-
-
News
News Highlights
- Books
Featured Books
- design007 Magazine
Latest Issues
Current IssueAll About That Route
Most designers favor manual routing, but today's interactive autorouters may be changing designers' minds by allowing users more direct control. In this issue, our expert contributors discuss a variety of manual and autorouting strategies.
Creating the Ideal Data Package
Why is it so difficult to create the ideal data package? Many of these simple errors can be alleviated by paying attention to detail—and knowing what issues to look out for. So, this month, our experts weigh in on the best practices for creating the ideal design data package for your design.
Designing Through the Noise
Our experts discuss the constantly evolving world of RF design, including the many tradeoffs, material considerations, and design tips and techniques that designers and design engineers need to know to succeed in this high-frequency realm.
- Articles
- Columns
- Links
- Media kit
||| MENU - design007 Magazine
Optimizing Communication Between Fabricators and Designers
March 21, 2023 | Andy Shaughnessy, Design007 MagazineEstimated reading time: 4 minutes
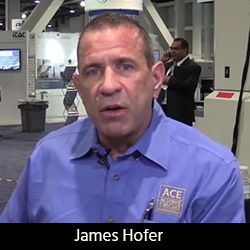
During DesignCon, I spoke with James Hofer from Accurate Circuit Engineering about some of his customers' biggest challenges. We discussed various ways to increase the level—and quality—of communication between designers and fabricators.
James also offered some interesting observations about bridging the gap between designer and fabricator. How often do you communicate with your fabricator?
Andy Shaughnessy: James, you mentioned some of the unique challenges that your customers face. Tell us about their challenges.
James Hofer: We’re doing more phased-array antennas and stacked laser-drilled microvias than ever before, but we’re still having a disconnect between the layout folks and the manufacturer, wherein they forget to stagger the vias; staggering is important. If you stack your microvias directly on top of each other, you risk intersection separation, which means when the vias heat up, they crack open at the interface between vias and the break the connection; when they cool down, they reconnect. This is caused by Z-axis expansion due to the mismatch of CTEs of the copper plating and the epoxy via fill. There are two methods of mitigating this phenomenon: copper filling the vias that are being stacked, and staggering vias slightly off center so that the stacked pad hits the pad at the via underneath it—not directly onto the hole of the via underneath. That will help with the “separation anxiety.”
I also run into designers who stack the microvias, but they’ll leave an artifact in their layout as a through-hole. If it’s not caught by them, it may also not be caught in a typical manufacturer’s DRC and we may see that as a drilled hole and not a stacked laser. If we don’t catch that, then we find ourselves trying to drill through stacked microvias, which could scrap the build. I had a rather big customer almost go through that. I spent half the day here on a conference call with them. But every customer’s task is important. I would prefer to spend a little time with them while they’re doing the layout or the designing of the boards to help them understand why we do what we do.
It’s one thing just to tell customers, “You have to do it this way.” But it’s more important for them to understand why they should do it and what problems it could cause if one decides not to. If somebody doesn’t want to listen to us, that’s fine, but discuss it with us so we can put steps in place to mitigate the issues that arise by not doing it.
Shaughnessy: Most PCB designers have been doing this at least 30 years. Why is there still a communication gap between designers and fabricators?
Hofer: There always has been a bit of a separation between the electrical engineer, the designer, and the manufacturer. Everybody feels as though they know the right way to do this, and you can get in a certain groove with subject matter experts. You might have a longtime manufacturer who knows exactly how to make your boards robust enough to work right every time, but then you switch manufacturers and they don’t know what you’re doing. They’re not used to you doing it this way or that way, so they don’t put in the steps to make sure things are as robust as possible.
Unfortunately, a lot of fabricators say, “This is the way to note it because this is the way we do it.” When we do a DFM with a customer, we suggest that they know the best way to clarify what they want and put that in a language that’s universal to all fabricators, not just one.
Shaughnessy: You’re ensuring that it’s not just tribal knowledge.
Hofer: Right, it should not be tribal knowledge. Maybe you change fabricators because I am busy, or you don’t like my price and you go away for a little while. I don’t want you telling the other fabricator, “It turns out that James only told us the way ACE does it, so I didn’t know that we needed to state our requirements that way.”
Someone just mentioned to me that a few fabricators have an online tool they can use to generate Gerbers. But I told him that they’re not really Gerbers; they’re proprietary software tools for that fabricator. I said, “If you go somewhere else, they won’t be able to use these files, and now you’re locked into that fabricator unless you pay for new Gerbers” That’s not good. I believe designers should be given as much information as possible, whether they stay with a particular manufacturer or not. I believe that we as manufacturers have a responsibility to help designers have knowledge of not only the particular manufacturers nuances but also if industry standards, so they might carry that knowledge with them no matter where they have there project built.
Shaughnessy: Either way, they’ll still remember that you tried to help them and not just nickel and dime them to death.
Hofer: That’s right. One more thing, and I don’t know if it’s a good or a bad habit, but we ask a million questions, always clarifying what we’re doing. This goes back to what I said at the beginning: “Don’t just understand what we do, but why we do it.” Then they can decide, “You know what? We’re not worried about that.” Give them the information so they can decide for themselves. If they go to another fabricator, they might find that fabricator doesn’t work like we do.
Shaughnessy: Well, that’s good stuff. Any closing thoughts?
Hofer: I’m glad to be here at DesignCon. I’m glad to see everyone getting back on the road again.
Shaughnessy: Great talking to you, James.
Hofer: Thanks for coming by.
Suggested Items
The Evolution of Picosecond Laser Drilling
06/19/2025 | Marcy LaRont, PCB007 MagazineIs it hard to imagine a single laser pulse reduced not only from nanoseconds to picoseconds in its pulse duration, but even to femtoseconds? Well, buckle up because it seems we are there. In this interview, Dr. Stefan Rung, technical director of laser machines at Schmoll Maschinen GmbH, traces the technology trajectory of the laser drill from the CO2 laser to cutting-edge picosecond and hybrid laser drilling systems, highlighting the benefits and limitations of each method, and demonstrating how laser innovations are shaping the future of PCB fabrication.
Day 2: More Cutting-edge Insights at the EIPC Summer Conference
06/18/2025 | Pete Starkey, I-Connect007The European Institute for the PCB Community (EIPC) summer conference took place this year in Edinburgh, Scotland, June 3-4. This is the third of three articles on the conference. The other two cover Day 1’s sessions and the opening keynote speech. Below is a recap of the second day’s sessions.
Day 1: Cutting Edge Insights at the EIPC Summer Conference
06/17/2025 | Pete Starkey, I-Connect007The European Institute for the PCB Community (EIPC) Summer Conference took place this year in Edinburgh, Scotland, June 3-4. This is the second of three articles on the conference. The other two cover the keynote speeches and Day 2 of the technical conference. Below is a recap of the first day’s sessions.
Preventing Surface Prep Defects and Ensuring Reliability
06/10/2025 | Marcy LaRont, PCB007 MagazineIn printed circuit board (PCB) fabrication, surface preparation is a critical process that ensures strong adhesion, reliable plating, and long-term product performance. Without proper surface treatment, manufacturers may encounter defects such as delamination, poor solder mask adhesion, and plating failures. This article examines key surface preparation techniques, common defects resulting from improper processes, and real-world case studies that illustrate best practices.
RF PCB Design Tips and Tricks
05/08/2025 | Cherie Litson, EPTAC MIT CID/CID+There are many great books, videos, and information online about designing PCBs for RF circuits. A few of my favorite RF sources are Hans Rosenberg, Stephen Chavez, and Rick Hartley, but there are many more. These PCB design engineers have a very good perspective on what it takes to take an RF design from schematic concept to PCB layout.