-
- News
- Books
Featured Books
- smt007 Magazine
Latest Issues
Current IssueMoving Forward With Confidence
In this issue, we focus on sales and quoting, workforce training, new IPC leadership in the U.S. and Canada, the effects of tariffs, CFX standards, and much more—all designed to provide perspective as you move through the cloud bank of today's shifting economic market.
Intelligent Test and Inspection
Are you ready to explore the cutting-edge advancements shaping the electronics manufacturing industry? The May 2025 issue of SMT007 Magazine is packed with insights, innovations, and expert perspectives that you won’t want to miss.
Do You Have X-ray Vision?
Has X-ray’s time finally come in electronics manufacturing? Join us in this issue of SMT007 Magazine, where we answer this question and others to bring more efficiency to your bottom line.
- Articles
- Columns
- Links
- Media kit
||| MENU - smt007 Magazine
Modern Inventory Management Secrets
November 7, 2022 | Michael Ford, Aegis Software Corp.Estimated reading time: 2 minutes
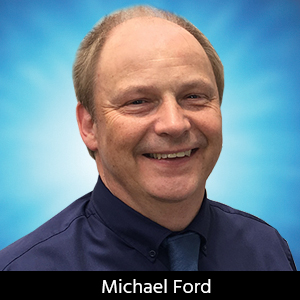
Inventory management should be simple; after all, it is how many of us learned to count. ERP solutions have become complex yet cannot solve our immediate supply-chain and manufacturing challenges unaided. It’s time to unfold the root-causes behind key issues and reveal the secrets for success in modern inventory management which have a significant impact on any manufacturing business.
To understand modern inventory management, we should start at the beginning, which is actually at the end. The aim of the manufacturer is to get rid of completed products as soon as possible. Whether it’s an OEM or EMS company, the customer has agreed on price, so it’s time to get paid and free up that warehouse space. Customers of completed products were once eager to take them into their distribution chain, turning their investment into cash while completing the journey to the final customer. However, once there, products generally depreciate over time, value-wise, whilst still accumulating costs associated with logistics and storage throughout the distribution chain. While this is shorter, it’s an altogether significant threat to profitability.
Distribution chains have now become shorter, designed to cope only with any expected fluctuations in supply and demand. With rampant inflation in many markets—fueled in part by the perceived shortage of products and materials, as well as changing customer demand patterns in many cases—the value of finished goods is appreciating. This is an extremely dangerous condition, as competing vendors now choose their timing for release of product supply based on where and when the pricing is most favorable. On the other hand, prices may suddenly crash as demand falls, confidence fades, and a flood of products come into the market that aim to stay ahead of the trends. Though this is normal practice in the industry, the effects scale considerably with turbulence in the supply-chain.
As usual, the manufacturer is bearing the brunt of this activity, alongside all the other market challenges they face. They are being asked to hold stock and not be paid, without the clear understanding of their customer’s business strategies. Within the manufacturing domain, that is their scope of investment responsibility, inventory cannot be allowed to build up. Production schedules are therefore more often revisited, and quickly adjusted. A production quantity boom-and-bust pattern emerges, with sudden demand, then suddenly, nothing. Though this pattern may be subtle in many cases, it causes a whip-like effect throughout the supply chain. With a keen eye on the level of finished goods, inventory costs, and capacities, production schedules are most effectively optimized on the fly, often using simple, intelligent visual tools to be fulfill commitments, but not waste money on unnecessary semi-finished or finished product stock.
The strengthening of the whip-effect is next seen as the need for raw materials becomes a lot more variable and volatile as compared to original ERP forecasts. This is driven by the need to reduce inventory investment costs and storage space of materials, as well as the risk of obsolescence. It may be driven by the manufacturer’s direct purchasing policy, or from the customer where materials are consigned. In either case, the party with the investment responsibility has the same motivation. As with finished goods, the value of materials would normally depreciate over time, as well as face the risk of obsolescence toward the end-of-life of products and physical degradation during storage. Recently, however, some materials have been appreciating in value, whether due to scarcity or inflation.
To read this entire article, which appeared in the November 2022 issue of SMT007 Magazine, click here.
Suggested Items
It’s Only Common Sense: Selling to Today's Generation of Buyers
06/30/2025 | Dan Beaulieu -- Column: It's Only Common SenseMillennials and Gen Z hold significant purchasing power and influence in industries worldwide. Selling to them requires adapting to their unique preferences, behaviors, and values, and exploring their buying habits, embracing their emphasis on social values, and mastering digital communication. Unlike previous generations, they prioritize experiences, sustainability, and value.
Adeon Technologies Signs Agreement as Distribution and Service Partner for PMT Global
06/13/2025 | Adeon Technologies BVAdeon Technologies has signed an agreement as Distribution and Service partner with PMT Global from Germany for its high precision measurement range of products.
Plexus Issues Fiscal 2024 Sustainability Report
06/06/2025 | PlexusPlexus Corp. released its fiscal 2024 Sustainability Report. The report, which is now available on the company’s Sustainability web page, highlights how Plexus’ commitment to sustainability and innovating responsibly is rooted in its values.
Technica Expands into Emerging Printed Electronics and Advanced Coatings Markets
06/04/2025 | Technica USATechnica is expanding its product portfolio with Agfa’s advanced line of Orgacon conductive coatings. The Orgacon products are a natural complement to Technica’s existing solutions and will allow the company to deliver greater value to customers in these markets.
Tariffs: Hope for the Best, Plan for the Worst
06/04/2025 | I-Connect007 Editorial TeamPaul Krugman received the Nobel Prize for Economics in 2008 for his work in economic geography and identifying international trade patterns. In April, he told the Goldman Sachs Exchanges podcast1, “The secret sauce of the Trump tariffs is that they are extremely uncertain. Nobody knows what they will be. Nobody knows what comes next. Now, if you’re a business trying to make plans, would you want to invest under those conditions?”