-
- News
- Books
Featured Books
- design007 Magazine
Latest Issues
Current IssueShowing Some Constraint
A strong design constraint strategy carefully balances a wide range of electrical and manufacturing trade-offs. This month, we explore the key requirements, common challenges, and best practices behind building an effective constraint strategy.
All About That Route
Most designers favor manual routing, but today's interactive autorouters may be changing designers' minds by allowing users more direct control. In this issue, our expert contributors discuss a variety of manual and autorouting strategies.
Creating the Ideal Data Package
Why is it so difficult to create the ideal data package? Many of these simple errors can be alleviated by paying attention to detail—and knowing what issues to look out for. So, this month, our experts weigh in on the best practices for creating the ideal design data package for your design.
- Articles
- Columns
- Links
- Media kit
||| MENU - design007 Magazine
Simplifying Simulation and Analysis
April 25, 2023 | Andy Shaughnessy, I-Connect007Estimated reading time: 6 minutes
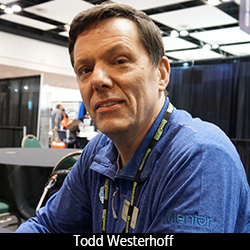
Simulation has always been a critical step in the design process, and it’s only become more critical as design methodologies have become more complex. Gone are the days when simulation meant a simple logic simulation of your circuit, or a basic SPICE run to check signal waveforms. The simulation complexities that are required often fall “above the paygrade” of all but the most experienced members of a hardware design team. So how do you keep simulation from becoming a design bottleneck?
Todd Westerhoff, product marketing manager at Siemens, dives into the discussion with Andy Shaughnessy.
Andy Shaughnessy: Todd, what are some of biggest challenges you hear from your customers?
Todd Westerhoff: Lately we find ourselves asking customers, “What do you do once a board layout is complete, before you send the design out to prototype fab? How do you verify a design is ready for manufacture?” With signal integrity, we talk a lot about what goes into designing a board; the simulations we run to figure out the device placement and signal routing rules that drive physical design. The modeling and simulation process to define those rules can get incredibly detailed—in the end, what comes out of that process are routing rules.
The assumption with routing rules is that board designers will follow the rules completely and accurately. Once PCB layout is complete, what should you do? Take the designer’s word that the rules were followed and not do any checking? It’s fascinating the types of answers we get, but the most common answer is “We bring up the database in a viewer and eyeball it, then build it and test it in the lab.” With the complexity of today’s designs, that’s not optimal.
Shaughnessy: They might have budgeted for re-spins.
Westerhoff: Sure, but as you go faster and the constraints get tighter, the problem is that there are hundreds or thousands of signals on the board that need to follow high-speed rules. But somewhere, somehow, it seems that deviations are required, because the rules can’t be followed explicitly. There’s something in the way like a mounting hole, or the board dimensions have been changes, or the stackup has been modified for some other reason. The point is, the chance that all the rules get followed without exception is fairly small.
In the integrated circuit (IC) space, we wouldn’t even consider taping out an IC without running extensive post-route verification. That would be crazy, given the cost of the die masks. But in the board space, we do it all the time. We spot check a handful of signals with simulation if we simulate anything at all, then we use visual inspection of the board layout to look for possible problems. Visual inspection is problematic—it’s boring and tedious; we get tired, and we make mistakes.
Some customers say, “We don’t have the skills in-house to run modeling and simulation, so we get a contractor to analyze the design.” That approach is expensive, but functional, except - what happens when the contractor comes back with problems that need to be fixed? Are you going to fix those issues and then pay them to analyze the design again? That loop time quickly gets both long and expensive.
Ideally, designers have signal integrity experts in their company that can do the modeling and simulation needed to verify the design. The problem there is, those signal integrity experts are probably already completely overloaded. You know that picture of climbers standing in a long line to get to the top of Mount Everest? That’s probably what it feels like trying to get time from an in-house signal integrity expert.
At Siemens, we’re focused simplifying and automating post-route PCB verification. Verifying all the design’s critical signals after routing is possible with our tools, instead of only verifying a handful of signals, which is what happens with other tools. Full-system post-route verification is a particular strength for Siemens and HyperLynx.
Shaughnessy: If you ask designers, they’ll say you should definitely do it.
Westerhoff: True. But there’s a difference between wanting to do something, or acknowledging it should be done, and actually doing it. We all know we should floss regularly, but how many of us actually do it? The fact is, post-route verification with most signal integrity tools is a tedious and manual process, so most designers limit their efforts to spot-checking, if they simulate at all. We’re focused on automating verification from to back and making the process more accessible to system designers who aren’t full-time signal integrity experts.
At DesignCon 2023, we demonstrated post-route verification of serial links at the full system level. We used a reference design for the fourth generation Intel Xeon processor—a server motherboard that has 336 PCI Express Gen 5 serial channels operating at 32 Gb/s. We showed how to model and simulate every single one of those channels to verify what the operating margin is. This is what we mean by full system, post-route verification.
The odd thing is that PCB signal integrity got its start 30 years ago through post-route verification. Back then, you would lay out the board, simulate your critical signals to find issues and then fix them. As speeds increased, more signals became critical and pre-layout analysis became more important. Post-route verification has faded over time because most tools don’t support it very well, so people have decided it’s just too hard to do. But it still works just fine, and we’re bringing it back.
The question has become – how can we make analysis available to the broader community, and make it practical for people who aren’t full-time signal integrity experts? The trick is identifying specific simulation flows that will help hardware designers make design tradeoffs and verify them. You offer those analytical flows in an “easy” mode—sort of the analytical equivalent of an airplane’s autopilot. You make it possible for hardware designers to those analysis flows themselves.
You have to be practical: signal integrity can be complicated, and when you offer simpler analysis flows that designers can run themselves, eventually those designers will run into a problem where they get stuck. How do they get unstuck? HyperLynx lets novice and expert users run with the exact same models and data. If a designer runs into a problem using a targeted flow, the expert user can load that same design into full HyperLynx, dig into it, figure out the issue and get the designer going again. We’re trying to create two different use models: one for the everyday user and one for the expert.
Going back to the airplane analogy: I can’t fly a 737 because it’s just too complicated. That said, I can successfully fly and land a simulated 737 with an autopilot and a little help. It’s pretty easy to fly a 737 on autopilot with a little training. But when the going gets rough, the autopilot kicks off and you had better know how to fly that plane on your own. Now clearly, you can’t put an inexperienced pilot in an airplane, but we can give a less experienced user a design tool with simplified analysis flow, with a plan to back them up. Our customers are creating complex, proprietary designs; they’re not about to send their designs to us for debugging. The two-use model approach lets them get support from expert users within their own organization.
Shaughnessy: That’s great. The democratization of signal integrity.
Westerhoff: That’s exactly what we’re trying to do. Many longtime specialists in this field are starting to retire; there simply aren’t enough experts to go around, and the technical issues continue to get more complex. We need to start thinking about different classes of analysis tools for different types of users.
Shaughnessy: Todd, this is a great idea, and it’s all part of “left-shift” as well. Great talking to you, as usual.
Westerhoff: Thanks, Andy.
Suggested Items
Microchip Enters into Partnership Agreement with Delta Electronics on Silicon Carbide Solutions
07/18/2025 | Globe NewswireThe growth of artificial intelligence (AI) and the electrification of everything are driving an ever-increasing demand for higher levels of power efficiency and reliability.
ESD Alliance Reports Electronic System Design Industry Posts $5.1 Billion in Revenue in Q1 2025
07/16/2025 | SEMIElectronic System Design (ESD) industry revenue increased 12.8% to $5,098.3 million in the first quarter of 2025 from the $4,521.6 million registered in the first quarter of 2024, the ESD Alliance, a SEMI Technology Community, announced in its latest Electronic Design Market Data (EDMD) report.
Beyond Design: Refining Design Constraints
07/17/2025 | Barry Olney -- Column: Beyond DesignBefore starting any project, it is crucial to develop a thorough plan that encompasses all essential requirements. This ensures that the final product not only aligns with the design concept but is also manufacturable, reliable, and meets performance expectations. High-speed PCB design requires us to not only push technological boundaries but also consider various factors related to higher frequencies, faster transition times, and increased bandwidths during the design process.
Prague PEDC: Call for Abstracts Deadline July 31
07/16/2025 | Pan-European Electronics Design Conference (PEDC)The second Pan-European Electronics Design Conference (PEDC) will take place Jan. 21-22, 2026, in Prague, Czech Republic. The call for abstracts deadline is July 31. Organized jointly by the German Electronics Design and Manufacturing Association (FED) and the Global Electronics Association PEDC serves as a European platform for knowledge exchange, networking, and innovation in electronics design and development.
The Pulse: Design Constraints for the Next Generation
07/17/2025 | Martyn Gaudion -- Column: The PulseIn Europe, where engineering careers were once seen as unpopular and lacking street credibility, we have been witnessing a turnaround in the past few years. The industry is now welcoming a new cohort of designers and engineers as people are showing a newfound interest in the profession.