-
- News
- Books
Featured Books
- pcb007 Magazine
Latest Issues
Current IssueThe Hole Truth: Via Integrity in an HDI World
From the drilled hole to registration across multiple sequential lamination cycles, to the quality of your copper plating, via reliability in an HDI world is becoming an ever-greater challenge. This month we look at “The Hole Truth,” from creating the “perfect” via to how you can assure via quality and reliability, the first time, every time.
In Pursuit of Perfection: Defect Reduction
For bare PCB board fabrication, defect reduction is a critical aspect of a company's bottom line profitability. In this issue, we examine how imaging, etching, and plating processes can provide information and insight into reducing defects and increasing yields.
Voices of the Industry
We take the pulse of the PCB industry by sharing insights from leading fabricators and suppliers in this month's issue. We've gathered their thoughts on the new U.S. administration, spending, the war in Ukraine, and their most pressing needs. It’s an eye-opening and enlightening look behind the curtain.
- Articles
- Columns
- Links
- Media kit
||| MENU - pcb007 Magazine
Korf and Strubbe: Material Witnesses
October 3, 2022 | I-Connect007 Editorial TeamEstimated reading time: 3 minutes
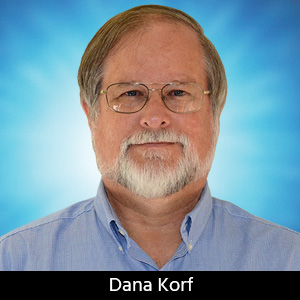
Recently, columnist Dana Korf has been working with Taiwan Union Technology Corporation (TUC), one of the largest providers of copper-clad laminate and mass lamination services in the world. We spoke with Dana about the trends he sees in materials at TUC and around the globe, why copper is still king, as well as some potential non-traditional materials that may see growth soon. Dana invited John Strubbe, TUC VP of technology, to join in the conversation.
Nolan Johnson: Dana, what’s new in the materials world? What are you seeing?
Dana Korf: If you look at straight FR-4, there’s not much going on. There are more high-voltage requirements in the automotive, so there’s a little bit of tweaking of FR-4 to handle voltages around 1,500 or 2,000 volts. Of course, they want long-term reliability, but that’s a relatively minor technical requirement to obtain. With HDI, it’s just a matter of working with thinner glass fabric with the traditional HDI resins, because layers are getting thinner and the number of required lamination cycles increases every year, but that’s more of an adjustment of material properties.
Chip packaging is becoming a constraint. Many companies, like TUC, are now offering chip level packaging materials because there’s just more demand for it than the market can handle. That has a fairly long approval process, just like automotive.
John Strubbe: Most of my work is in low-loss materials for digital. Trying to, as I often say, “get down to free space, no loss,” for the same price as FR-4. There’s a lot of work in copper foil and resins, and a lot of analysis on the glass fabrics. They’re starting to look at quartz again and polymeric materials. They’re trying to get down to really low losses for digital, but the designers are running into the problem that even if you get the losses down to that level, it’s still not good enough. There’s analysis about whether the loss-budget gains you get vs. the cost will be worth it or even possible. That’s what most of the large material folks are working on now. In the RF space, they’re pretty much just working on better controlled RF materials to get the cost down.
Korf: When I was working in China, I was seeing digital designers looking at RF materials to get their losses down. The RF folks were looking at digital performance materials to get the cost down, and that’s still going on. I see that most of the material development work is primarily being driven to reduce the loss, Df, primarily in the digital space. There are umpteen varieties of FR-4, so they seem to be covering the market well; the high voltage for automotive is stressing the specs a little bit, but not too much.
What’s interesting on the material side is we’re starting to look at non-glass alternatives. For example, we’re looking at quartz again, like we did in the 1980s. The problem with quartz glass is that when you hit it with a laser, it melts and balls up. It doesn’t evaporate away. That was a challenge many years ago when we tried it.
Johnson: That makes it tough for laser applications.
Korf: It does make it interesting.
Johnson: What are some of the nontraditional materials being evaluated?
Strubbe: We can talk about the coppers getting down to zero roughness, what’s going on there, and limitations. Does it stick to the resin at the end of the day? Like a lot of technologies, they tend to cycle every 20 or 30 years, and improve with every cycle. Fundamentally, it’s stuff that’s been looked at before.
To read this entire conversation, which appeared in the September 2022 issue of PCB007 Magazine, click here.
Suggested Items
The Evolution of Picosecond Laser Drilling
06/19/2025 | Marcy LaRont, PCB007 MagazineIs it hard to imagine a single laser pulse reduced not only from nanoseconds to picoseconds in its pulse duration, but even to femtoseconds? Well, buckle up because it seems we are there. In this interview, Dr. Stefan Rung, technical director of laser machines at Schmoll Maschinen GmbH, traces the technology trajectory of the laser drill from the CO2 laser to cutting-edge picosecond and hybrid laser drilling systems, highlighting the benefits and limitations of each method, and demonstrating how laser innovations are shaping the future of PCB fabrication.
Day 2: More Cutting-edge Insights at the EIPC Summer Conference
06/18/2025 | Pete Starkey, I-Connect007The European Institute for the PCB Community (EIPC) summer conference took place this year in Edinburgh, Scotland, June 3-4. This is the third of three articles on the conference. The other two cover Day 1’s sessions and the opening keynote speech. Below is a recap of the second day’s sessions.
Day 1: Cutting Edge Insights at the EIPC Summer Conference
06/17/2025 | Pete Starkey, I-Connect007The European Institute for the PCB Community (EIPC) Summer Conference took place this year in Edinburgh, Scotland, June 3-4. This is the second of three articles on the conference. The other two cover the keynote speeches and Day 2 of the technical conference. Below is a recap of the first day’s sessions.
Preventing Surface Prep Defects and Ensuring Reliability
06/10/2025 | Marcy LaRont, PCB007 MagazineIn printed circuit board (PCB) fabrication, surface preparation is a critical process that ensures strong adhesion, reliable plating, and long-term product performance. Without proper surface treatment, manufacturers may encounter defects such as delamination, poor solder mask adhesion, and plating failures. This article examines key surface preparation techniques, common defects resulting from improper processes, and real-world case studies that illustrate best practices.
RF PCB Design Tips and Tricks
05/08/2025 | Cherie Litson, EPTAC MIT CID/CID+There are many great books, videos, and information online about designing PCBs for RF circuits. A few of my favorite RF sources are Hans Rosenberg, Stephen Chavez, and Rick Hartley, but there are many more. These PCB design engineers have a very good perspective on what it takes to take an RF design from schematic concept to PCB layout.