-
-
News
News Highlights
- Books
Featured Books
- design007 Magazine
Latest Issues
Current IssueAll About That Route
Most designers favor manual routing, but today's interactive autorouters may be changing designers' minds by allowing users more direct control. In this issue, our expert contributors discuss a variety of manual and autorouting strategies.
Creating the Ideal Data Package
Why is it so difficult to create the ideal data package? Many of these simple errors can be alleviated by paying attention to detail—and knowing what issues to look out for. So, this month, our experts weigh in on the best practices for creating the ideal design data package for your design.
Designing Through the Noise
Our experts discuss the constantly evolving world of RF design, including the many tradeoffs, material considerations, and design tips and techniques that designers and design engineers need to know to succeed in this high-frequency realm.
- Articles
- Columns
- Links
- Media kit
||| MENU - design007 Magazine
Q&A: The Learning Curve for Ultra HDI
October 20, 2022 | Andy Shaughnessy, Design007 MagazineEstimated reading time: 2 minutes
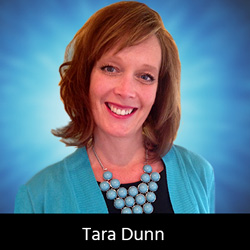
For this issue on ultra HDI, we reached out to Tara Dunn at Averatek with some specific questions about how she defines UDHI, more about the company’s patented semi-additive process, and what really sets ultra HDI apart from everything else. Do designers want to learn a new technology? What about fabricators? We hope this interview answers some of those questions that you may be having about these capabilities and what it could mean for your designs.
Q: How do you define ultra HDI? What is the cutoff in mils or microns?
A: That is an excellent question. At this point I think it means different things to different people depending on where their current HDI capabilities are. IPC has created an ultra HDI working group and I believe the definition they are working with is that to be considered ultra-HDI, a design needs to include one or more of these parameters: Line width below 50 µm, spacing below 50 µm, dielectric thickness below 50 µm, and microvia diameter below 75 µm.
Q: Averatek has developed the A-SAP™ semi-additive process, which can produce traces down into the UHDI space. Can you clear up the differences between mSAP and A-SAP, and what this means to designers and design engineers?
A: In general, SAP, or a semi-additive process, is a process that starts with a very thin layer of copper and then builds the trace patterns from there. One common differentiating factor in these two approaches to SAP is the starting copper thickness. Typically, copper thickness that is 1.5 microns or above would be considered mSAP, or a modified semi-additive process. Because the copper is a little thicker than other SAP processes, it requires more etching, which can have impacts on trace width and space and also the sidewalls of the trace. This process can typically provide features as small as 30 microns in highly specialized facilities that are running extremely high-volume manufacturing. This technology is commonly seen in our smartphones.
Averatek’s A-SAP begins with a much thinner electroless copper, typically 0.2 µm and this copper thickness, or thinness if you will, enables the fabricator to produce much finer feature sizes. The technology is capable of traces and spaces as small as 1 micron if the fabricator has advanced imaging equipment. Typically, PCB fabricators have equipment that can image traces to 12.5 µm today. There are also signal integrity benefits to this process. Because the base copper is so thin, there is minimal impact on the trace sidewalls, and greater control to line width resulting in impedance control tolerance improvements.
One other difference between the mSAP and A-SAP technologies is in the ratio of trace height to trace width; mSAP processes allow a 1:1 ratio of height to width and A-SAP traces can be produced with aspect ratio of 2:1 or greater. For example, a 25 µm wide trace could be 40 µm tall. This has gotten a lot of attention from a signal integrity perspective.
To read this entire article, which appeared in the October 2022 issue of Design007 Magazine, click here.
Suggested Items
The Evolution of Picosecond Laser Drilling
06/19/2025 | Marcy LaRont, PCB007 MagazineIs it hard to imagine a single laser pulse reduced not only from nanoseconds to picoseconds in its pulse duration, but even to femtoseconds? Well, buckle up because it seems we are there. In this interview, Dr. Stefan Rung, technical director of laser machines at Schmoll Maschinen GmbH, traces the technology trajectory of the laser drill from the CO2 laser to cutting-edge picosecond and hybrid laser drilling systems, highlighting the benefits and limitations of each method, and demonstrating how laser innovations are shaping the future of PCB fabrication.
Day 2: More Cutting-edge Insights at the EIPC Summer Conference
06/18/2025 | Pete Starkey, I-Connect007The European Institute for the PCB Community (EIPC) summer conference took place this year in Edinburgh, Scotland, June 3-4. This is the third of three articles on the conference. The other two cover Day 1’s sessions and the opening keynote speech. Below is a recap of the second day’s sessions.
Day 1: Cutting Edge Insights at the EIPC Summer Conference
06/17/2025 | Pete Starkey, I-Connect007The European Institute for the PCB Community (EIPC) Summer Conference took place this year in Edinburgh, Scotland, June 3-4. This is the second of three articles on the conference. The other two cover the keynote speeches and Day 2 of the technical conference. Below is a recap of the first day’s sessions.
Preventing Surface Prep Defects and Ensuring Reliability
06/10/2025 | Marcy LaRont, PCB007 MagazineIn printed circuit board (PCB) fabrication, surface preparation is a critical process that ensures strong adhesion, reliable plating, and long-term product performance. Without proper surface treatment, manufacturers may encounter defects such as delamination, poor solder mask adhesion, and plating failures. This article examines key surface preparation techniques, common defects resulting from improper processes, and real-world case studies that illustrate best practices.
RF PCB Design Tips and Tricks
05/08/2025 | Cherie Litson, EPTAC MIT CID/CID+There are many great books, videos, and information online about designing PCBs for RF circuits. A few of my favorite RF sources are Hans Rosenberg, Stephen Chavez, and Rick Hartley, but there are many more. These PCB design engineers have a very good perspective on what it takes to take an RF design from schematic concept to PCB layout.