-
- News
- Books
Featured Books
- smt007 Magazine
Latest Issues
Current IssueWhat's Your Sweet Spot?
Are you in a niche that’s growing or shrinking? Is it time to reassess and refocus? We spotlight companies thriving by redefining or reinforcing their niche. What are their insights?
Moving Forward With Confidence
In this issue, we focus on sales and quoting, workforce training, new IPC leadership in the U.S. and Canada, the effects of tariffs, CFX standards, and much more—all designed to provide perspective as you move through the cloud bank of today's shifting economic market.
Intelligent Test and Inspection
Are you ready to explore the cutting-edge advancements shaping the electronics manufacturing industry? The May 2025 issue of SMT007 Magazine is packed with insights, innovations, and expert perspectives that you won’t want to miss.
- Articles
- Columns
- Links
- Media kit
||| MENU - smt007 Magazine
Automation and Flexibility: Essential Components for Future-thinking EMS Companies
March 29, 2023 | Norihiro Koike, Saki CorporationEstimated reading time: 3 minutes
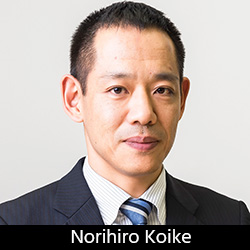
The near future for electronics manufacturing services is all about automation and flexibility. Three key factors affect EMS companies today: the high cost of labor, maintaining a reliable supply chain, and an increasingly high variety of products being manufactured. Quality trained personnel are essential and the supply of both product components and machine parts must remain stable despite a difficult geopolitical situation.
EMS providers in Europe and the U.S. continue to lead technologically, with manufacturers in China rushing to follow. The situation in China is changing. Once predominantly a major location for high-volume mass production, there has been a shift to high-end products primarily for domestic consumption, and neighboring countries such as India are moving into the mass-production market. Now, for many traditional high-volume geographies, there is a greater need for customization in EMS manufacturing, with high-mix, low-volume production on the increase.
Saki is upbeat. The challenges for manufacturers are improved when automation and flexibility are given priority. Automation reduces labor-hours, improves both production efficiency and quality, and inspection solution providers are continually working toward offering an entirely automated inspection solution. To this end, solutions are being developed which unify hardware and software, an essential aspect for automation. With standardized hardware, parts management is significantly easier, and costs are lowered in terms of both labor and consumables.
Software consistency means programs and operations are improved; training time and costs are reduced, day-to-day operations are smoother, equipment becomes simpler to use, and productivity increases. Collaborations with major solder print and pick-and-place machine manufacturers have ensured integrated operations and improved efficiency of not just the inspection machine alone, but the entire line.
For EMS companies, the variety of products produced is increasing, and with it comes a demand for greater flexibility in production planning as well as mass-producing the same product. We have entered an era where custom requests are driving the need for flexibility in the production itself. The conventional wisdom of setting specifications for AOI, AXI, and SPI at the time of purchase and simply allowing operations to continue for 10 years unadjusted is being overturned. Flexibility in production forces inspection machines to be flexible, too. It is driving the development for next-generation inspection machines, with models entering the market that allow customers to switch camera heads with ease, without having to change the machine configuration of the line.
As a result, when the manufacturer’s product changes, it is possible to change the resolution of the optical head of the inspection machine to match the inspection object requirements. This interchangeable camera ensures that the product life of the inspection machines is significantly extended beyond the previously typical 10 years. For example, it is currently possible to exchange two models of a camera—an 8 µm model ideal for use with 0201 mm components, and a 15 µm high-speed model—both with an extended height-measurement range; but of course, the latest camera heads will be immediately installable as they are released. This adaptability allows the high-speed 3D inspection of a variety of component types and ensures Saki’s inspection machines are never a bottleneck.
The realization of a highly accurate product platform improves the integrity of inspection. By applying this platform to the entire line, it is possible to reduce user labor-hours while maintaining the high-quality, high-performance results. Further, cost reductions can be achieved after the initial equipment introduction with the flexibility to upgrade, according to the customer’s production situation and quality requirements.
All these sensibilities form the impetus for the development of total line inspection solutions. Available product ranges are increasingly being designed with hardware and software cohesion to provide a full product line quality assurance solution that is low maintenance, future-proof, easy to operate, and integrated with the third-party machines in the process.
The final piece of the puzzle? Artificial intelligence.
AI has become such a focus for many industries, including EMS companies, but understanding how to properly develop AI processes, and where they might be of use, is a significant learning curve for all. A unified product platform design approach can take advantage of AI functionality, improving inspection quality and automation through the addition of advanced intelligent programming.
This is an excerpt of the original article which appears in the March 2023 issue of SMT007 Magazine. It was just getting interesting...continue reading here.
Suggested Items
Driving Innovation: Direct Imaging vs. Conventional Exposure
07/01/2025 | Simon Khesin -- Column: Driving InnovationMy first camera used Kodak film. I even experimented with developing photos in the bathroom, though I usually dropped the film off at a Kodak center and received the prints two weeks later, only to discover that some images were out of focus or poorly framed. Today, every smartphone contains a high-quality camera capable of producing stunning images instantly.
Hands-On Demos Now Available for Apollo Seiko’s EF and AF Selective Soldering Lines
06/30/2025 | Apollo SeikoApollo Seiko, a leading innovator in soldering technology, is excited to spotlight its expanded lineup of EF and AF Series Selective Soldering Systems, now available for live demonstrations in its newly dedicated demo room.
Indium Corporation Expert to Present on Automotive and Industrial Solder Bonding Solutions at Global Electronics Association Workshop
06/26/2025 | IndiumIndium Corporation Principal Engineer, Advanced Materials, Andy Mackie, Ph.D., MSc, will deliver a technical presentation on innovative solder bonding solutions for automotive and industrial applications at the Global Electronics A
Fresh PCB Concepts: Assembly Challenges with Micro Components and Standard Solder Mask Practices
06/26/2025 | Team NCAB -- Column: Fresh PCB ConceptsMicro components have redefined what is possible in PCB design. With package sizes like 01005 and 0201 becoming more common in high-density layouts, designers are now expected to pack more performance into smaller spaces than ever before. While these advancements support miniaturization and functionality, they introduce new assembly challenges, particularly with traditional solder mask and legend application processes.
Knocking Down the Bone Pile: Tin Whisker Mitigation in Aerospace Applications, Part 3
06/25/2025 | Nash Bell -- Column: Knocking Down the Bone PileTin whiskers are slender, hair-like metallic growths that can develop on the surface of tin-plated electronic components. Typically measuring a few micrometers in diameter and growing several millimeters in length, they form through an electrochemical process influenced by environmental factors such as temperature variations, mechanical or compressive stress, and the aging of solder alloys.