-
- News
- Books
Featured Books
- smt007 Magazine
Latest Issues
Current IssueWhat's Your Sweet Spot?
Are you in a niche that’s growing or shrinking? Is it time to reassess and refocus? We spotlight companies thriving by redefining or reinforcing their niche. What are their insights?
Moving Forward With Confidence
In this issue, we focus on sales and quoting, workforce training, new IPC leadership in the U.S. and Canada, the effects of tariffs, CFX standards, and much more—all designed to provide perspective as you move through the cloud bank of today's shifting economic market.
Intelligent Test and Inspection
Are you ready to explore the cutting-edge advancements shaping the electronics manufacturing industry? The May 2025 issue of SMT007 Magazine is packed with insights, innovations, and expert perspectives that you won’t want to miss.
- Articles
- Columns
- Links
- Media kit
||| MENU - smt007 Magazine
Excerpt—The Printed Circuit Assembler’s Guide to... SMT Inspection: Today, Tomorrow, and Beyond, Chapter 3
April 22, 2021 | Brent Fischthal, Koh Young AmericaEstimated reading time: 2 minutes
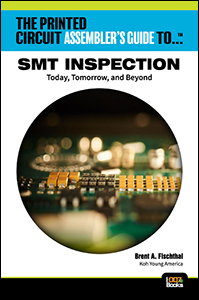
Chapter 3: The Data Dilemma
Data-driven analytics, using inspection data, can be used to overcome production challenges and to enable the smarter factory of today and of the future. Industry 4.0 and its associated benefits will doubtlessly advance the industry, so equipment suppliers need to continue to work diligently to accelerate M2M communication standards to aid the use of machine data to accelerate this trend.
To this end, the role of inspection becomes two-fold. The first is to ascertain if boards are good or bad at the point of inspection. The second is to provide data for the greater good of the process, the line and—ultimately—the factory.
Connectivity is the Foundation of the Smart Factory
Initiatives like the IPC Connected Factory Exchange (CFX) and IPC-Hermes-9852 underpin efforts within the industry to develop standards and help create a smart factory. These M2M communication standards, guided in part by Industry 4.0, are altering the manufacturing process by improving metrics such as first pass yield and throughput by applying autonomous process adjustments.
Far beyond an automatic line changeover, this two-way communication allows equipment to automatically adjust production parameters to increase board quality and lower costs by eliminating manual labor, rework, and scrap. As part of this mission, advanced process control with interconnected PCBA equipment will revolutionize process optimization and lay the foundation for the smart factory.
Measurement-based Inspection
Every electronics manufacturer—and most equipment suppliers, including automated inspection providers—is looking to optimize the assembly process. However, this is difficult, or even impossible, with the limitations of 2D imaging, the former industry standard. Not only is it difficult for 2D AOI systems to identify defects on curved and reflective solder joints, but 2D AOI systems simply do not generate data that is reliable enough to actually deliver consistent results.
Every aspect of the 2D inspection process relies on contrast—not quantitative measurement. As such, 2D users must either suggest the repair or scrapping of defective boards, which increases costs and eliminates the potential for process improvements.
Finding the Component Body
The introduction of 3D imaging to the inspection market solved many of these problems. By measuring components and solder joints, and then offering critical height information to the inspection algorithms, users could identify errors such as pad overhang and insufficient solder.
The 3D data is only valid when 3D technology is used for all component types to extract the exact body dimensions. Systems that use “blob detection,” which may be susceptible to external factors such as board warpage and component proximity, are less reliable. The combination of measurement and process data piles collected from its SPI and AOI systems, as well as from printers and mounters, allows delivery of advanced AI features with reliable “big data.”
To overcome this, true 3D technology must extract the component body data.
To download this free eBook, published by I-Connect007, click here.
To view the entire I-Connect007 eBook library, click here.
Suggested Items
SHENMAO Strengthens Semiconductor Capabilities with Acquisition of PMTC
07/10/2025 | SHENMAOSHENMAO America, Inc. has announced the acquisition of Profound Material Technology Co., Ltd. (PMTC), a premier Taiwan-based manufacturer of high-performance solder balls for semiconductor packaging.
KYZEN to Highlight Understencil and PCB Cleaners at SMTA Querétaro Expo and Tech Forum
07/09/2025 | KYZEN'KYZEN, the global leader in innovative environmentally responsible cleaning chemistries, will exhibit at the SMTA Querétaro Expo & Tech Forum, scheduled to take place Thursday, July 24, at Centro de Congresos y Teatro Metropolitano de Querétaro.
Driving Innovation: Direct Imaging vs. Conventional Exposure
07/01/2025 | Simon Khesin -- Column: Driving InnovationMy first camera used Kodak film. I even experimented with developing photos in the bathroom, though I usually dropped the film off at a Kodak center and received the prints two weeks later, only to discover that some images were out of focus or poorly framed. Today, every smartphone contains a high-quality camera capable of producing stunning images instantly.
Hands-On Demos Now Available for Apollo Seiko’s EF and AF Selective Soldering Lines
06/30/2025 | Apollo SeikoApollo Seiko, a leading innovator in soldering technology, is excited to spotlight its expanded lineup of EF and AF Series Selective Soldering Systems, now available for live demonstrations in its newly dedicated demo room.
Indium Corporation Expert to Present on Automotive and Industrial Solder Bonding Solutions at Global Electronics Association Workshop
06/26/2025 | IndiumIndium Corporation Principal Engineer, Advanced Materials, Andy Mackie, Ph.D., MSc, will deliver a technical presentation on innovative solder bonding solutions for automotive and industrial applications at the Global Electronics A