-
-
News
News Highlights
- Books
Featured Books
- design007 Magazine
Latest Issues
Current IssueAll About That Route
Most designers favor manual routing, but today's interactive autorouters may be changing designers' minds by allowing users more direct control. In this issue, our expert contributors discuss a variety of manual and autorouting strategies.
Creating the Ideal Data Package
Why is it so difficult to create the ideal data package? Many of these simple errors can be alleviated by paying attention to detail—and knowing what issues to look out for. So, this month, our experts weigh in on the best practices for creating the ideal design data package for your design.
Designing Through the Noise
Our experts discuss the constantly evolving world of RF design, including the many tradeoffs, material considerations, and design tips and techniques that designers and design engineers need to know to succeed in this high-frequency realm.
- Articles
- Columns
- Links
- Media kit
||| MENU - design007 Magazine
Six Money-saving Material Properties When Designing PCB Stackups
March 13, 2023 | Patrick Hope, Siemens Digital Industry Software, Sponsored ContentEstimated reading time: 4 minutes
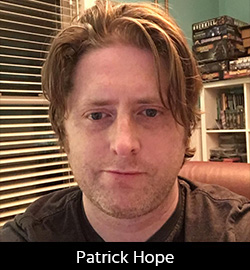
Stackup decisions are critical to every PCB and electronic product, but they don’t always get the attention they deserve. With better stackup planning focusing on six key parameters, designers can select the best materials early in the design process and minimize the risk of under- and overdesigning their PCB.
Dielectric Material Selection
A typical dielectric material sheet will have multiple pages of specs with dozens of parameters for consideration. Cutting through the noise to get to the essence of the material’s properties is hugely beneficial when it comes to material selection. While every spec listed will have a circumstantial purpose, in essence, there are essentially three groups to consider: electrical properties, thermal properties, and mechanical properties.
Many of the mechanical properties like moisture absorption, Young’s Modulus, peel strength, and Poisson’s Ratio are important in specific circumstances. Making concise dielectric material comparisons should focus on six electrical and thermal properties: Dk, Df, Tg, Td, XY-CTE, and Z-CTE.
Video #1: Introduction
Electrical Parameters
Dielectric constant (Dk) and dissipation factor (Df) values are directly related, forming a balancing act within the board as their values directly reflect the ratio between the resin and glass within the material. Understanding the relationship between these electrical parameters and the resin percentage within your material will go a long way toward helping you make decisions about your materials.
Determining the Dk and Df values of your dielectric is usually a straightforward process within any stackup calculator once the loss budget and target thickness have been set, but assessing and assembling these values can be difficult.
Laminate vendors give each resin system a unique datasheet for each resin content available, with values typically listed at 1 Ghz. The Dk and Df values will drift within each option, as the overall resin content will vary. It’s probably easier to view the laminate vendor’s table values than it is to scour all their datasheets. If you are dealing with more than just a handful of materials, the best alternative is to use a materials library which provides these values across multiple resin ratios and with multiple materials and at any frequency.
This goes a long way to simplifying this issue, providing values among multiple resin ratios, as well as at multiple frequencies.
Video #2: Electrical Parameters
Thermal Parameters
When examining the required thermal parameters of your materials, like decomposition temperature (Td) and transition temperature (Tg), PCB assembly is the largest factor. The European Union’s Restriction on the Use of Hazardous Substances (RoHs) directive has had an impact on thermal parameters as the lead-free solder required today has a higher melting point than tin-lead materials, and therefore temperatures during assembly or rework can reach >260°C multiple times. Thicker boards need higher temperatures to bond properly so it’s better to choose high glass-transition-temperature materials and materials with comparatively low z-CTEs for them.
When looking at Tg values, there are three ways to measure what is essentially the same attribute, and vendors will use any one of these ways to measure what is essentially the same data point.
1. Dynamic Mechanical Analysis (DMA)
The best method to use is the dynamic mechanical analysis (DMA) method. It detects changes in the storage modulus and loss modulus (Tg: peak temperature of the tan delta; IPC TM-650 Method 2.4.24.2).
2. Differential Scanning Calorimeter (DSC)
The next best method is differential scanning calorimeter (DSC), which measures the flow of heat into or out of a sample while the sample is heated (Tg: temperature at half height of step change in heat flow; IPC TM-650 Method 2.4.25).
3. Thermomechanical Analysis (TMA)
The last method is thermomechanical analysis, which measures changes in the height of the sample vs. temperature (Tg: temperature where CTE changes; IPC TM-650 Method 2.4.24.24, 2.4.24.5).
If you are designing a thinner board, manufacturers can save 25% or more on material costs by using mid-Tg materials, which can be a critical cost-saver in high-volume production.
Coefficient of Thermal Expansion (CTE)
These values represent the XY coefficient of thermal expansion and the z-axis coefficient of thermal expansion. They are different values and the practical application for this information is different, but the concept behind them is the same.
Excessive x,y (horizontal) expansion caused from high temperatures often leads to misalignment of BGAs, causing solder joint failure, while excessive z-axis (vertical) expansion can lead to barrel cracking.
Video #3: Thermal Parameters
Over Design: The Hidden Cost of Your Board
Being able to locate points of saving within these six material attributes allows you to explore other options and gets you out of your comfort zone, which is where the real savings lie. Improving performance in any one of these values represents an increase in cost from your laminate vendor. Digging deep into your board requirements and understanding where you can cut overall costs can be quite beneficial.
Laminate prices are never advertised, so understanding the relational costs really come from aggregate data from multiple suppliers, or from internal understanding of the pricing structure. Understanding and seeing these cost savings may require working in-depth with your laminate vendors.
Video #4: Over Designing
For more information on material properties, material selection, and building the most cost-effective, robust stackup, please download Stackups: The Design within the Design.
Try a free trial of our Z-planner Enterprise, our powerful stackup planning software. Z-planner Enterprise allows you to evaluate and compare hundreds of dielectric materials and find suggested alternatives based on your board’s requirements.
Suggested Items
Driving Innovation: Direct Imaging vs. Conventional Exposure
07/01/2025 | Simon Khesin -- Column: Driving InnovationMy first camera used Kodak film. I even experimented with developing photos in the bathroom, though I usually dropped the film off at a Kodak center and received the prints two weeks later, only to discover that some images were out of focus or poorly framed. Today, every smartphone contains a high-quality camera capable of producing stunning images instantly.
Hands-On Demos Now Available for Apollo Seiko’s EF and AF Selective Soldering Lines
06/30/2025 | Apollo SeikoApollo Seiko, a leading innovator in soldering technology, is excited to spotlight its expanded lineup of EF and AF Series Selective Soldering Systems, now available for live demonstrations in its newly dedicated demo room.
Indium Corporation Expert to Present on Automotive and Industrial Solder Bonding Solutions at Global Electronics Association Workshop
06/26/2025 | IndiumIndium Corporation Principal Engineer, Advanced Materials, Andy Mackie, Ph.D., MSc, will deliver a technical presentation on innovative solder bonding solutions for automotive and industrial applications at the Global Electronics A
Fresh PCB Concepts: Assembly Challenges with Micro Components and Standard Solder Mask Practices
06/26/2025 | Team NCAB -- Column: Fresh PCB ConceptsMicro components have redefined what is possible in PCB design. With package sizes like 01005 and 0201 becoming more common in high-density layouts, designers are now expected to pack more performance into smaller spaces than ever before. While these advancements support miniaturization and functionality, they introduce new assembly challenges, particularly with traditional solder mask and legend application processes.
Knocking Down the Bone Pile: Tin Whisker Mitigation in Aerospace Applications, Part 3
06/25/2025 | Nash Bell -- Column: Knocking Down the Bone PileTin whiskers are slender, hair-like metallic growths that can develop on the surface of tin-plated electronic components. Typically measuring a few micrometers in diameter and growing several millimeters in length, they form through an electrochemical process influenced by environmental factors such as temperature variations, mechanical or compressive stress, and the aging of solder alloys.