-
- News
- Books
Featured Books
- smt007 Magazine
Latest Issues
Current IssueIntelligent Test and Inspection
Are you ready to explore the cutting-edge advancements shaping the electronics manufacturing industry? The May 2025 issue of SMT007 Magazine is packed with insights, innovations, and expert perspectives that you won’t want to miss.
Do You Have X-ray Vision?
Has X-ray’s time finally come in electronics manufacturing? Join us in this issue of SMT007 Magazine, where we answer this question and others to bring more efficiency to your bottom line.
IPC APEX EXPO 2025: A Preview
It’s that time again. If you’re going to Anaheim for IPC APEX EXPO 2025, we’ll see you there. In the meantime, consider this issue of SMT007 Magazine to be your golden ticket to planning the show.
- Articles
- Columns
Search Console
- Links
- Media kit
||| MENU - smt007 Magazine
Solder Paste Printing and Optimizations for Interconnecting Back Contact Cells
July 26, 2022 | Narahari S Pujari and Krithika PM, MacDermid Alpha Electronics SolutionsEstimated reading time: 2 minutes
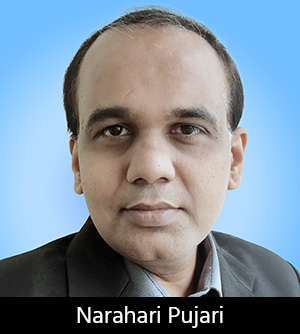
Introduction
The interdigitated back contact (IBC) is one of the methods to achieve rear contact solar cell interconnection. The contact and interconnection via rear side theoretically achieve higher efficiency by moving all the front contact grids to the rear side of the device. This results in all interconnection structures being located behind the cells, which brings two main advantages. First, there is no frontside shading of the cell by the interconnection ribbons, thus eliminating the need for trading off series resistance, losses for shading losses when using larger interconnection ribbons. Second, a more homogeneous looking frontside of the solar module enhances the aesthetics. This combined increased power yield and improved aesthetics make back-contact modules particularly suited for special applications such as vehicle and building integration.
Out of many ways of interconnecting the IBC cells, busbar stringing, which is similar to conventional tabbing and stringing of two-side contacted cells, is the most common method2. In this technique, the metallization design of the cell contains multiple parallel-printed busbars distributed over the cell, allowing shorter finger length, and ribbon on busbar soldering. This reduces the resistance losses in the metallization compared to the edge stringing. With the advent in multibar bar (MBB) technology, the width of these busbars is also reducing and is down to around 300 to 500 microns. The interconnection can be carried out by either ECA (electrically conductive adhesives) or by using direct ribbon/wire. Both materials have created some challenges. The poor peel strength is often the major issue. The uniform IMC (intermetallic layer), which is characteristic of reliable bond strength, is absent with ECA. The metallization paste used in IBC is low-temperature-curing silver paste. The paste is fired at lower temperature around 500°C or less and deposited on silicon cell. In addition to that, the height of the paste is only about 8-12 micron. Because of this, silver leaching during interconnection is commonly observed. The metallization just comes off during interconnection at high temperature. If used, solder wire, cold solder joints, and solder diffusion through the cell are the major issues. Poor adhesion between cell and ECA, and interconnecting wire, high contact resistance are other common problems. Accordingly, when a circuit or conductive layer or interconnection is formed on a substrate using such conventional pastes, damage to the substrate or failure in reliability of the device may occur. Further, when ECA is used, silver in the ECA is expensive and appears on various restricted chemicals lists due its short supply.
To read this entire paper, which appeared in the July 2022 issue of SMT007 Magazine, click here.
Suggested Items
Indium’s Karthik Vijay to Present on Dual Alloy Solder Paste Systems at SMTA’s Electronics in Harsh Environments Conference
05/06/2025 | Indium CorporationIndium Corporation Technical Manager, Europe, Africa, and the Middle East Karthik Vijay will deliver a technical presentation on dual alloy solder paste systems at SMTA’s Electronics in Harsh Environments Conference, May 20-22 in Amsterdam, Netherlands.
SolderKing Achieves the Prestigious King’s Award for Enterprise in International Trade
05/06/2025 | SolderKingSolderKing Assembly Materials Ltd, a leading British manufacturer of high-performance soldering materials and consumables, has been honoured with a King’s Award for Enterprise, one of the UK’s most respected business honours.
Knocking Down the Bone Pile: Gold Mitigation for Class 2 Electronics
05/07/2025 | Nash Bell -- Column: Knocking Down the Bone PileIn electronic assemblies, the integrity of connections between components is paramount for ensuring reliability and performance. Gold embrittlement and dissolution are two critical phenomena that can compromise this integrity. Gold embrittlement occurs when gold diffuses into solder joints or alloys, resulting in mechanical brittleness and an increased susceptibility to cracking. Conversely, gold dissolution involves the melting away of gold into solder or metal matrices, potentially altering the electrical and mechanical properties of the joint.
'Chill Out' with TopLine’s President Martin Hart to Discuss Cold Electronics at SPWG 2025
05/02/2025 | TopLineBraided Solder Columns can withstand the rigors of deep space cold and cryogenic environments, and represent a robust new solution to challenges facing next generation large packages in electronics assembly.
BEST Inc. Reports Record Demand for EZReball BGA Reballing Process
05/01/2025 | BEST Inc.BEST Inc., a leader in electronic component services, is pleased to announce they are experiencing record demand for their EZReball™ BGA reballing process which greatly simplifies the reballing of ball grid array (BGA) and chip scale package (CSP) devices.