look behind the curtain.
- Articles
- Columns
- Links
- Media kit
||| MENU - pcb007 Magazine
Driving Down Cost with Process Engineering
April 20, 2021 | I-Connect007 Editorial TeamEstimated reading time: 3 minutes
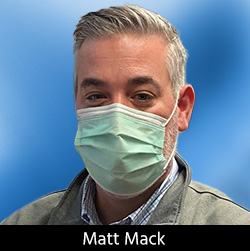
Nolan Johnson and Barry Matties speak with Matt Mack, a process engineer at ICM Controls. Matt shares how he’s driving down cost through continuous improvement. He also discusses planning for the future with automation and AI. Matt started with ICM Controls in 2019. Prior, he worked at Whelen Engineering (now GreenSource Fabrication) for about five years. His career in the PCB industry began at Sanmina.
Nolan Johnson: We’re interested in learning about your approach to process engineering. What’s your thinking for identifying processes that are in need of improvement?
Matt Mack: I start with our price per panels and the costs that are associated with it. I start to think, how can we make the process smoother, more efficient, where I don’t need to have as much human interaction with chemicals? That all starts with gathering data with chemical data. I’ll do titrations, for example. I’ll pick one line at a time that I will not have any dosing on, and I’ll calculate the square footage of panels through X amount of time, how much it dropped in concentration, and I’ll adjust dosing based on panel count. Then you have to optimize speed.
You can also do line speed, increasing or decreasing to optimize quality. I always strive for the 1.33 Cpk for the parts. It’s not always possible, but we come pretty close. It took about six months to really get dosing right. Right now, we do chemical analysis about twice a week. That’s much lower than recommended, but the data is not driving us to analyze it more. I asked our software guy to develop a chemical database that allows me to input the chemical data and track Cpk, track trends up and down, and in-spec/out-of-spec; if any of those rules are violated, it notifies me through an email.
Some of those are deemed critical, some are not. If any of it is deemed critical, we’ll trigger the production’s halt. If it’s not critical, we might be able to do it on the fly. For instance, let’s look at the copper concentration in a microetch. I might empty the line out before its formal dump, but it’s not going to impact quality on the product. Those are some of the rules that I observe. Any time you see a trend of five points decreasing, it could be a dosing issue, so I would jump right on the dosing, and verify it’s dosing what I’ve asked it to dose; second, maybe the chemical ran out and there’s an airlock. I get a lot of those emails where it’ll show you process control.
Matties: When you stand back as a process engineer and take that 30,000-foot view of a process, what do you want to improve to optimize it? What’s your process for doing that?
Mack: The first thing I monitor is speed. We track panels through and panels out. I would always start with asking: What are some of the slower ones, and how do I increase throughput on that piece of production? If you’re going to have funnels where, let’s say, the score machine is not putting out as many panels as the plating line, I might need to buy either a faster score machine or an additional score machine to maximize output. As we’re ramping up here, there is some capex equipment that we’re looking to quote in order to increase production on the floor. Generally, speed is what I look at.
The second thing would be chemical usage. If it costs us X to run one panel, what is the impact of that one piece of chemical on the panel? I look at price per panel by operation, as well. Can I get away with dosing less? For instance, for the pre-treat line, they recommended running something like 20 milliliters a panel. I actually optimized it to only run at about 8 milliliters. It saved us $18,000 over the course of a year. A lot of what drives me to look at process either optimizes panel production or price. Regarding price, for example, every six months I’ll review price per panel to determine where we can improve and where we can’t.
To read this entire interview, which appeared in the April 2021 issue of PCB007 Magazine, click here.
Suggested Items
Copper Price Surge Raises Alarms for Electronics
07/15/2025 | Global Electronics Association Advocacy and Government Relations TeamThe copper market is experiencing major turbulence in the wake of U.S. President Donald Trump’s announcement of a 50% tariff on imported copper effective Aug. 1. Recent news reports, including from the New York Times, sent U.S. copper futures soaring to record highs, climbing nearly 13% in a single day as manufacturers braced for supply shocks and surging costs.
I-Connect007 Editor’s Choice: Five Must-Reads for the Week
07/11/2025 | Andy Shaughnessy, Design007 MagazineThis week, we have quite a variety of news items and articles for you. News continues to stream out of Washington, D.C., with tariffs rearing their controversial head again. Because these tariffs are targeted at overseas copper manufacturers, this news has a direct effect on our industry.I-Connect007 Editor’s Choice: Five Must-Reads for the Week
Digital Twin Concept in Copper Electroplating Process Performance
07/11/2025 | Aga Franczak, Robrecht Belis, Elsyca N.V.PCB manufacturing involves transforming a design into a physical board while meeting specific requirements. Understanding these design specifications is crucial, as they directly impact the PCB's fabrication process, performance, and yield rate. One key design specification is copper thieving—the addition of “dummy” pads across the surface that are plated along with the features designed on the outer layers. The purpose of the process is to provide a uniform distribution of copper across the outer layers to make the plating current density and plating in the holes more uniform.
Trump Copper Tariffs Spark Concern
07/10/2025 | I-Connect007 Editorial TeamPresident Donald Trump stated on July 8 that he plans to impose a 50% tariff on copper imports, sparking concern in a global industry whose output is critical to electric vehicles, military hardware, semiconductors, and a wide range of consumer goods. According to Yahoo Finance, copper futures climbed over 2% following tariff confirmation.
Happy’s Tech Talk #40: Factors in PTH Reliability—Hole Voids
07/09/2025 | Happy Holden -- Column: Happy’s Tech TalkWhen we consider via reliability, the major contributing factors are typically processing deviations. These can be subtle and not always visible. One particularly insightful column was by Mike Carano, “Causes of Plating Voids, Pre-electroless Copper,” where he outlined some of the possible causes of hole defects for both plated through-hole (PTH) and blind vias.